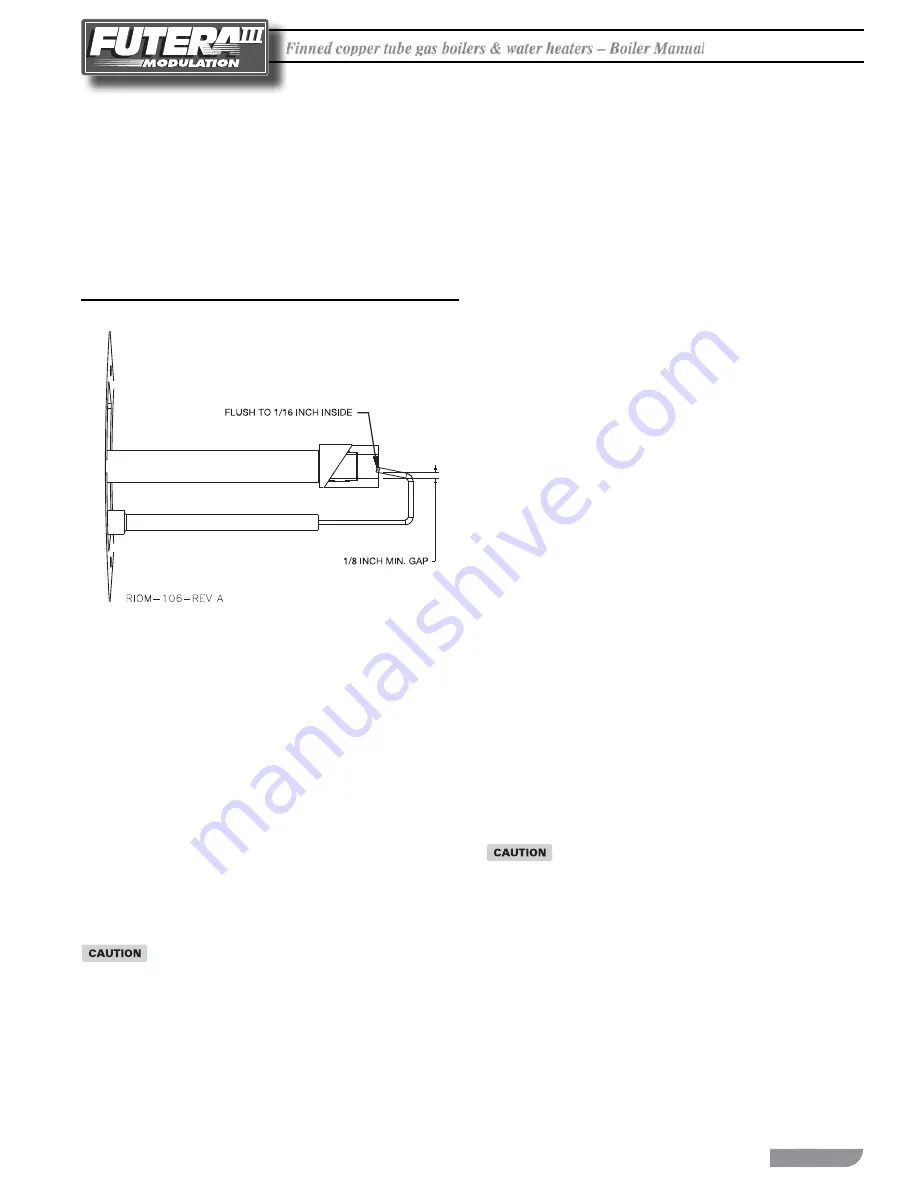
Fi
d
b
b il
&
h
B il
M
l
Finned copper tube gas boilers & water heaters – Boiler Manual
25
F
F
CHECKING & ADJUSTMENTS
Spark Gap
With the main and pilot gas manual valves in the closed position
energize the unit. Observe the trial for ignition to confi rm that the
spark is strong and continuous. If not check and adjust the spark
gap as shown in Figures 17 &18.
Figure 16
Spark Gap
Pilot Adjustment
Th e pilot pressure has been factory set at 3 in. W.C. for natural and
LP gas and shouldn’t need adjustment. To check the pilot pressure
close the manual main shut-off valve 2 and the pilot gas shut-off
valve, Figure 14. Remove the 1/8" pipe plug from the pilot tee and
connect a manometer having a minimum range of
6 in
,
152 mm
WC to it. Open the pilot gas shut-off valve. With the unit powered,
generate a call for heat. When the prepurge is complete the ignition/
pilot trial will begin. At this point put the Honeywell RM7800 test
switch in the test position. Th e control will hold in the ignition/
pilot sequence allowing you to check the pressure.
To adjust the pilot the following steps must be taken:
1. Remove the pilot gas pressure regulator cap.
2. Turn the pressure regulator adjustment screw clock-wise to
increase the pressure and counterclockwise to decrease it.
3. Replace the pressure regulator adjustment screw cap.
Never force the regulator adjustment screw beyond the stop
limits or damage to the regulator will occur!
Required Gas Pressure
Provide gas supply pressure at inlet to boiler gas train as follows:
LP
Nat
Minimum (in. W.C.)
2
2
Maximum (in. W.C.)
14
14
Measure pressure when the boiler is fi ring at full rate. Low
gas pressure could indicate undersized gas line or insuffi cient gas
supply.
“Static and operating gas pressure required at the gas valve inlet is
between 2" W.C. and 14" W.C. for natural gas and 2" W.C. and
14" W.C. propane. If the gas pressure is above this limit, a lock-up
style regulator suitable for dead end service such as an Equimeter
or Fisher must be installed to prevent increase (creep) of gas
pressure when the units are not operating. Th is pressure regulator
(supplied by others) may be installed at the service entrance to
each unit or a “master” regulator sized to handle multiple units may
be utilized. Consult local gas utility or regulator manufacturer for
recommendations to meet specifi c job site requirements.”
Input Rate, Natural Gas
Gas appliances are rated based on sea level operation with no adjust-
ment required at elevations up to
2000 ft
,
610 m
. At elevations
above
2000 ft
,
610 m
input ratings should be reduced by 4% for
each
1000 ft
,
305 m
.
Check the input rate as follows:
1. Turn off all other gas appliances that use the same gas meter
as the boiler/water heater.
2. Call your gas supplier and ask for the heating value of the gas.
3. Start the boiler/water heater and let it run for 15 minutes.
4. Using the gas meter and a stopwatch, clock the time that it takes
to burn
10 ft
3
,
0.28 m
3
of gas and divide this time by 10.
5. Insert the heating value and the time, in seconds, into the formula
below.
6. Input = (heating value, Btu/hr)(3600)/(time, seconds)
7. If the computed rate deviates by more than 5% from the rated
input value of the unit, consult factory.
Never increase the input to the boiler/water heater
above that for which it is rated. Doing so can cause
premature failure of the boiler!