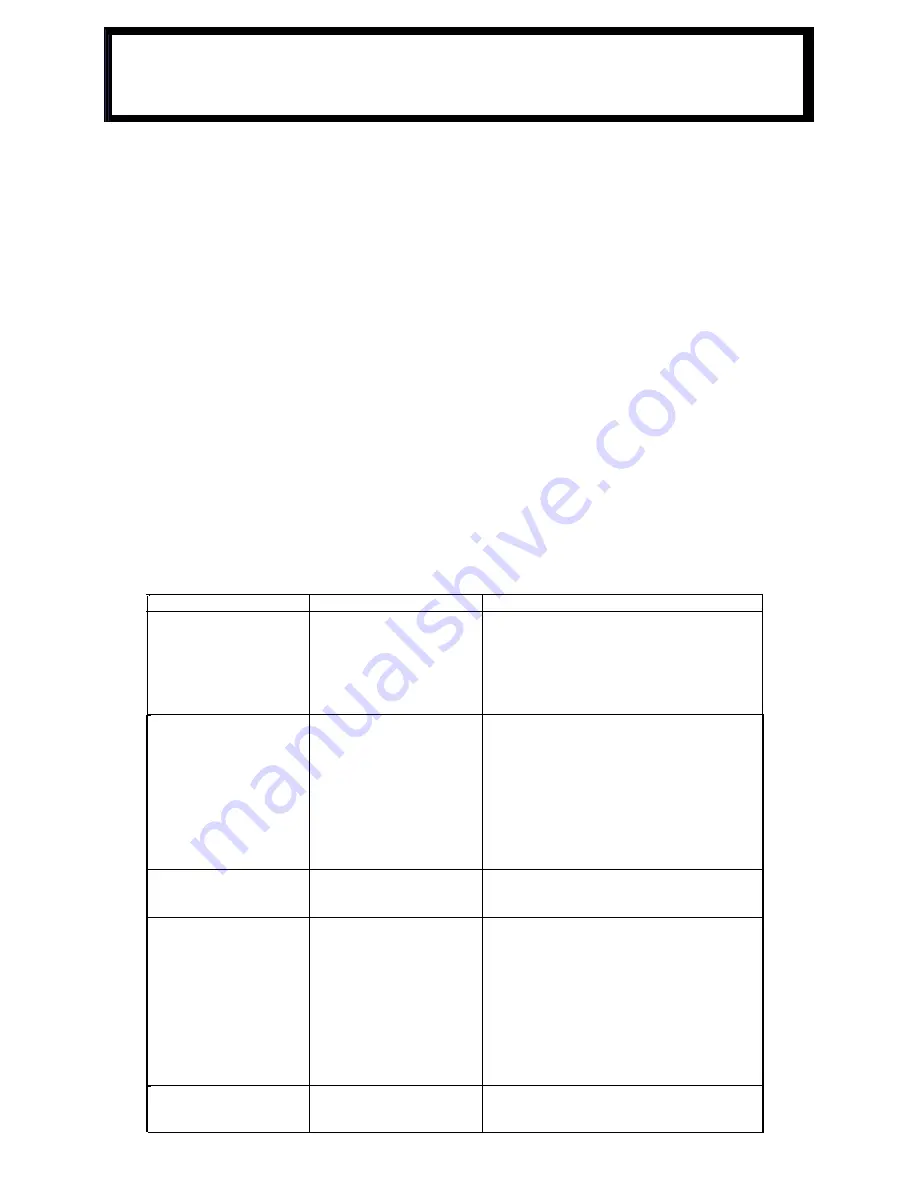
7
CONDITION
POSSIBLE CAUSE
CORRECTION
MOTOR RUNS IN ONE
DIRECTION ONLY
(1) Defective solenoid or stuck
solenoid
(2)Defective remote control
switch
(1) Jar solenoid to free contacts. Check by applying
12 volts to coil terminal (it should make an audible
click when energized).
(2) Disengage winch clutch, remove remote control
switch plug from the socket and jump pins at 8 and
4 o'clock. Motor should run.Jump pins at 8 and 10
o'clock. Motor should run.
MOTOR RUNS
EXTREMELY HOT
MOTOR RUNS, BUT WITH
INSUFFICIENT POWER,OR
WITH LOW LINE SPEED
(1) Long period of operation
(2) Insufficient battery
(3) Bad connection
(4) Insufficient charging system
(1) Cooling-off periods are essential to prevent
overheating.
(2) Check battery terminal voltage under load. If 10
volts or less, replace or parallel another battery to
it.
(3) Check battery cables for corrosion; clean and
grease.
(4) Replace with larger capacity charging system.
MOTOR RUNS, BUT DRUM
DOES NOT TURN
(1) Clutch not engaged
(1) If clutch engaged but symptom still exists, it will
be necessary to disassemble winch to determine
cause and repair.
MOTOR WILL NOT
OPERATE
(1) Defective solenoid or stuck
solenoid
(2) Defective remote control
switch
(3)Defective motor
(4) Loose connections
(1) Jar solenoid to free contacts. Check by applying
12 volts to coil terminal (it should make an audible
click when energized).
(2) Disengage winch clutch, remove remote control
switch plug from the socket and jump pins at 8 and
4 o'clock. Motor should run. Jump pins at 8 and 10
o'clock. Motor should run.
(3) If solenoids operate, check for voltage at motor
posts; replace motor.
(4) Tighten connections on motor.
MOTOR WATER
DAMAGED
(1) Submerged in water or
water from high pressure car
wash
(1) Allow to drain and dry thoroughly, then run
motor without load in short bursts to dry windings.
L
ubrication/Cable lnstallation
All moving parts in the winch are permanently
lubri cated with high temperature lithium grease at
the time of assembly. Under normal conditions,
factory lubrication will suffi ce. Lubricate cable
periodically using light penetrating oil. Inspect
for broken trands and replace if necessary with
Ramsey part number listed in Parts List. If the
cable becomes worn or damaged, it must be
replaced.
Unwind the new cable by rolling it out along the
ground, to prevent kinking. Remove old cable and
observe the manner in which it is attached to the
cable drum fl ange.
Before installing the new cable assembly, make
sure end of cable is squarely cut and wrapped
with tape to prevent fraying.
Troubleshooting Guide
Position the cable drum so that the large
13/32” diameter hole in the motor end drum
fl ange is approximately on the top. Form a
short bend (approximately 1/2” long) in the end
of the cable. Insert the bend into the 13/32”
hole in the drum fl ange and then carefully run
the winch in the “reel-in” direction approxi-
mately 3/4 revolution until the 1/4” diameter
threaded hole in the drum fl ange is on top.
Secure the cable to the drum fl ange using
cable anchor and capscrew. Securely tighten
the capscrew but do not overtighten.
Wind 5 wraps of cable onto the drum. Wind on
the rest of the cable by pulling in a light load to
keep the tension constant. Allow the cable to
swivel by using a length of chain or a swivel
block between the cable hook and the load.
LUBRICATION & CABLE INSTALLATION
Содержание Quick-Mount QM5000H
Страница 2: ......
Страница 3: ...3 SAFETY PRECAUTIONS OPERATION TIPS...
Страница 4: ...4 TECHNIQUES OF OPERATION...
Страница 11: ......
Страница 12: ...Ramsey Winch Company Post Office Box 581510 Tulsa Oklahoma 74158 1510 Telephone 918 438 2760 FAX 918 438 6688...