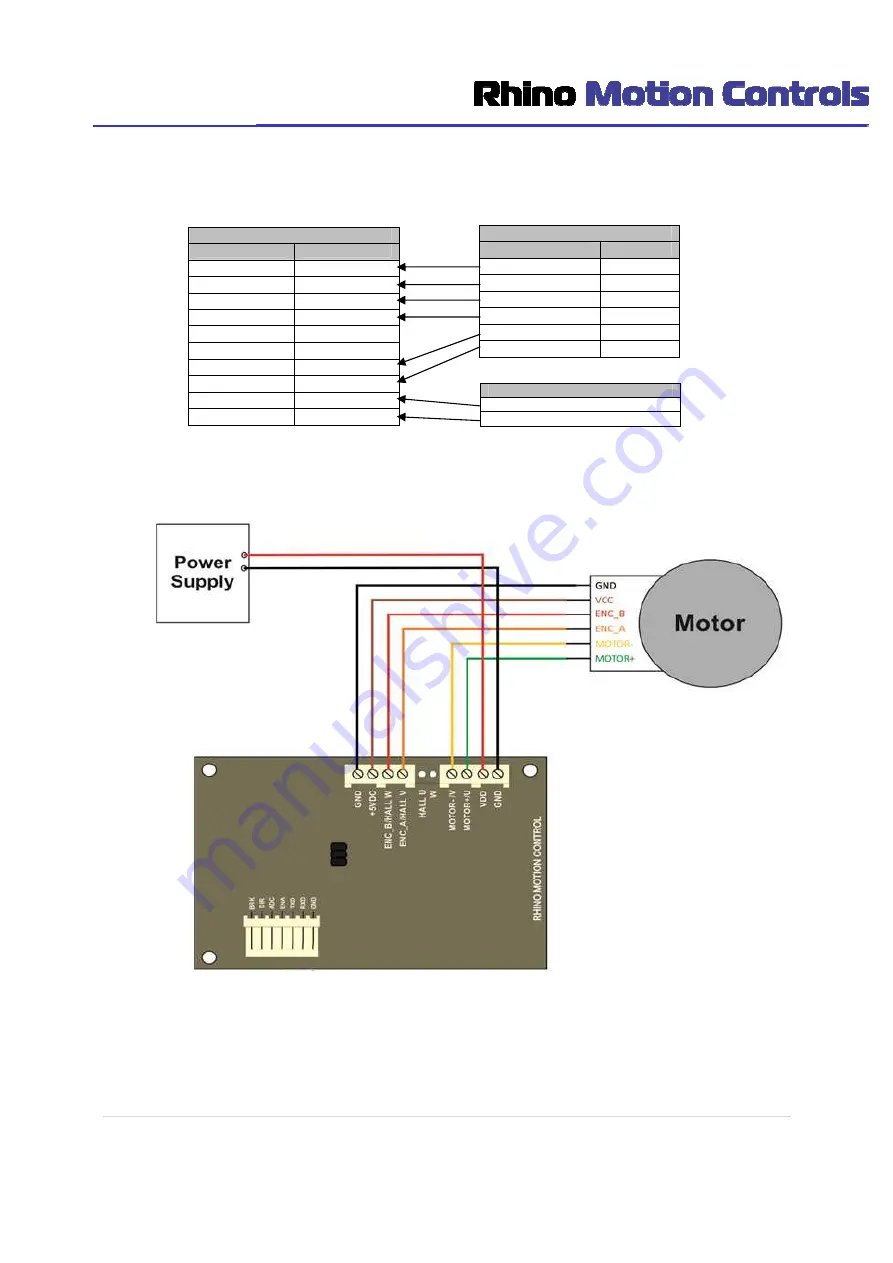
5 |
P a g e
Drive & Motor Connection
Drive Pin outs
Pin No.
Description
8
GND
9
+5VDC
10
ENC_B/Hall W
11
ENC_A/Hall U
12
Hall U
13
W
14
Motor- / V
15
Motor+ / U
16
VDD
17
GND
Motor Pin outs
Motor
Wire Color
GND
Black
VCC(5 V DC )
Brown
ENC_B(Encoder B)
Red
ENC_A(Encoder A)
Orange
M-( Motor-)
Yellow
M+( Motor+)
Green
Power Supply Pin outs
VCC – 10 to 30V
GND