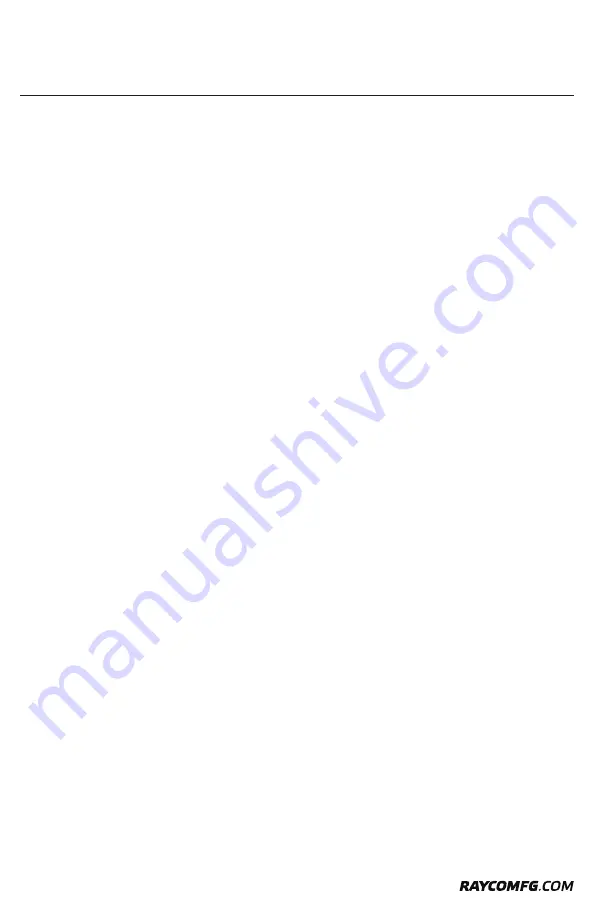
T415 Operation & Service Manual
20
Safety
attachments that cause the machine to exceed the weight that
is stamped on the certification plate also place the operator
into an unprotected environment. Excessive weight may inhibit
the brake performance, the steering performance and the
ROPS. The protection that is offered by the ROPS/FOPS
Structure will be impaired if the ROPS/FOPS Structure has
structural damage. Damage to the structure can be caused
by an overturn, a falling object, a collision, etc.
Do not mount items (fire extinguishers, first aid kits, work lights,
etc.) by welding brackets to the ROPS/FOPS Structure or
by drilling holes in the ROPS/FOPS Structure.
Welding brackets or drilling holes in the ROPS/FOPS
Structures can weaken the structures. Consult your Rayco
dealer for mounting guidelines.
The Top Over Protection Structure (TOPS) is another type
of guard that is used on crawlers. This structure protects
the operator in the even of a tip over. The same guidelines
for the inspection, the maintenance and the modification of
the ROPS/FOPS Structure are required for the Top Over
Protection Structure.
Other Guards (If Equipped)
Protection from flying object and/or falling objects is required
for special applications. Logging applications and demolition
applications are two examples that require special protection.
A front guard needs to be installed when a work tool that
creates flying objects is used. Mesh front guards that are
approved by Rayco or polycarbonate front guards that are
approved by Rayco are available for machines with a cab or
an open canopy. On machines that are equipped with cabs,
the windshield should also be closed. Safety glasses are
recommended when flying hazards exist for machines with
cabs and machines with open canopies.
If the work material extends above the cab, top guards and
front guards should be used.
Additional guards may be required for specific applications
or work tools. The Operation and Maintenance Manual
for your machine or your work tool will provide specific
requirements for the guards. Consult your Rayco dealer for
additional information.
Precautions for Welding on FRAME with
ENGINE/MACHINE Electronic Control
Unit (ECU)
Important: ALWAYS disconnect Electronic Control Unit (ECU)
connectors and engine control system-to-machine ground
before welding on engine or machine.
High currents or electrostatic discharge in electronic
components from welding may cause permanent damage.
Safety Decals
The safety decals located on this machine contain useful
and important information which will help you to operate
your machine safely. The complete decal kit and location of
each decal is given in the “Parts” manual. For your protection,
familiarize yourself with each label until you completely
understand the warning intended. Do not violate any such
warnings!
Keep all decals in place and in good condition:
• Use soap and water to keep decals clean. DO NOT
use mineral spirits, abrasive cleaners or other similar
cleaners which will damage the decals.
• Replace any damaged or missing decals. Before
attaching decals, the surface temperature of the metal
must be at least 40 degrees. The metal should also
be clean and dry before attaching the decal.
• If a machine component to which a decal is attached
is replaced, be sure to replace the decal as well.
• Replacement decals may be purchased from Rayco
Mfg or your Rayco dealer.
LOCK-Out / Tag-Out Guidelines
Always practice lock out tag out procedures when working
on this machine.
Locking and tagging out equipment safeguards those working
on the equipment from being injured by its unexpected
energized or releasing stored energy. This section summarizes
the applicable requirements for lockout/ tag out procedures,
and its intent to comply with OSHA regulations.
Lock Out Procedure
1. All affected persons are to be notified that the
equipment will be off and locked out.
2. All energy sources for the equipment should be
identified.
3. The equipment shall be shut off or otherwise
deenergized, being careful to de-energize all
energy sources. This includes all valves, switches,
breakers, or other controls that supplies energy to the
equipment. In case of mechanical energy, a block may
be used to stop the release of stored energy.
4. A lock is to be placed on each energy source
disconnect or energy release block.
a. The lock is to be placed directly on the
equipment if provided with an integral locking
device.
b. If there is no integral lockout device on the
equipment, securely attach an independently
manufactured lockout device on the equipment and
then place the lock on the lockout device.
c. If none of the above are possible, use the tag out
procedure.