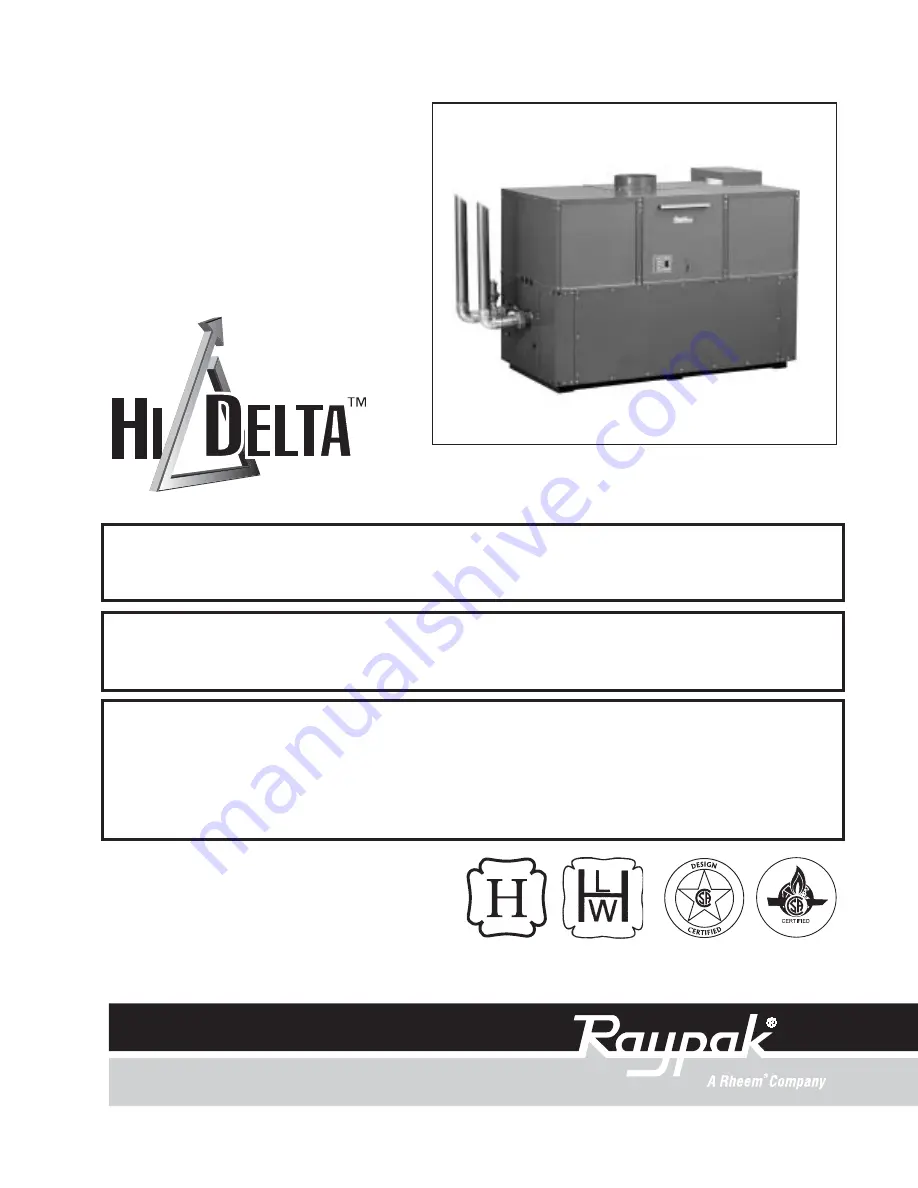
INSTALLATION
AND OPERATING
INSTRUCTIONS
Models 302-902
Type H, WH, & P
FOR YOUR SAFETY
Do not store or use gasoline or other flammable vapors and liquids or other combustible materials in the vicinity of
this or any other appliance. To do so may result in an explosion or fire.
WARNING:
Improper installation, adjustment, alteration, service or maintenance can cause property damage,
personal injury or loss of life. Refer to the user’s information manual provided with this boiler. Installation and
service must be performed by a qualified installer, service agency or the gas supplier.
FOR YOUR SAFETY
WHAT TO DO IF YOU SMELL GAS:
·
Do not try to light any appliance.
·
Do not touch any electrical switch; do not use any phone in your building.
·
Immediately call your gas supplier from a neighbor’s phone. Follow the gas supplier’s instructions.
·
If you cannot reach your gas supplier, call the fire department.
This manual should be maintained in legible condition
and kept adjacent to the boiler or kept in a safe place
for future reference.
P/N 240757
CATALOG NO. 1000.50
K
Effective:
08-01-03
Replaces: 01-15-03
Содержание 302-902
Страница 7: ...7 General Information ...
Страница 49: ...49 WIRE DIAGRAM MODEL 302 402 Reference Drawing Number M152462 Rev M H4 W1 ...
Страница 50: ...WIRE DIAGRAM MODEL 302 402 Reference Drawing Number M152470 Rev J H3 W3 50 ...
Страница 51: ...51 WIRE DIAGRAM MODEL 502 752 Reference Drawing Number M152464 Rev R H3 HW3 ...
Страница 52: ...WIRE DIAGRAM MODEL 902 Reference Drawing Number M152465 Rev P H3 W3 52 ...