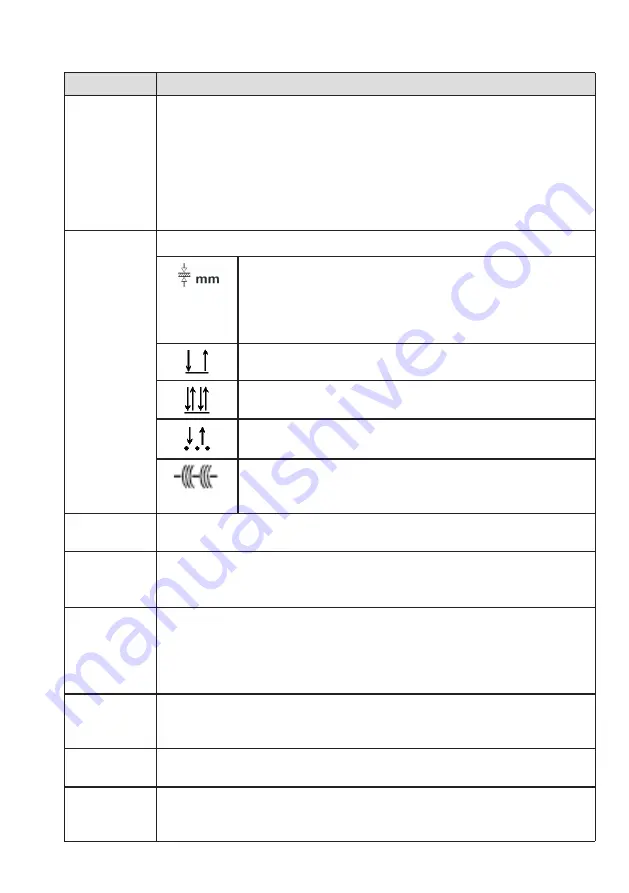
Controls
Function
6
Correktion of wire speed
Fine adjustment for wire speed in addition to the machine calculated
speed by adjustments of you did with the rotary cam switches 11 and
12. The correction value stays active even if you change steps.
Negative correction = reduces wire speed => arc gets longer
Positive correction = increases wire speed => arc gets shorter
If arc energie gets too low and welding result isn‘t convinient you
need to change output voltage by the rotary switches.
7
Mode switch
Auxiliary function to find the right adjustment for a
certein material thickness. 7-Segment indicator 2.
For control reason value of calculated material thickness
is show shortly when activating the torch button.
If arc is astablished indicator show welding current.
2-Step mode
4-Step mode
Spot welding - time adjust with potentiometer 8
Pulse welding - Interval welding
Pulse time can be adjusted with regulator 8,
the pause time is half the pulse time.
8
Time setting
for functions spot and pulse welding [0.1 ... 5.0 sec]
9
Material selection switch
Selection of material like aluminium, copper (CuSi3), steel and stain-
less steel (CrNi) and wire thickness like 0.8, 1.0, 1.2 mm
10
SDI adjustment
Stepless adjustable DC choke to allow hard or soft welding arc.
If potentiometer is in the left stop position Automatic SDI is switched
on. Now application controller is calculating adjustment according to
position of rotary switches.
11
Rotary cam switch - coarse adjustment
Not available in all products. Big increase of output voltage and
welding current.
12
Rotary cam switch - fine adjustment
Stepwise increase of voltage and current.
13
FOCUS switch
Arc will be focussed. Available only at products 304, 404 und 504 and
only for steel and stainless steel welding.