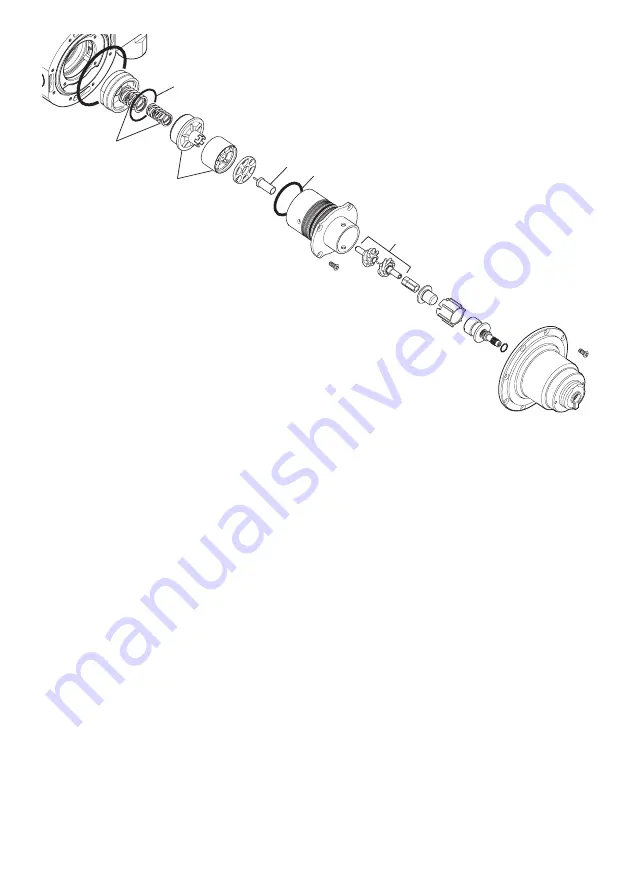
21
Critical Components
Figure 4
A
A
D
D
G
G
Performance Check
Six Monthly
Exercising the Thermostat:
If the valve has not been in regular or recent use the
thermostat should be exercised before any other checking. Where user adjustment
of the blend temperature is available the exercising of the thermostat can be
achieved as described in
COMMISSIONING
. For valves with locked temperature
control it is necessary to isolate and restore each supply in turn a few times.
Blend Temperature:
check for correct blend setting and/or maximum preset
temperature. Reset as necessary
Performance:
check blend stability against known datum (e.g. commissioning
check) for an induced pressure or flow change. Renew thermostatic cartridge when
necessary.
Function:
check inlet pipework temperature for correct function of checkvalves,
and maintain/renew as necessary. Check and clean strainers as appropriate.
Lubricate accessible seals when necessary using silicone-only based lubricant.