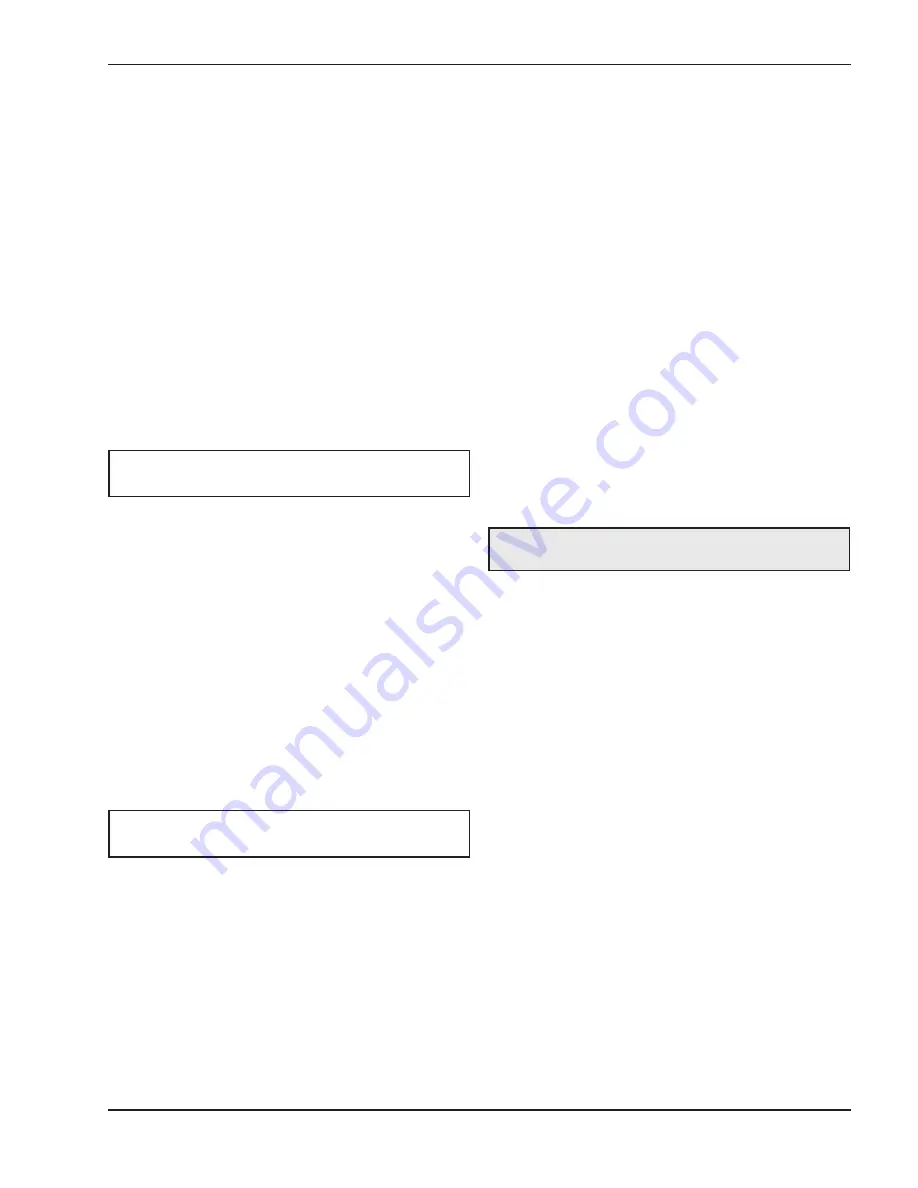
15
Heater Contacts
The
Stg 1, Stg 2, Stg 3
and
Stg 4
terminals (15 through
22) are isolated outputs in the Controller. There is no
power available on these terminals from the Controller.
These terminals are to be used as a switch to either
make or break the heater circuit. When the Controller
requires heater stages to fire, it closes the contact
between the appropriate terminals.
Alarm Contact
For field installations, terminals 19 and 20 provide dry
contacts for an alarm. For factory installations, the
alarm is installed with a UDB diagnostic control (when
available). The UDB provides the alarm dry contacts.
Sensor and Unpowered Input
Connections
Outdoor Sensor
Connect the two wires from the optional outdoor sen-
sor to the
Com
(common sensor) and
Air
(outdoor air
sensor) terminals (4 and 5). The outdoor sensor is
used by the Controller to measure the outdoor air tem-
perature.
Heater Outlet Sensor (Field Install)
Connect the two wires from the Heater Outlet Sensor
to the
Com
(common sensor) and the
Boil Out
(heater
outlet sensor) terminals (4 and 7). The heater outlet
sensor is used by the Controller to measure the heater
outlet water temperature from the heater.
Heater Inlet Sensor (Field Install)
Connect the two wires from the Heater Inlet Sensor to
the
Com
(common sensor) and the
Boil In
(heater inlet
sensor) terminals (4 and 8). The heater inlet sensor is
used by the Controller to measure the heater inlet
water temperature to the heater.
Heater Sys/D or DHW Sensor
Either a System Sensor or DHW Sensor may be con-
nected to the Controller. If a sensor is used, connect
the two wires from the sensor to the
Com
(common
sensor) and the
Sys/D
(demand/DHW sensor) termi-
nals (4 and 6).
TROUBLESHOOTING
Field Testing the Power Supply
Verify that all exposed wires and bare terminals are
not in contact with other wires or grounded surfaces.
Turn on the power and measure the voltage between
the 1 and 2 terminals on the P3 terminal block, using
an AC voltmeter. The reading should be 120 VAC
±
10%, and the reading between terminals 2 and 3 must
be less than 1.0 VAC.
Verify the power at the transformer by using the AC
voltmeter across pins 1 and 4 of terminal block P1.
The reading should be between 22 VAC and 26 VAC.
Testing the Sensors (10 kΩ)
In order to test the sensors, the actual temperature at
each sensor location must be measured.
Using Table D on page 16, estimate the temperature
measured by the sensor, based on ohm readings from
various sensors to COM.
The sensor and thermometer readings should be
close. If the meter reads a very high resistance, there
may be a broken wire, a poor wiring connection or a
defective sensor. If the resistance is very low, the
wiring may be shorted, there may be moisture in the
sensor or the sensor may be defective. To test for a
defective sensor, measure the resistance directly at
the sensor location.
Testing the Enable/Disable and
DHW Field Install Inputs
When the Enable/Disable system calls for heat, you
should measure between 22 VAC and 26 VAC at ter-
minals 2 and 4 on P1. When the heat demand device
is off, you should measure less than 1 VAC. For DHW
override, use terminals 3 and 4.
NOTE:
The heater outlet sensor is required for
every mode of operation.
CAUTION:
The sensor must be disconnected in
order to measure the correct ohms.
NOTE:
Do not apply power to these terminals as
this damages the Controller.