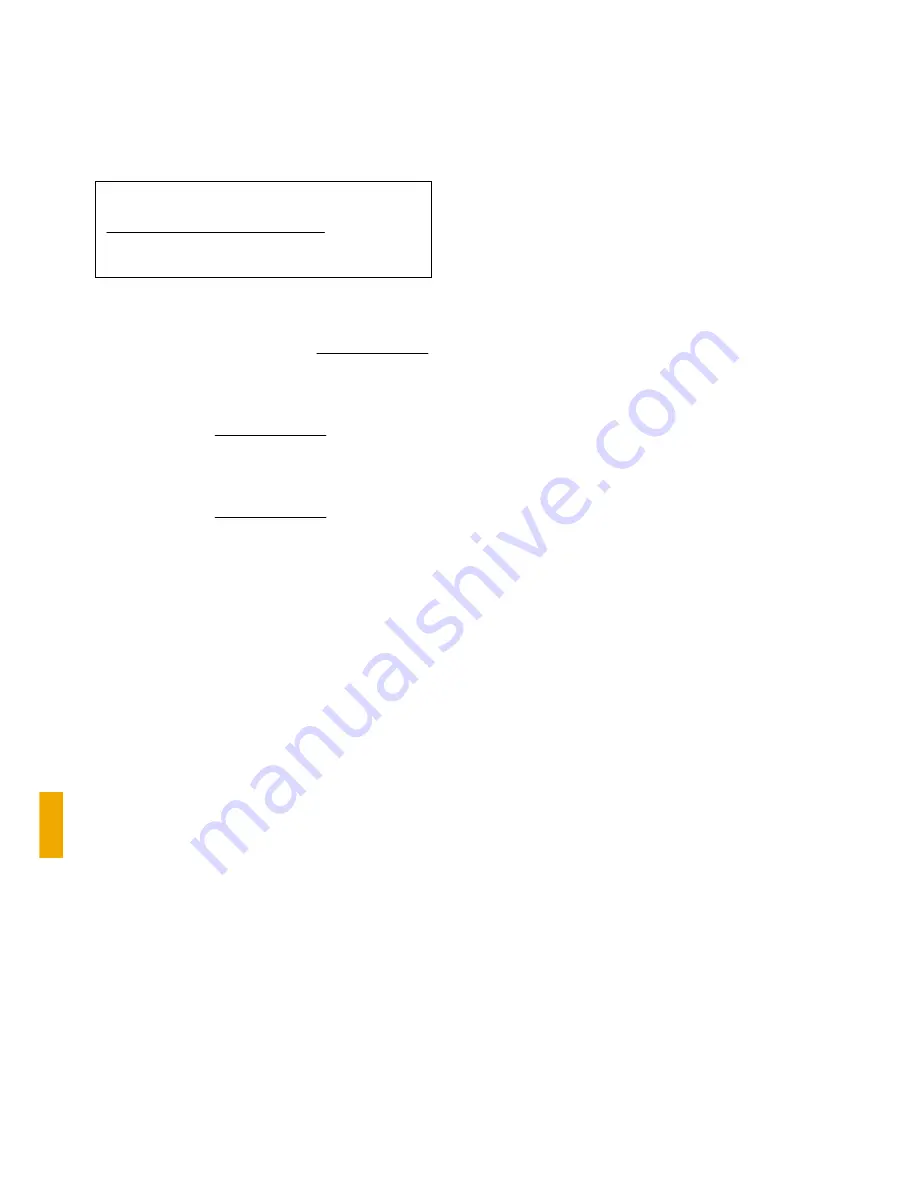
10
Temperature range
Back-flow temperature should be over 40º C for oil-fired
units and over 45º C for gas-fired units. The advance
temperature can be set at a maximum of 85º C. Mini-
mum water circulation can be approximately calculated
as follows:
m³/h
70
(kW)
capacity
nom.
=
Calculating discharge flows:
Min. discharge flow bypass (m³/h) =
70
(kW)
Capacity
nom.
Min. discharge flow for heating circulation pump when
D
T = 10 K in m³/h =
11,6
(kW)
Capacity
nom.
Min. discharge flow for heating circulation pump when
D
T = 20 K in m³/h =
23,2
(kW)
Capacity
nom.
The
rapidomatic
®
electronic heat circulation regulator
(accessory) permits energy-saving operation by control-
ling the hot water temperature according to heat re-
quired, including shutdown resultant from night-time
drop in demand.
6.4Flue connection
The flue pipe should be connected to the boiler flue gas
outlet in compliance with DIN 1298. Ensure that it is
properly attached all around the flue gas outlet. Connec-
tion to chimney is carried out according to the corre-
sponding regulations. To avoid noise transmission, it is
advisable to install a noise insulation layer between the
flue pipe and the chimney wall. The flue pipe must be
attached to the chimney sloping upwards.
A chimney of adequate dimensions is vital for the correct
functioning of the burner unit.
Dimensions comply with DIN 4705, with reference to DIN
18160, and on the basis of boiler and burner capacity.
For sliding units, use chimneys corresponding to DIN
18160 part 1, group 1. The total exhaust gas flow for the
collective nominal heat capacity must be taken into ac-
count when calculating dimensions. The effective chim-
ney height is measured from the burner level. In this re-
spect, we draw your attention to any local regulations
that may apply.
Ensure that the flue gas temperature in the lower capac-
ity range does not drop below approx. 160º C on entry
into the chimney.
Select a chimney construction that minimises the danger
of condensation or a cold chimney inner wall. For exact
and constant control of the chimney draught, we recom-
mend the installation of a draught limiter, which permits:
1. stabilisation of draught variations
2. virtual elimination of dampness inside chimney
3. reduced waste when system is off.
Connection pieces should be attached to the chimney
with an upward incline, in flow direction, of 30º or 45º. It
is advisable to fit flue pipes with heat insulation.
6.5 Checking seals
Fill the boiler and haeting system with water and carry
out seal check. Do not execeed the the maximum per-
mitted total pressure of 5.5 bar while doing so.
Your attention is drawn to the VD Tüv guidelines relating
to water quality in hot water systems and heating units.
6.6 Burner connection
Unscrew the steel plate from the burner door before fit-
ting burner. A hole should be made in the steel plate us-
ing a welder, if required by the size of the burner flame
tube.
Note:
To avoid dropping below the dew point, partial power is
set at 60% of full power. A hole in the burner door allows
the connection to certain gas blast burners of an exhaust
gas re-circulator.
When connecting an exhaust gas re-circulator, remove
the aluminium shutter (see Fig. 34, page 30) and knock
a hole through the firebrick situated behind it.
6.7 Fuels
Heating oil complying with DIN 51603, town gas, natural
gas and liquid gas. See DVGW worksheet G 260.
A symmetrical flame, burning in an optimum-sized com-
bustion chamber means that fossil fuels are burnt with a
minimum of contamination.