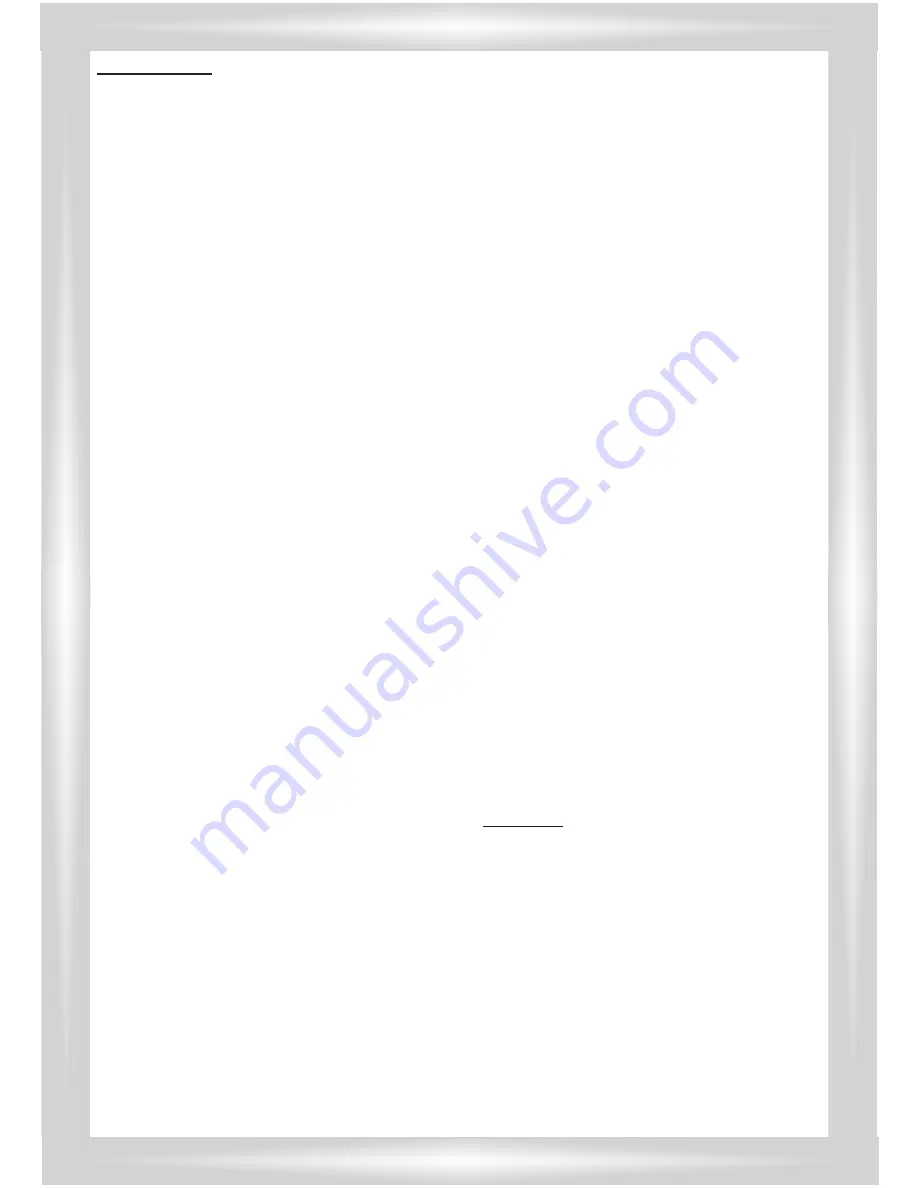
Flue system
This appliance is designed to work on an Open or Conventional flue only, with a minimum
effective height of 4.5 metres. A negative flue draught is required in the region of 1.0mm
(.04”) WG
If the flue draught is likely to exceed this amount (e.g. with a tall chimney), then a proprietary
flue stabilizer will be required.
The initial flue pipe from the Rayburn can be of vitreous enamelled steel or cast iron, having a
diameter of 100mm. It is advisable to rise vertically from the Rayburn for at least 600mm
before a bend is introduced. Bends should be kept to a minimum and must allow the flue to
continue to rise at least by 45 degrees.
The main flue can be a masonry chimney with a 125mm diameter stainless-steel lining, suit-
able for temperatures up to 330 deg C. Alternatively, clay linings are suitable or flue blocks. If
it is an existing chimney, it must be first swept and a new lining fitted or the existing flexible
lining renewed.
If there is no masonry chimney available, then a prefabricated, twin wall, factory insulated sys-
tem may be used of an appropriate material, normally stainless-steel. Internal diameter should
be 125mm. Note that the appliance operates in a ‘dry’ condition with a negative draught and
has a maximum flue gas temperature of 330 deg C.
There must also be some provision for cleaning access.
An approved oil terminal or cowl must be fitted and the flue must terminate above roof height
in accordance with BS Codes of practice, 5410. Generally this means that the terminal should
be at least 600mm measured vertically from the roof, although additional clearances will be
required in some situations.
If the flue terminal location is likely to be subject to occasional wind turbulence (e.g. due to
adjacent tall trees or hills) an anti-down-draught cowl may be used, but if the problem is due
to a high pressure zone, no known cowl can guarantee to overcome this. Extra height may be
the only answer.
Ridge vent terminals or gas appliance cowls must not be used with this Rayburn.
The flue must only serve the Rayburn as sharing with another appliance is not allowed.