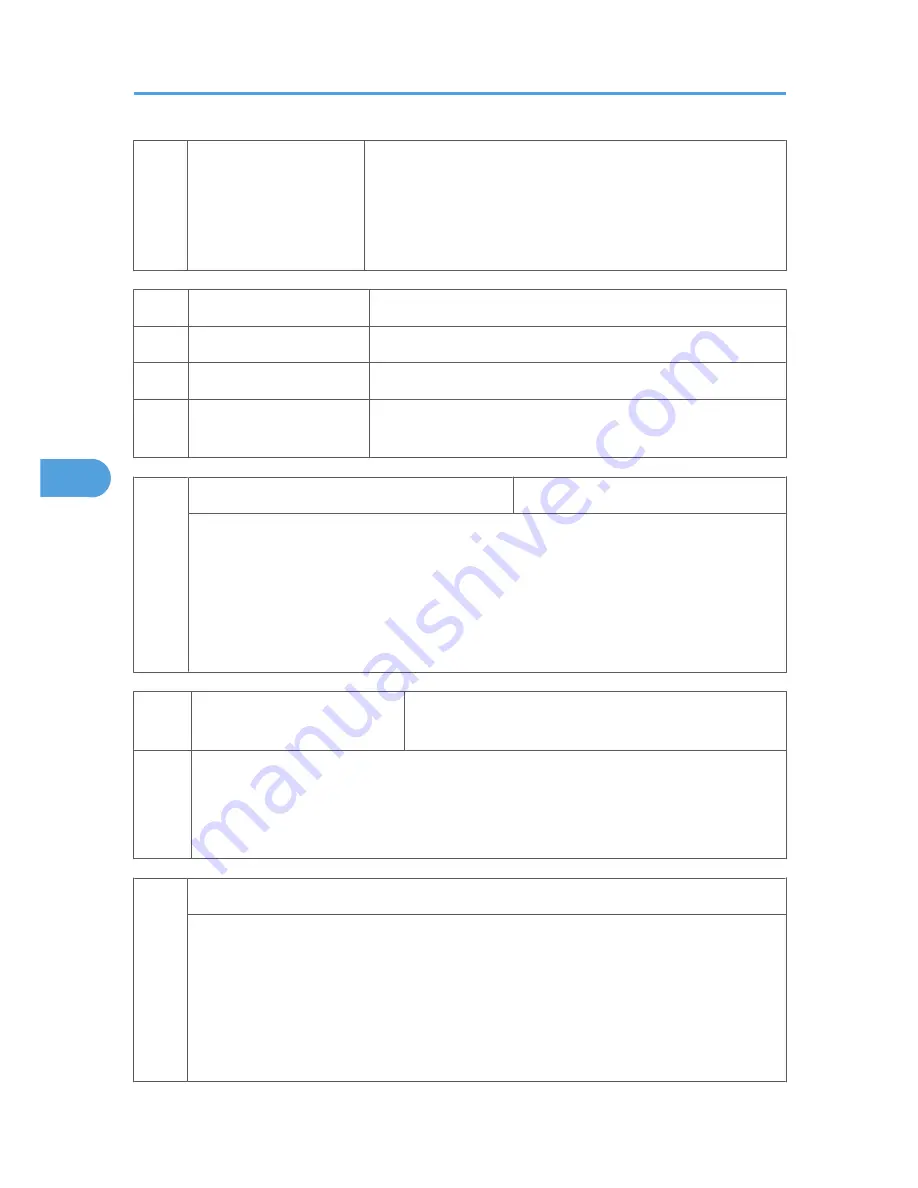
[0
°
C ~ 60
°
C / 5
°
C / 1
°
C step]
When the fusing temperature exceeds this setting, the machine can
operate.
Do not set a reload temperature (Spec. Temp – SP Value) higher
than the SP1105-02 setting.
1106 Fusing T Disp.
Fusing Temperature Display
001 Roller Center
Displays the fusing temperature for the center of the hot roller.
002 Roller Ends
Displays the fusing temperature for the ends of the hot roller.
003 I/O Board Temp.
Displays in the internal temperature of the machine when it was
powered on.
1109
Nip Band Check
Fusing Nip Band Check
This SP sets the machine in the nip band width check mode. The nip width should be 7 mm. You
can increase it by changing the position of the pressure springs (there are two positions only).
If you cannot adjust to the correct value, replace the pressure roller.
[*0=Off, 1=On]
Important! After checking the nip band width, switch off SP1109. If this SP remains on, this will
cause paper to jam in the fusing unit (SC559).
1111
*
Switchback Timing
Paper Reverse Timing Duplex
[+5 ~ –5 / 0 mm / 1 mm step]
Adjusts the reverse timing of paper in the duplex unit (stopping the rotation of the reverse roller
after the trailing edge of the paper passes the duplex entrance sensor).
Adjust the timing if paper frequently jams at the inverter gate in the duplex unit.
1159
Fusing Jam SC Set
This SP setting determines whether SC559 is issued after three paper late jams occur in the fusing
unit. After this SP code is turned on, a counter monitors the number of paper late jams that occur
in the fusing unit. After the 3rd occurrence of a fusing jam, SP559 is issued and the machine
cannot be used until the service technician releases the error.
Note: Switching the machine off/on does not reset this jam counter. The counter is reset after
the cause of the jam has been removed and a sheet of paper successfully passes the fusing exit
sensor.
5. Service Tables
190
5
Содержание A-P4
Страница 1: ...Model A P4 Machine Code G147 SERVICE MANUAL May 12th 2006 Subject to change...
Страница 27: ...Installation Flowchart 1 Installation 26 1...
Страница 32: ...2 Remove the tray full sensor cover 1 x2 x1 3 Insert the loose connector 2 into the hole Bridge Unit B538 31 1...
Страница 59: ...3 Reattach the application cover x1 1 Installation 58 1...
Страница 64: ...Lubrication Lubricate the paper feed clutch gear A with Silicone Grease G501 every PM visit Lubrication 63 2...
Страница 65: ...2 Preventive Maintenance 64 2...
Страница 72: ...Left Covers 1 Left upper cover A x4 2 Controller cover B x2 Covers and Common Procedures 71 3...
Страница 82: ...Laser Unit 81 3...
Страница 103: ...5 Cover C x2 6 Gear D x1 7 Lower paper feed unit E x2 x1 3 Replacement and Adjustment 102 3...
Страница 116: ...Left side 5 Two terminals C x2 6 Center fusing lamp lead D Clamps x3 7 Bracket E x1 Right side Fusing Unit 115 3...
Страница 119: ...5 Springs x2 A both sides 6 Arms x2 B both sides 7 Pawl bracket C x4 3 Replacement and Adjustment 118 3...
Страница 127: ...2 Paper feed unit A x2 x2 3 Rear bracket B x4 x1 bushing x1 4 Paper feed clutch C x1 3 Replacement and Adjustment 126 3...
Страница 128: ...Duplex Unit Duplex Cover Removal 1 Duplex unit cover A x4 Duplex Unit 127 3...
Страница 142: ...IOB 1 Remove the center plate A x1 x1 2 Remove the rear lower cover B x 4 3 Remove the IOB C x 24 x 4 Boards 141 3...
Страница 181: ...4 Troubleshooting 180 4...
Страница 289: ...Self Diagnostic Test Flow 5 Service Tables 288 5...
Страница 303: ...In this machine the development unit is provided with its own motor separate from the main motor 6 Details 302 6...
Страница 306: ...Controller Block Diagram Board Layout 305 6...
Страница 319: ...What Happens When a New Unit Is Detected 6 Details 318 6...
Страница 367: ...6 Details 366 6...
Страница 379: ...MEMO 378...
Страница 380: ...MEMO 379...
Страница 381: ...MEMO 380...