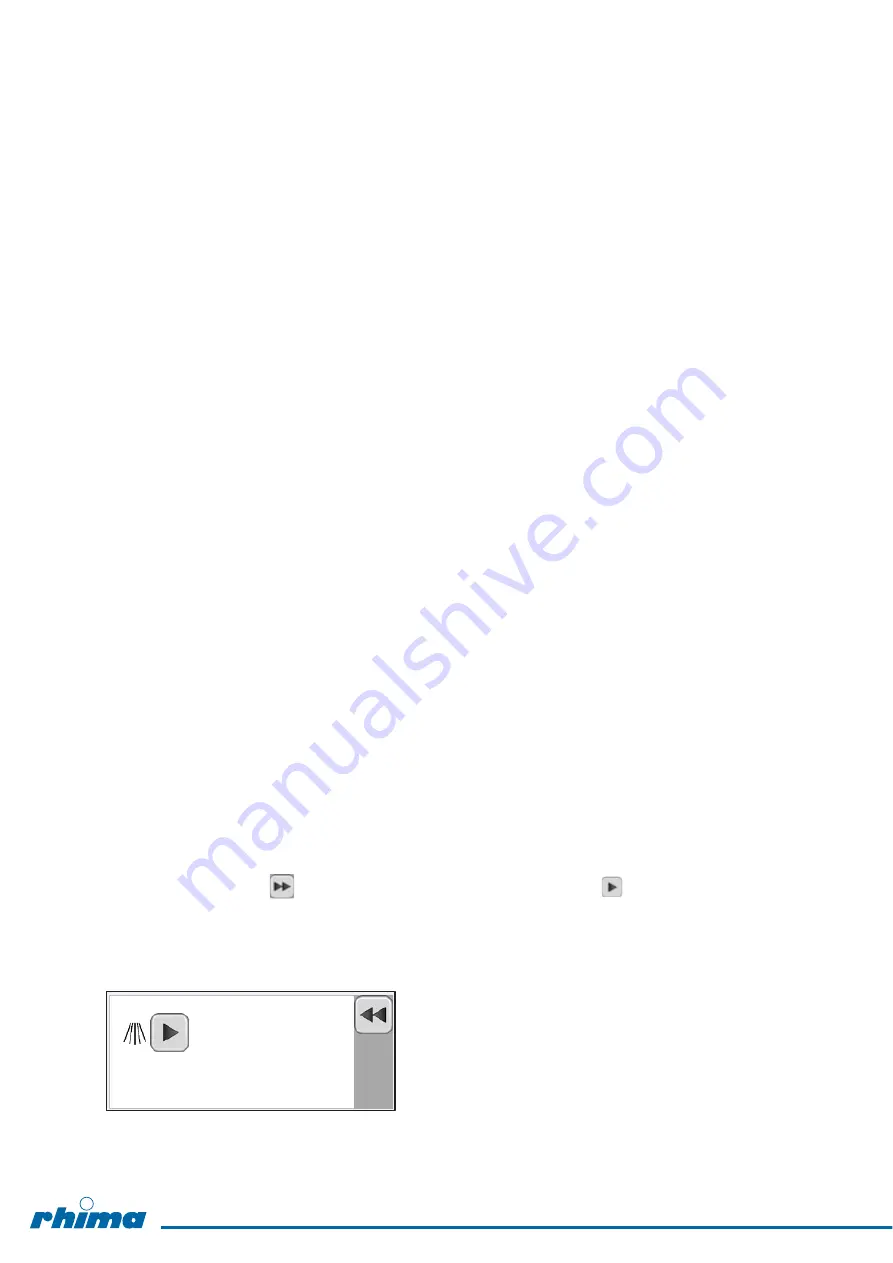
5.8
Purging and disinfecting the WD
All parts of the machine supplying fluids to the load or chamber are purged and disinfected during
a normal operating cycle. The wash chamber and pipework of the machine have been designed
so that any remaining process water shall flow towards the discharge point of the machine.
Should the machine not have been used for a period longer than 24 hours, it is recommended
that a short cycle including disinfection be run before placing a load into the machine for
processing. However, all the cycles validated and sealed by the manufacturer include a
disinfection phase as the last phase of the process.
Service engineers shall pay attention to
the state of the machine before dismantling any parts of the chamber or pipework. Unless
informed otherwise, it shall always be assumed that there may be harmful
microorganisms present by a Fault condition or water system breakdown.
5.9
Methods of cleaning
Daily:
Check that all the sprayers rotate freely and the spray holes are open
In case the fixed or rotating nozzles get blocked the cleaning effect will deteriorate.
Please take care of keeping the nozzles clear
Weekly:
Use a toilet brush and clean the outlet sieve by brushing it a few times
Clean the outer stainless steel panels with diluted washing agent and soft washcloth; flush,
wipe and dry. See also chapter 11.3 (Maintenance manual)
Chamber cleaning: see section 9.7 (Maintenance manual)
5.10 Flushing of chemical dosing systems
To avoid problems in chemical dosing like solidified detergent and blocked piping it’s
very important to flush the system regularly with hot water.
It’s recommended to flush the dosin
g systems every two weeks and always whenever
the detergent container is changed.
Fill a container with hot tap water and put the detergent suction tubes into the container.
In user’s mode press
–
key
to find “Chemical dosing
flush
”
-key . By pressing it the
chemical dosing system can be flushed. Repeat the flushing 3 times.
Put the suction tubes into the detergent container and turn on the pumps once again to
refill the system with the current detergent.
22
Содержание DEKO 190GT
Страница 2: ...2 ...
Страница 10: ...5 1 3 Sequence diagrams Here is a typical curve of DEKO 190 process cycle with main sequences 10 ...
Страница 26: ...26 ...
Страница 28: ...28 ...
Страница 30: ...30 ...
Страница 31: ...APPENDIX 2 USER INSTRUCTIONS 31 ...
Страница 32: ...32 ...
Страница 34: ...34 ...