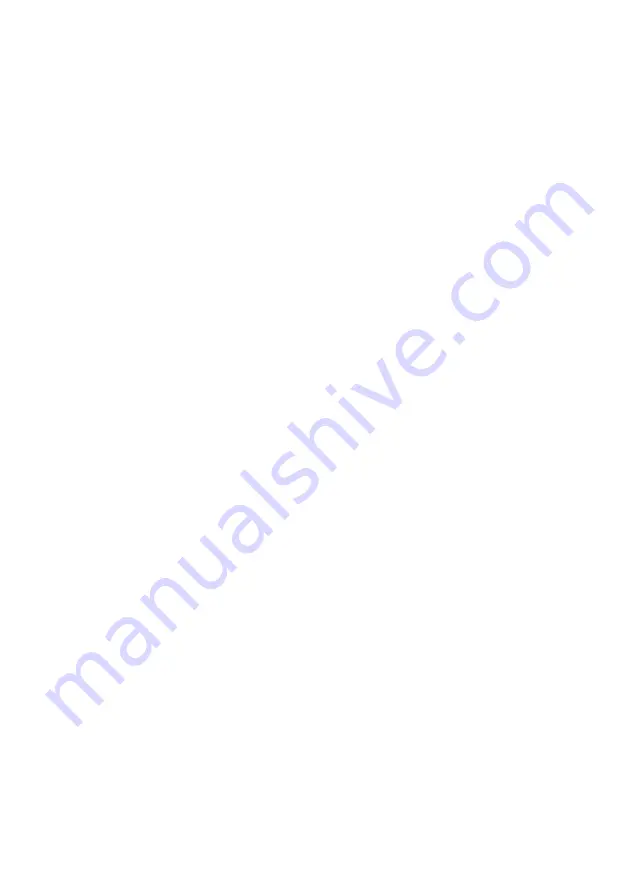
This models of welding power sources have been developed according to the generally
recognized rules of technology. Nevertheless, their use can lead to a risk for life and limb
of the user or third parties or might lead to damages of the system or other property.
You should therefore read this document completely and thoroughly before starting up
the welding machine.
• Safety and warning notices are used for occupational safety and accident prevention.
They must be observed. Not only the general safety instructions listed here must be
observed but also the safety and warning information in the original manual.
• In addition to the information in these brief instructions, the general safety and
accident prevention regulations have to be considered. They differ from country to
country (German: UVV BGV A3, TRBS 2131, BGR 500 Chapter 2.26 „Welding, cutting
and allied processes“). In addition the specific regulations for welding are relevant.
• Please notify also the safety information signs in this document.
• As a matter of principle, no safety devices may be dismantled or put out of operation,
as this poses a risk and the intended use of the system is no longer guaranteed.
Dismantling of safety devices when setting up, repairing and maintaining is specially
described. The safety devices must be reassembled immediately after this work has
been completed.
• Changes to the system, the attachment or installation of additional equipment and
external the use of safety devices is not permitted. This invalidates the guarantee and
the reliability claim.
• If external agents are used (e.g. solvents for cleaning), the operator of the system must
guarantee the safety of the system during use.
• Except when this is expressly stated in writing by REHM, REHM welding systems are
only intended for sale to commercial / industrial users and only for their use.
T
he MIG/MAG welding systems are designed according to EN 60974-1 arc welding
equipment - welding power sources for overvoltage category III and pollution degree 3
and according to EN 60974-10 arc welding equipment - electromagnetic compatibility
(EMC) for group 2 class A and are suitable for use in all areas , except residential areas
that are directly connected to a public low-voltage supply system. Both conducted and
radiated interference can make it difficult to ensure electromagnetic compatibility in
these areas. For this purpose, the observance of suitable measures to meet the require-
ments (filters for mains connection, shielding such as the use of shielded lines, welding
lines that are as short as possible, earthing of the workpiece, equipotential bonding) as
well as the assessment of the environment (such as computers, control equipment,
sound and television broadcast transmitters, neighboring Persons, e.g. when using a
pacemaker). The user is responsible for faults.
Qualification of the operating personnel
REHM welding systems may only be used by persons who are trained in the use,
operating and maintenance of the welding systems.
Only qualified, authorized and instructed personnel may work on and with the systems.
1 Safety Instructions