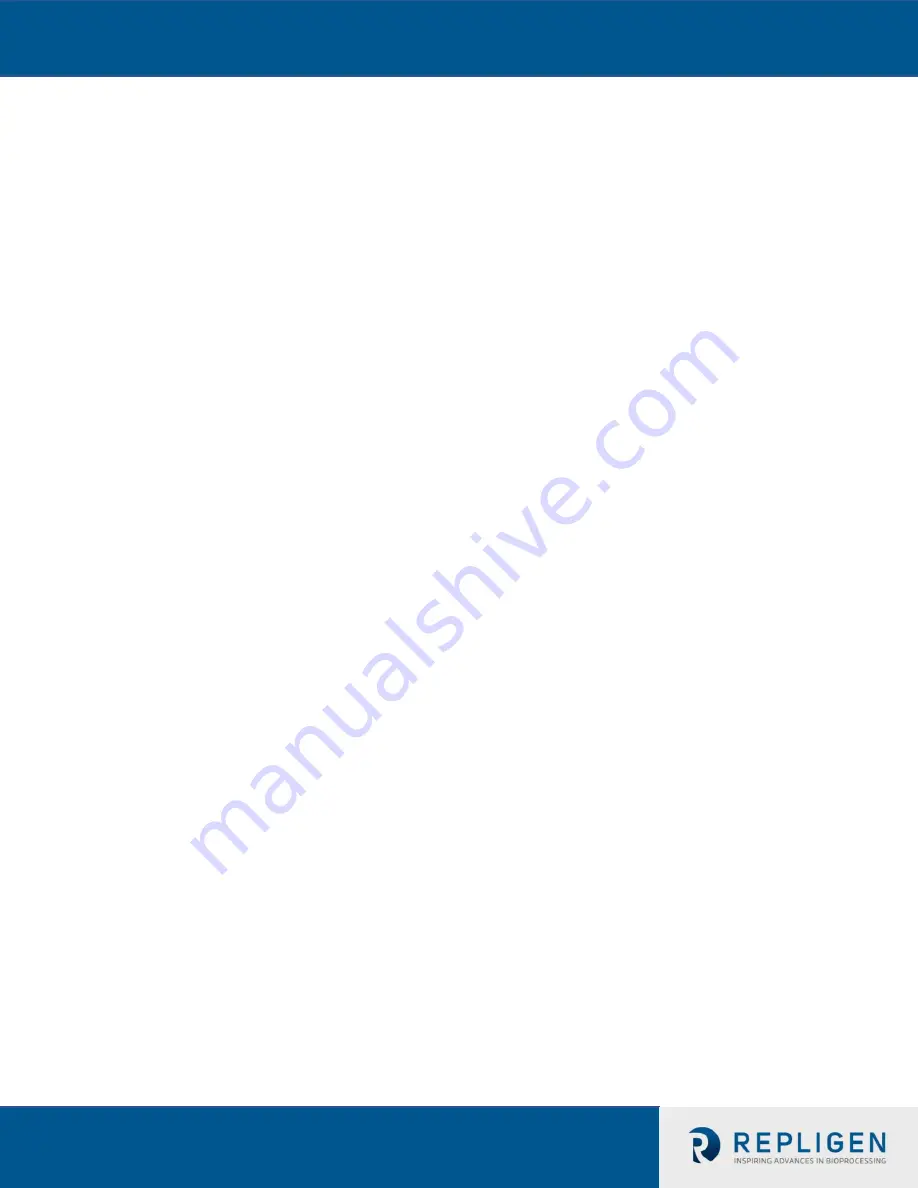
XCell
TM
ATF System with C410:V4B Controller
User Guide
75
Appendix 5: Profibus Communication
The XCell™ ATF
C410v4 controller is capable of remote operation using a Profibus DP slave card that
enables communication to the Profibus DP master (customer). To activate this control mode, the
selector switch on the Administrator screen must be toggled to Profibus.
See section F.2 Basic
Administration Screen (Remote Mode Connection) selector switch
.
1.1
Remote Control Mode
It is possible to set the
XCell™ ATF
to Remote Control Mode from the main screen. With the
control mode set to “Remote”,
the
XCell™ ATF
uses parameters sent from the Profibus master.
When set to “Local” parameters may be entered from the local Human Machine Interface.
Instead of using the onboard HMI (operator interface), the Remote control mode is intended to
allow another operator interface (provided by the end user) to control ATF functions, as well as
receive feedback from the ATF controller regarding the ATF status and data acquisition for
historical purposes.
1.2
Input Signals (from Master to
XCell™ ATF
)
The master, a system with a PROFIBUS interface, for example, sends output data to a slave
device (
XCell™ ATF
) in its configuration, which becomes input for the
XCell™ ATF
controller. The
input signals
from Master to XCell™ ATF
are divided into different pages. The master has to set
a parameter to define which of the pages is being sent,
using the ‘
SendingDataPage
’ parameter
(InputPage0, InputPage1, InputPage2, InputPage3, InputPage4). When the
XCell™ ATF
receives
a new value in
“
SendingDataPage
”
from the Master, a timer is started. After 500ms, the XCell
ATF controller begins copying the values from the Profibus input to the parameters defined in
“
Input Signals (from Master to
XCell™ ATF
)
” tables
(provided the system is in remote control
mode and the selector switch is set to Profibus)
Should a parameter (from the master) be changed without changing page, the value is copied
immediately.
When programming commands to the ATF controller, it is recommended that
“SendingDataPage” value remain at the value of the most recently sent command page, until an
operator interacts with the
master’s user interface, requesting a change to the ATF controller’s
state. Examples include: Remote setup, Remote Start, Remote Stop as discussed below.
Further, it is recommended to set the “SendingDataPage” value to 3 or 4 (for infrequent
calibration commands) only when ATF is not running, and Repligen service personnel
specifically are required to perform calibration activities.
1.3
Output Signals (to Master from
XCell™ ATF
)
The slave device (
XCell™ ATF
) provides output data, which becomes inputs for the master. The
output signals from the ATF are divided into different pages. The master has to set a parameter
to define which of the pages is to be received,
using the ‘Requested
DataPage
’ parameter
(OutputPage0, OutputPage1, OutputPage2, OutputPage3, OutputPage4). When the
XCell™ ATF
receives a new value in
“Requested
DataPage
”
from the Master, the XCell ATF controller begins
copying the values from the parameters
defined in “Output Signals (from XCell™ ATF to
Master)
” tables
to the Profibus outputs.
The Master can continuously cycle (in a recommended 1 second interval) the
RequestedDataPage parameter to receive all the output data from the XCell™ ATF. The