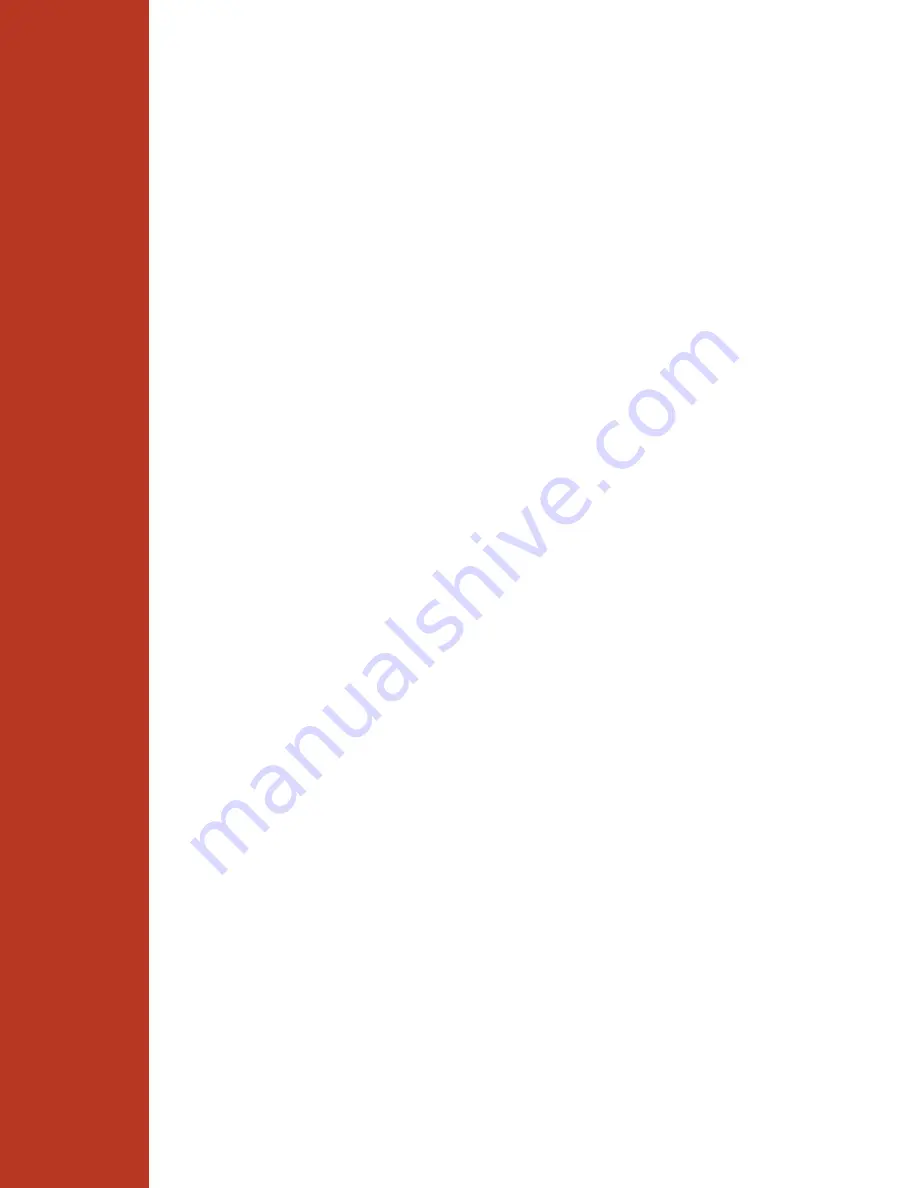
GENERAL INFORMATION
Chain in service will generally wear out before it breaks in
fatigue, if it has been selected properly for the application. For
straight running chains, the normal wear areas are the top
flights and pin joints. Sideflexing chains also wear in this
manner. But sideflexing chain wear life is usually limited by
wear of the reach bar surfaces which contact the corner wear
strips.
Proper chain and wear strip selection will provide optimum
chain and wear strip life. Friction and wear resistance are two
factors which should be considered when selecting a wear strip
material:
1. The lower the coefficient of friction between the chain
and wear strip, the longer the chain life.
2. The greater the wear resistance of the chain and wear strip
materials, the longer the chain life and wear strip life.
Of course, the combination of chain tension, top load, type of
lubrication, abrasion and speed of a given conveyor will govern
the final wear rate of a particular chain-wear strip combination.
The worst condition is high speed, dry operation.
Rexnord has accumulated many years of application
experience as well as laboratory test data on chain-wear strip
compatibility. The following general guide lines will help in the
application of wear strip materials.
See Page 17, Multiflex for specific recommendations.
METAL WEAR STRIPS
Metal wear strips are harder than non-metallics, and in addition
can be heat treated or work hardened to increase hardness.
They are, therefore, suited for applications where abrasive
particles are present either from the environment or from the
products carried. Abrasive particles are less likely to embed in
metal wear strips.
For non-corrosive environments, plain carbon steel. cold
finished, is recommended. For corrosive environments, use
stainless steel, one quarter temper minimum (25. Rc). cold
finish.
STEEL
Plain carbon, cold rolled steel is recommended. Surface finish
should be 32-63 RMS. Use heat treatable grades where
available and hardened to 25-30 Rc. Lubricants used should
have rust inhibitors added.
STAINLESS STEEL
Cold rolled finish (32-63 RMS) is recommended. An austenitic
grade offers the best corrosion resistance.
The softer annealed grades of austenitic stainless steel are
NOT RECOMMENDED, especially with thermoplastic chains.
Interaction between the chain material and the soft stainless
steel might develop. When this happens, the resulting wear
debris consists almost entirely of finely divided stainless steel
particles, nearly black in color, similar to molydisulfide or
graphite. The wear of the stainless steel might be rapid while
the thermoplastic chain by contrast exhibits only slight wear.
Therefore, ONE QUARTER TEMPER (MINIMUM 25 Rc.)
austenitic grade stainless is recommended for use with
any of the chain materials, but especially with
thermoplastic. Martensitic stainless steels can also be
used. They offer excellent wear resistance when heat
treated to 25-35 Rc, but they are not as corrosion resistant
as austenitic.
BRONZE AND BRASSES
These materials are sometimes used with stainless steel
chains. A hard temper material is recommended since a soft
bronze wears rapidly. Typical applications calling for these
metals are those which require non-sparking and anti-static
conditions.
ALUMINUM
Not recommended due to poor wear resistance.
NON-METALLIC WEAR STRIPS
Non-metallic wear strips have a lower coefficient of friction than
metals. They are generally easier to install and remove and
provide for quieter operation. Nylatron
®
is the preferred
material, especially for dry operation at high load or high speed
conditions around corners. Ultra high molecular weight
polyethylene is also recommended for all well lubricated
applications and some dry applications.
ACETAL
Not recommended for use with Acetal chains. It is best not to
run identical plastics together.
Nylatron
®
(nylon with molydisulfide filler) is the preferred
material for dry applications because of its low wear rate and
low friction. It is especially suited for dry operation on
thermoplastic sideflexing chain corners.
Although Nylatron
®
is more stable in wet applications than most
nylons it will absorb moisture and expand. Therefore, room for
expansion must be provided and fasteners must allow for
movement.
ULTRA HIGH MOLECULAR WEIGHT POLYETHYLENE
UHMWP
UHMWP polyethylene (molecular weight of at least 1.0 million)
is recommended for both dry and wet applications on straight
runs. It is also recommended for all well lubricated corners and
non-lubricated corners where chain load and speed are low. It
is NOT RECOMMENDED for dry operation on corners where
the chain load or speed are high.
UHMWP has a wear rate equivalent to nylon in non-lubricated
applications. It is virtually unaffected by moisture and is more
resistant to corrosive chemicals than nylon. It is not as rigid as
cast nylon and may deflect when subjected to high loads from
sideflexing chains.
TEFLON
This material has perhaps the lowest coefficient of friction
available in a plastic wear strip material. It is soft and tends to
flow off the surface and is not practical as a wear strip material
except in low load - low speed applications.
LUBRICANT IMPREGNATED WOOD
Suitable for dry applications where self-lubricating properties of
the material are best utilized. Not recommended for abrasive
conditions where particles may embed in the surface and wear
the chain.
CHAIN AND
WEAR STRIP
COMPATIBILITY
Re
x
®
Multifle
x Chains
MF-15 Rex
®
Engineering Manual
Содержание 1874
Страница 1: ... Rex Engineering Manual ...
Страница 2: ...Rex TableTop Engineering Manual ...
Страница 13: ...Rex MatTop Engineering Manual ...
Страница 35: ...Rex Multiflex Engineering Manual ...