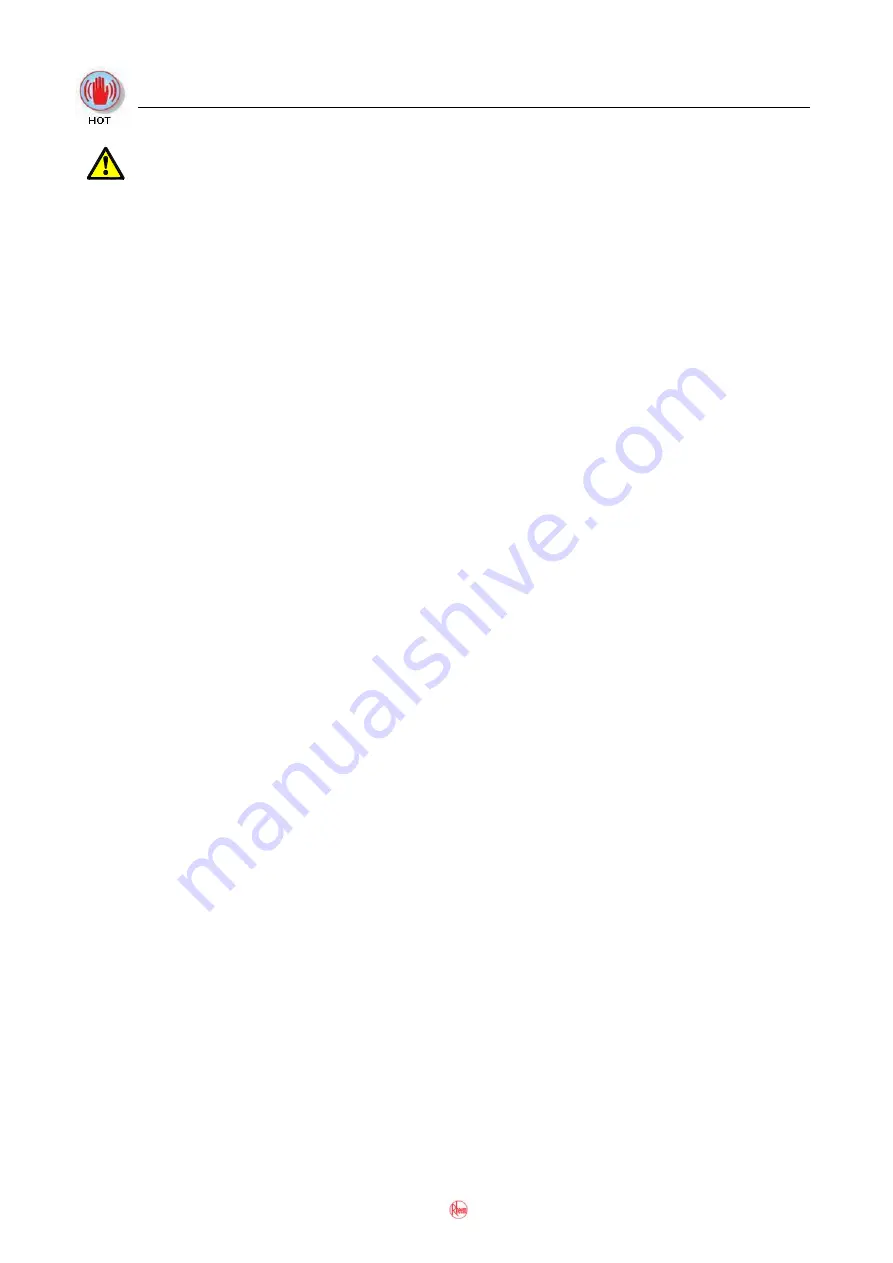
61
This document is stored and maintained electronically by
Service. All printed copies are deemed uncontrolled.
TM077: 325 & 410 Series II Heat Pump Service Instructions
Rev 00: Issued April 2014
Tempering Valve Annual Service Procedure (RheemPlus Models)
A quantity of hot water will discharge from the tank during this process.
Personal Protective Equipment should be worn to prevent scalds or burns.
1. Remove the tempering valve.
Refer to „Tempering Valve (RheemPlus Models)‟ on page
2.
Dismantle and clean or replace hot water inlet filter. The “C” clip and filter can be
removed by gently prising out with a small flat bladed screwdriver. When clean
reassemble by inserting
filter then the “C” clip.
3. Dismantle and clean or replace cold water inlet filter and non-return valve. Unscrew
quick connect fitting and gently prise out filter and then non-
return valve (a “C” clip is
not fitted). Reassemble in reverse order ensuring th
at the “O” ring for the quick connect
fitting is in place. No thread tape is required on the snap lock fitting thread.
4. Screw tempering valve back into heater using thread tape on threaded section.
5. Insert cold pipe into tempering valve quick connect fitting and push up to click pipe into
place (no tool required).
6. Reconnect warm water pipe using thread tape on threaded section.
7. Close hot tap or T&PR valve and restore water supply.
8. Check for leaks.
9. Purge air from the system through hot taps.
10. When tank is full restore electricity.
After servicing the tempering valve the warm water temperature will need to be checked to
ensure correct operation. R
efer to „Tempering Valve Adjustment Procedure (RheemPlus
Models)‟ on page 60.