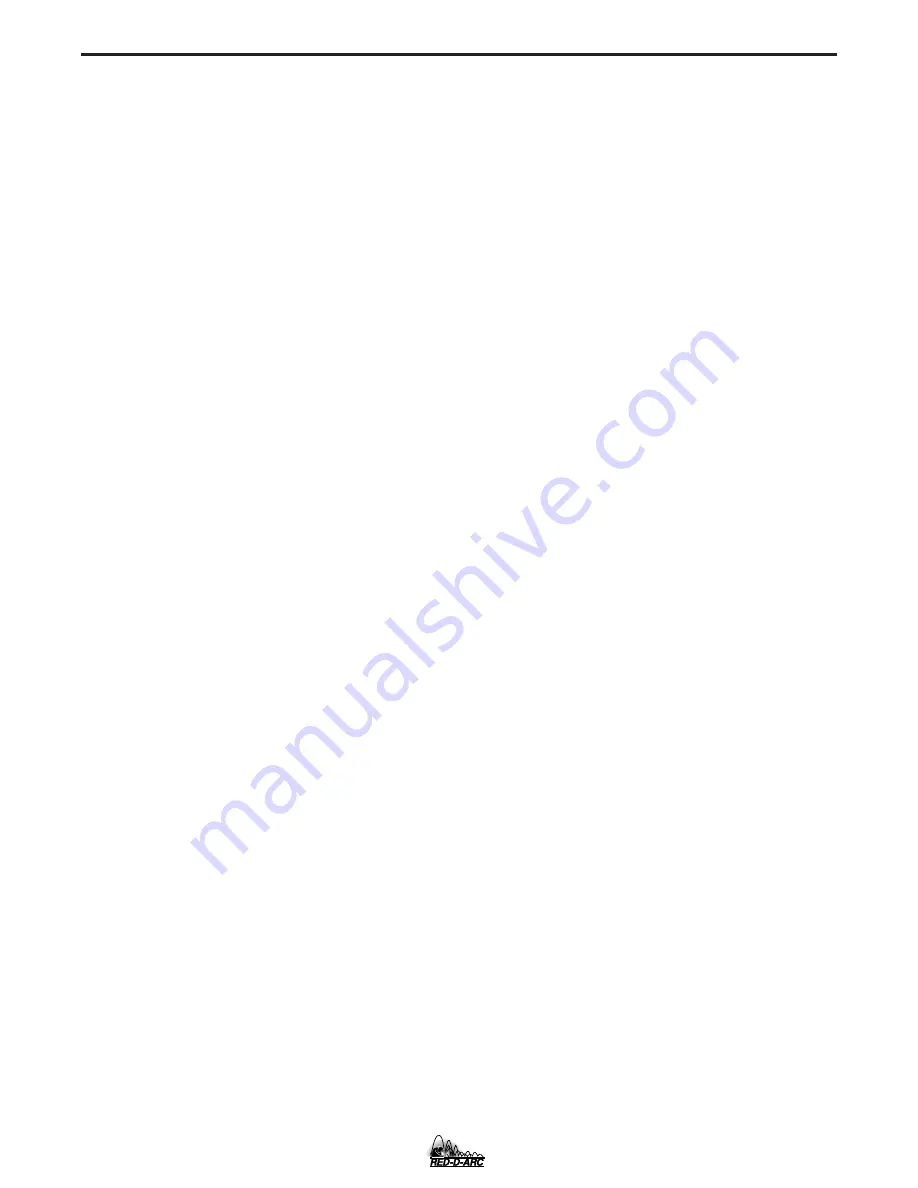
B-3
OPERATION
B-3
•
The Arc Control regulates the relative Slope of the
process. Slope dynamically controls the force the
arc has to penetrate an open root. At the minimum
setting, Arc Control is very soft and is similar to the
Stick Soft mode. At the maximum setting, the slope
is reduced, the OCV is reduced, and the operator
has full control off the arc force required to pene-
trate an open root joint. For vertical down, open root
pipe welding applications, the recommended setting
is between 8 and 10.
•
During welding, a boost circuit increases the avail-
able voltage to minimize pop outs. The boost circuit
is independent of the OCV and only operates when
an arc is lit.
TIG GTAW: The TIG mode features continuous con-
trol from 5 to 425 amps. The TIG mode can be run in
either the TIG touch start or high frequency assisted
start mode.
•
The Hot Start control selects the starting mode
desired. A setting of less than 5, the TIG lift start
mode is selected. The OCV is controlled below 10v
and the short circuit "TIG touch" current is main-
tained at 25 amps independent of the preset cur-
rent.When the tungsten is lifted, an arc is initiated
and the output is regulated at the preset value. Hot
start settings between 0 and 5 regulate the arc initia-
tion current. A setting of 5 results in the most positive
arc initiation. A setting of 0 reduces hot start.
•
Hot Start settings between 5 and 10, select high fre-
quency assisted starting TIG mode. In this range, the
OCV of the machine is controlled between 50 and 70
volts. If using the Lincoln K930-1 TIG Module, set
the Hot start to 10 for maximum OCV.
•
The Arc Control is not used in the TIG mode.
CV-WIRE: The CV-WIRE mode features continuous
control from 10 to 45 volts. The mode was intended
for most GMAW, FCAW, and MCAW applications.
•
The Hot Start control is not used in the CV-WIRE
mode.
•
The Arc Control regulates pinch effect. At the mini-
mum setting (-10), minimizes pinch and results in a
soft arc. Low pinch settings are preferable for weld-
ing with gas mixes containing mostly inert gases. At
the maximum setting (+10), maximizes pinch effect
and results in a crisp arc. High pinch settings are
preferable for welding FCAW and GMAW with CO2.
CV-FLUX CORED: The CV-FLUX CORED mode fea-
tures continuous control from 10 to 45 volts. This
mode was designed for self-shielded flux cored wires
that require tight voltage control.
•
The Hot Start control is not used in the CV-FLUX
CORED mode.
•
The Arc Control regulates pinch effect. At the mini-
mum setting (-10), minimizes pinch and results in a
soft arc. At the maximum setting (+10), maximizes
pinch effect and results in a crisp arc. Most self-
shielded wires work well at an Arc Control setting of 5.
8. HOT START and ARC CONTROL features have
different functions depending on the welding Mode
that is active. Each feature is described under the
welding mode heading.
(See Item 6 for specified
Mode Operation)
LOWER CASE FRONT
The output studs, line switch and remote connector
are located on the lower case front.
9. Both STUDS contain "Twist-Mate" connector
inserts.
•
The Negative stud is configured to accept the
pass through gas system.
10. The ON-OFF switch is a 3-phase circuit breaker
rated at 100 amps per leg.
11. The METER POLARITY switch is located above
the output connectors. The switch provides a work
connection for wire feeder voltmeters. Place the
switch in the position of the electrode polarity indi-
cated by the decal.
The switch does not change
the welding polarity.
12. 3-PIN AMPENOL for remote control.
REMOTE CONTROL of the OUTPUT CONTROL and
WELD TERMINALS
The EX350i has auto sensing of remote output con-
trols.If after connecting or removing a remote, the
EX350i is not configured the way you would like the
local or remote control settings can be changed by
pushing the OUTPUT CONTROL or WELD TERMI-
NAL button. (A user cannot select between the 3 and
14 pin amphenols.)
CV modes
•
The remote will default to the 14-pin amphenol
remote if a remote is connected to either of the 14-
pin amphenols and the 3-pin amphenol. Note: Only
one of the 14-pin amphenols can have a remote
control connected at a time. If no remote is connect-
ed to either of the 14-pin amphenols then the
remote will default to the 3-pin amphenol if a remote
is connected to it.
•
If a remote control
is connected or is not connect-
ed to any of the amphenols the WELD TERMINAL
control will default to REMOTE.
EX350i
Содержание EX350i
Страница 32: ...EX350i NOTES...