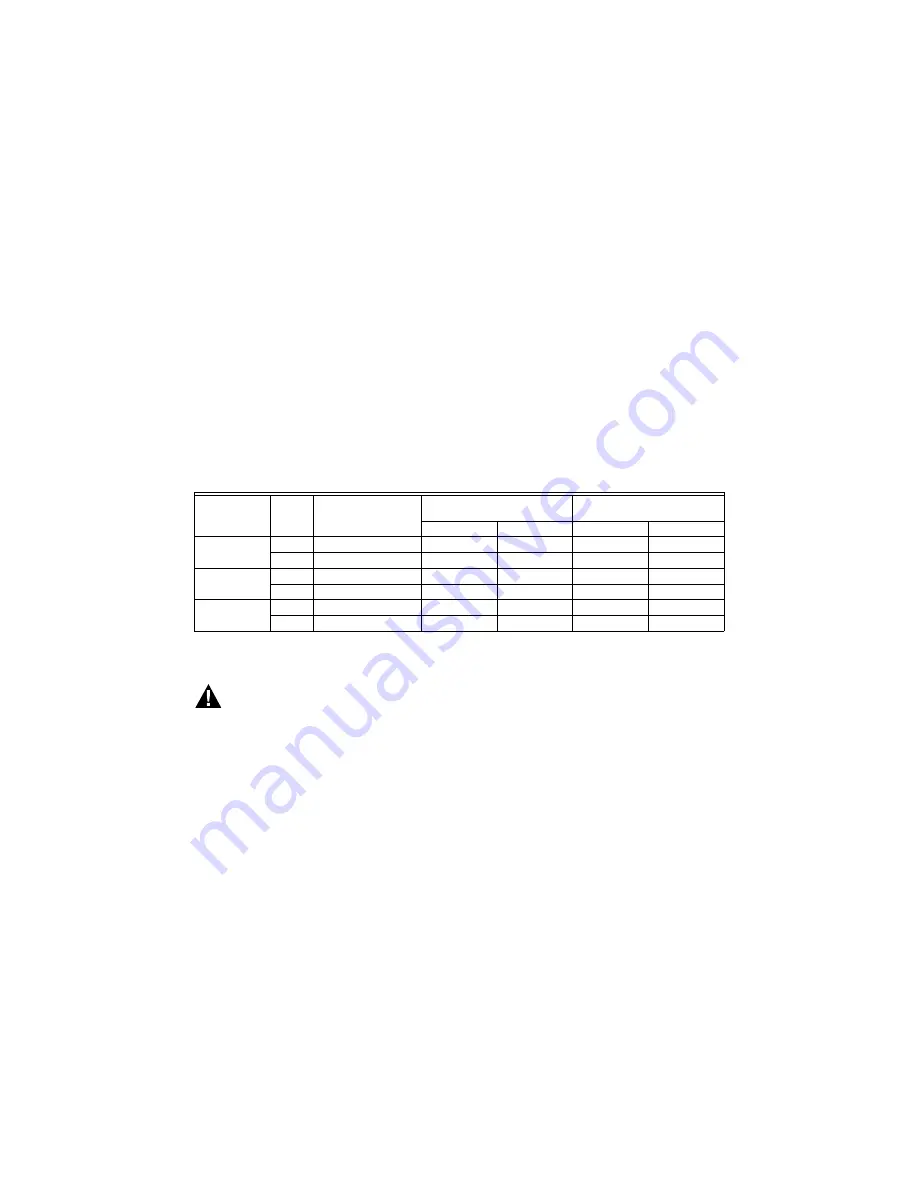
SV9401/SV9402/SV9403, SV9501/SV9502/SV9503, SV9601/SV9602 SMARTVALVE™
11
69-1004—01
1.
Carefully check the main burner lightoff to make
sure the burner lights smoothly and all the ports
remain lit.
2.
Check the manifold pressure listed on the appli-
ance nameplate. The ignition system control full
rate outlet pressure should match this rating.
3.
With the main burner operating, check the ignition
system control flow using the meter clocking
method or check pressure using a manometer con-
nected to the output pressure tap on the ignition
system control.
4.
Adjust the pressure regulator (if necessary) to
match the appliance rating. See Table 8 for factory
set nominal outlet pressure and adjustment range.
a. Remove the pressure regulator adjustment cap
screw.
b. Using a screwdriver, turn the inner adjustment
screw clockwise to increase or counterclock-
wise to decrease the gas pressure to the
burner.
c. Replace the cap screw and tighten firmly to
prevent gas leakage.
5.
If the desired outlet pressure or flow rate cannot be
achieved by adjusting the ignition system control,
check the ignition system control inlet pressure
using a manometer at the inlet pressure tap of the
ignition system control. If the inlet pressure is in
the nominal range (Table 8, replace the ignition
system control. Otherwise, take the necessary
steps to provide proper gas pressure to the control.
6.
Carefully check the burner lightoff at step pressure
to make sure the burner lights smoothly, without
flashback to the orifice. Make sure all ports remain
lit.
7.
Cycle the burner several times, allowing at least 60
seconds between cycles for the regulator to
resume the step function.
8.
Repeat steps 6 and 7 after allowing the burner to
cool.
9.
Readjust the full rate outlet pressure (if necessary)
to improve lightoff characteristics.
Convertible (R) Models
Models with convertible (NAT/LP) regulators, used for
mobile home applications, are not field-adjustable. Do
not attempt to adjust outlet pressure on these controls.
Use the instructions in this manual for changing between
LP and natural gas.
Table 8. Pressure Regulator Specification Pressures in. wc (kPa).
MAINTENANCE
WARNING
Fire or Explosion Hazard. Can cause property
damage, severe injury, or death.
Do not attempt to take the control apart or clean
it. Improper cleaning or reassembly can cause
gas leakage.
Regular preventive maintenance is important in
applications such as in the commercial cooking and
agricultural and industrial industries that place a heavy
load on system controls because:
• In many such applications, particularly commercial
cooking, the equipment operates 100,000 to 200,000
cycles per year. Such heavy cycling can wear out the
gas control in one to two years.
• Exposure to water, dirt, chemicals and heat can
damage the gas control and shut down the control
system.
The maintenance program should include regular
checkout of the control as outlined in the Startup and
Checkout section, and the control system as described in
the appliance manufacturer literature. Maintenance
frequency must be determined individually for each
application. Some considerations are:
• Cycling frequency. Appliances that may cycle 20,000
times annually should be checked monthly.
• Intermittent use. Appliances that are used seasonally
should be checked before shutdown and again before
the next use.
• Consequence of unexpected shutdown. Where the
cost of an unexpected shutdown would be high, the
system should be checked more often.
• Dusty, wet, or corrosive environment. Because these
environments can cause the gas control to deteriorate
more rapidly, the system should be checked more
often.
The system should be replaced if:
• It does not perform properly on checkout or
troubleshooting.
• The gas control is likely to have operated for more
than 200,000 cycles.
• The control is wet or looks as if it has been wet.
Model Type
Type of
Gas
Nominal Inlet Pressure
Range
Factory Set Nominal Outlet
Pressure
Setting Range
Step
Full Rate
Step
Full Rate
Standard Slow NAT
5.0-7.0 (1.2-1.7)
–
3.5 (0.9)
–
3-5 (0.7-1.2)
LP
12.0-14.0 (2.9-3.9)
–
10.0 (2.5)
–
8-12 (2.0-3.0)
Step
NAT
5.0-7.0 (1.2-1.7)
0.9 (0.2)
3.5 (0.9)
None
3-5 (0.7-1.2)
LP
12.0-14.0 (2.9-3.9)
2.2 (0.5)
10.0 (2.5)
None
8-12 (2.0-3.0)
Convertible
NAT
5.0-7.0 (1.2-1.7)
–
3.5 (0.9)
None
None
LP
12.0-14.0 (2.9-3.9)
–
10.0 (2.5)
None
None