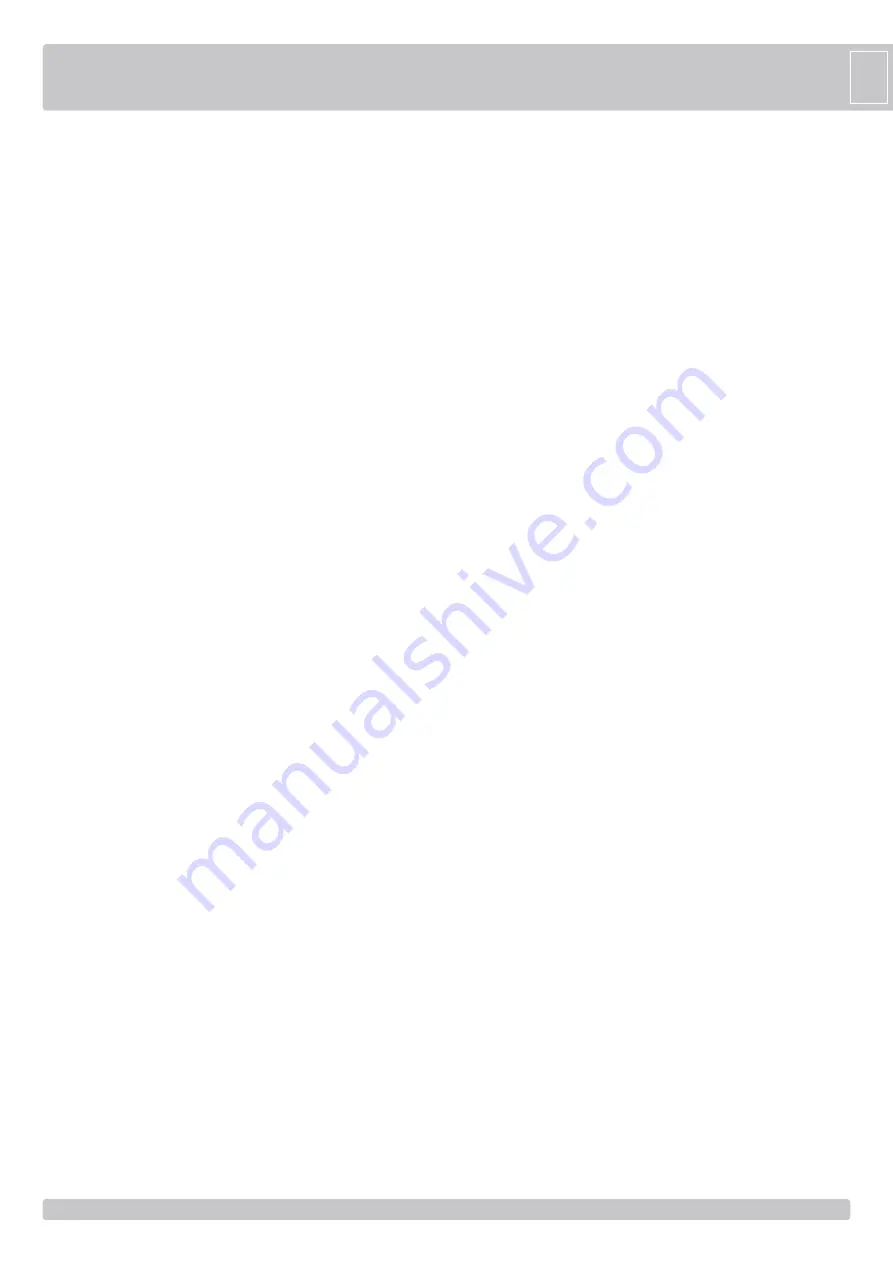
27
27
G
B
Terminal 43-44-45
=> connection 220V traffic lights 2
Terminal 46-47-48
=> remote repetition of traffic lights (neutral switching contact)
Terminal 49-50
=> glass broken emergency pushbutton
Terminal 51-52
=> 220V connection to electronic circuit
Terminal 53
=> not used
Terminal 54
=> ground connection
Terminal 55-56-57-58-59
=> weekly/yearly clock connection
O
RDINARY ROUTINE MAINTENANCE PROCEDURE STOPPER T 275 A:
The standard routine maintenance sequence is as follows:
- Cleaning of pit with suction of all material settlements
- Cleaning of water drains located on the pit bottom
- Cleaning and greasing of the central sliding rail
- Testing (and replacement, if needed) of the lower beat gaskets
- Testing and repair (if required) of the handling piston for oil leaks
- General testing of the pop-up element’s screws for correct tightening
- General cleaning of the driven cylinder and painting touch-ups, if needed
- Testing of the hydraulic station, top-up of oil level and checks over working pressure settings
- Testing and possibly setting of safety pressure switch for proper operation (40 kg)
MOREOVER, IF THE FOLLOWING ITEMS ARE IN THE SYSTEM, PERFORM THE FOLLOWING CHECKS AND TESTS:
- Test the flashlight that is incorporated in the element’s head for proper operation
- Operating test of traffic-lights lanterns
- Operating test of inductive safety turns
- Check over the power failure procedure for proper operation
- Operating test over the control radio receiver
- Operating test of the emergency lowering sound analyser
- Operating test of the remote control GSM effector
- Sight check of the electronic handling management unit (e.g. : “flooded” relay contacts - oxidized clamps - etc.)
I
NSTRUCTIONS TO SET AND REPAIR THE SYSTEM
The STOPPER T bollard has been designed with high reliability criteria and if regular six-monthly maintenance is executed, no further set up is to be
done.
However light impacts of vehicles on the bollard could cause a higher friction during the movement. In this case what follows could be necessary:
-
Set up of the raising force of the bollard:
you need to take the bollard out of the pit, install the test- pressure switch and verify the pressure on
duty (standard 12 BAR); set the screw (in red) on the hydraulic pump up to a max. level of 15 BAR - to make the pressure increase, turn the screw in
clockwise.
- Set up of the pressure switch reversal:
the bollard contains a pressure switch which is ON during raising of the bollard; in case of rush increase of
the pressure of minimum 40 kg (weight of a pedestrian or a vehicle staying on the top of the bollard) the bollard will suddenly stop and lower. In order
to increase or decrease the sensibility of the pressure switch, you need to take the bollard out of the pit, lay a sample 40 kg weight on the top of the
bollard and make sure the pressure switch is working by giving a raising command; if a set up is needed, set the screw on the pressure switch: - to
increase sensibility, turn it in counterclockwise - to decrease the sensibility turn in clockwise.