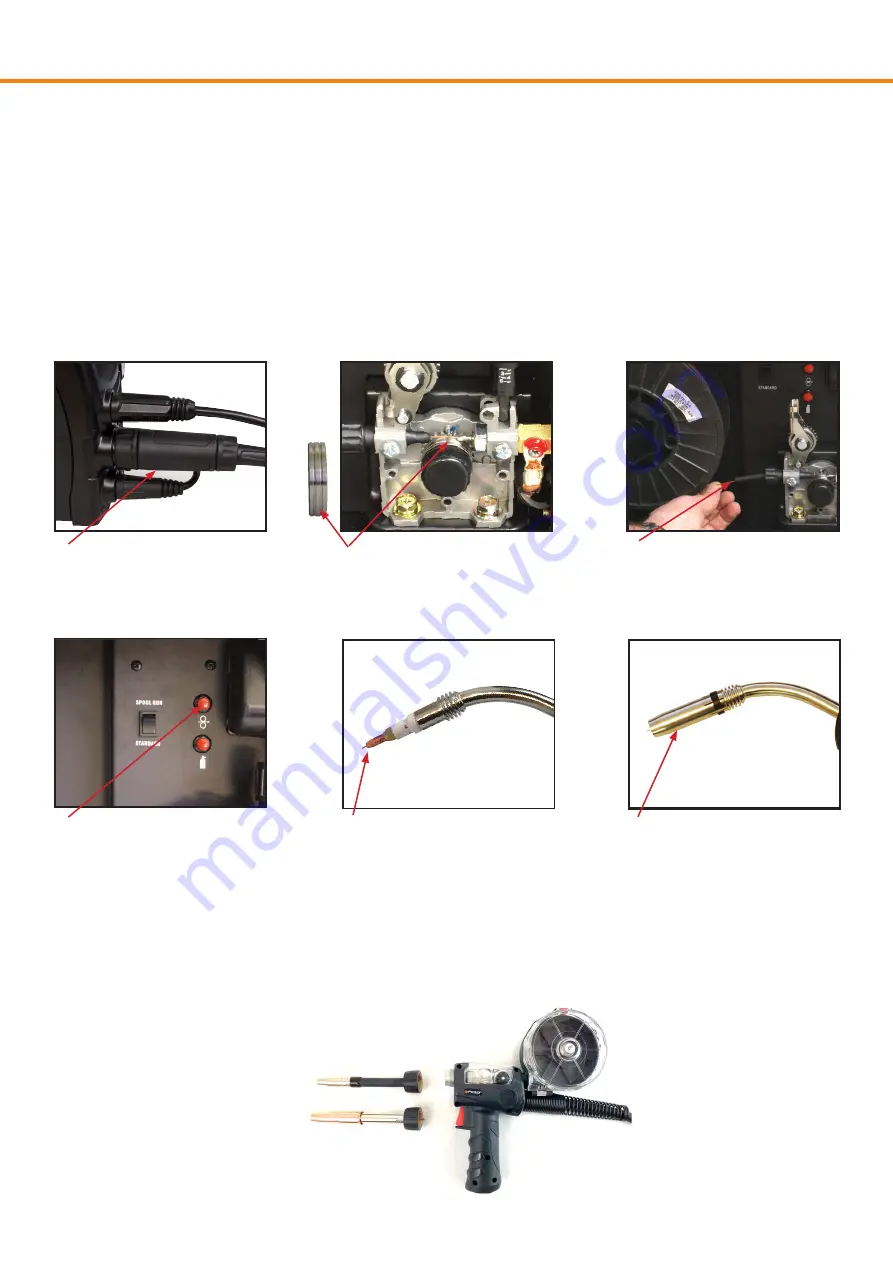
22
Continued Torch & Wire Feed Set Up for Aluminum Wire
(10) Loosen off the inlet guide tube retaining screw
(11) Remove the inlet guide tube from the front end machine euro connector using long nose pliers.
(12) Carefully feed the extended PA liner section into the inlet guide tube hole of the machine euro
connector
(13) Feed the extended PA liner all the way up and over the drive roller
(14) Tighten the torch euro connection to the machine euro connector
(15) Cut the extended liner with a sharp razor knife just in front of the drive roller
(16) Fit an Aluminum contact tip of the correct size to match the diameter of the wire being used
(17) Fit the remaining front end parts to the torch neck ready for welding
(17) Fit the remaining front end parts to the
torch neck ready for welding.
(11) Install a U groove drive roller of the
correct size for the diameter wire being used.
NOTE: MIG 180-145not geared
(7) Place aluminum wire onto spool
holder. Feed the wire through the inlet
guide tube on to the drive roller.
NOTE: MIG 180-145 not geared
(10)Connect the torch to the machine
tighten and secure the torch euro con-
nector to the machine euro connection.
(16) Fit an Aluminium contact tip of the
correct size to match the wire diameter
being used
(12) Press and hold the inch wire button to
feed the wire down the torch cable through to
the torch head.
NOTE:
GEAR DRIVE FEEDER ON 210 MODEL ONLY
The most common and effective method of welding alloy is by using a Spool gun or a push-pull torch. JASIC Technologies America Inc
provides a spool gun that is designed specifically for our machines and when set up correctly will provide the operator with trouble free
welding. Our spool gun is offered in 2 configurations depending on the operators preference. The Torch can come with either a Tweco
style neck or a Binzel style neck. It depends on the Distributors preference in equipment but both are totally interchangable.
SB15 STYLE
TWECO2 STYLE
Содержание JRW145D
Страница 37: ...SPOOL GUN EXPLODED DIAGRAM SPGLBT200 37...