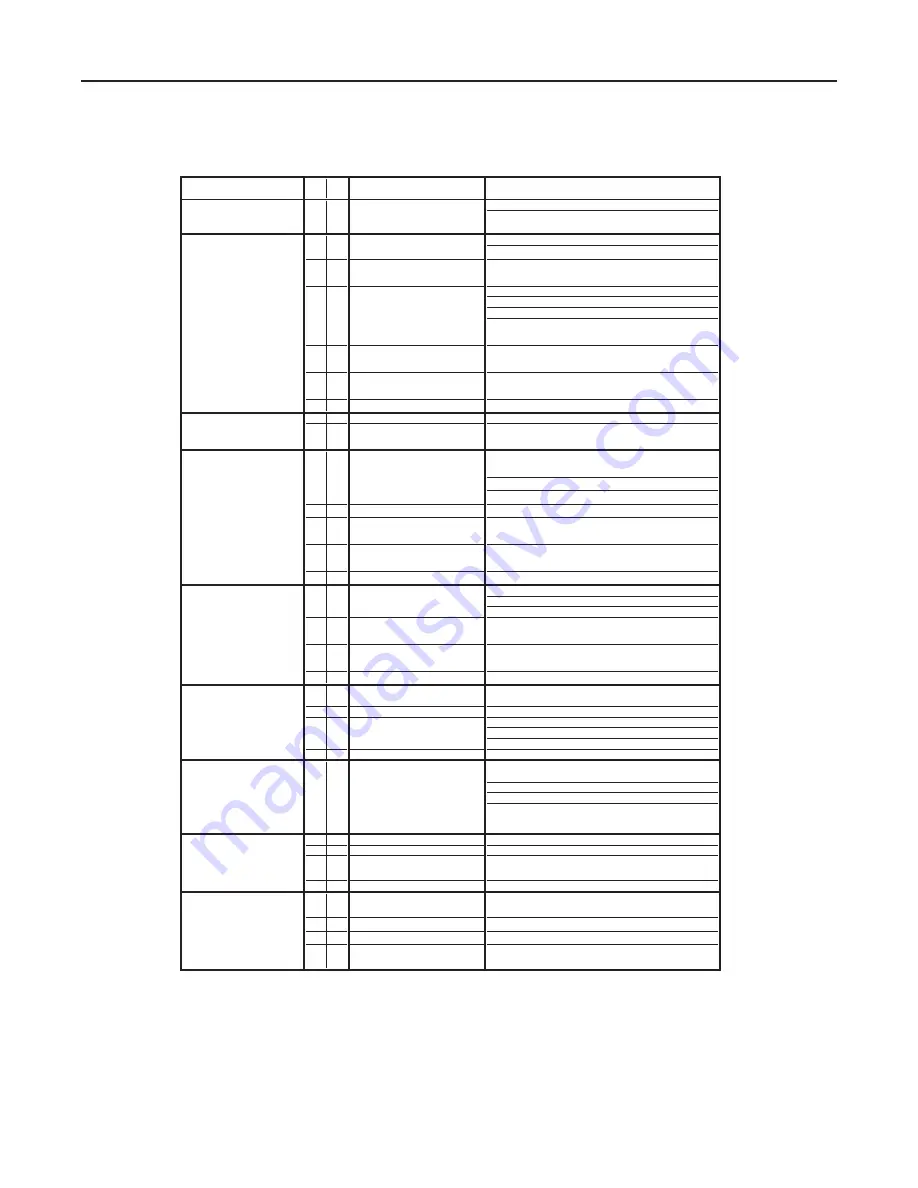
R e s i d e n t i a l S p l i t
R e v. : 1 3 M a r c h , 2 0 1 5
50
Functional Troubleshooting
Fault
Htg Clg Possible Cause
Solution
Main power Problems
Fault Code 27
X
X
Low or no line voltage
Check Line Voltage circuit breaker and disconnect
Check for line voltage between L1 and L2 on the control
board
HP Fault-Code 29
X
Reduced or no water flow
Check pump operation or valve operation/setting
High pressure
in cooling
Check water flow adjust to proper flow rate
X
Water Temperature out of range in
cooling
Bring water temp within design parameters
X
Reduced or no Air flow
Check for dirty air filter and clean or replace
in heating
Check fan motor operation and airflow restrictions
Dirty Air Coil- construction dust etc.
Too high of external static. Check static vs blower table
X
Air Temperature out of range in
heating
Bring return air temp within design parameters
X
X
Overcharged with refrigerant
Check superheat/subcooling vs typical operating condition
table
X
X
Bad HP Switch
Check switch continuity and operation. Replace
LP/LOC Fault-Code 21
X
X
Insufficient charge
Check for refrigerant leaks
Low Pressure/Loss of Charge
X
Compressor pump down at start-
up
Check charge and start-up water flow
FP1 Fault - Code 85
X
Reduced or no water flow
Check pump operation or water valve operation/setting
Water Coil low
temperature limit
in heating
Plugged strainer or filter. Clean or replace.
Check water flow adjust to proper flow rate
X
Inadequate anti-freeze level
Check antifreeze density with hydrometer
X
Improper temperature limit setting
(30°F vs 10°F [-1°C vs -12°C])
Clip JW1 jumper for antifreeze (10°F [-12°C]) use
X
Water Temperature out of range
Bring water temp within design parameters
X
X
Bad thermistor
Check temp and impedance correlation per chart
FP2 fault - Code 86
X
Reduced or no Air flow
Check for dirty air filter and clean or replace
Air Coil low
temperature limit
in cooling
Check fan motor operation and airflow restrictions
Too high of external static. Check static vs blower table
X
Air Temperature out of range
Too much cold vent air? Bring entering air temp within
design parameters
X
Improper temperature limit setting
(30°F vs 10°F [-1°C vs -12°C])
Normal airside applications will require 30°F [-1°C] only
X
X
Bad thermistor
Check temp and impedance correlation per chart
Condensate Fault-Code 25
X
X
Blocked Drain
Check for blockage and clean drain
X
X
Improper trap
Check trap dimensions and location ahead of vent
X
Poor Drainage
Check for piping slope away from unit
Check slope of unit toward outlet
Poor venting. Check vent location
X
Moisture on sensor
Check for moisture shorting to air coil
Under Voltage- Code 09
X
X
Under Voltage
Check power supply and 24VAC voltage before and during
operation.
(Auto resetting)
Check power supply wire size
Check compressor starting. Need hard start kit?
Check 24VAC and unit transformer tap for correct power
supply voltage
Unit Short Cycles
X
X
Dirty Air Filter
Check and Clean air filter
X
X
Unit in "Test Mode"
Reset power or wait 20 minutes for auto exit.
X
X
Unit selection
Unit may be oversized for space. Check sizing for actual
load of space.
X
X
Compressor Overload
Check and Replace if necessary
Only Fan Runs
X
X
Thermostat position
Insure thermostat set for heating or cooling operation
X
X
Unit locked out
Check for lockout codes. Reset power.
X
X
Compressor Overload
Check compressor overload. Replace if necessary.
X
X
Thermostat wiring
Check thermostat wiring at heat pump. Jumper Y and R
for compressor operation in test mode.
Содержание RPVE Series
Страница 2: ......
Страница 55: ...55 Residential Spl i t Rev 13 M arch 2015 Notes...