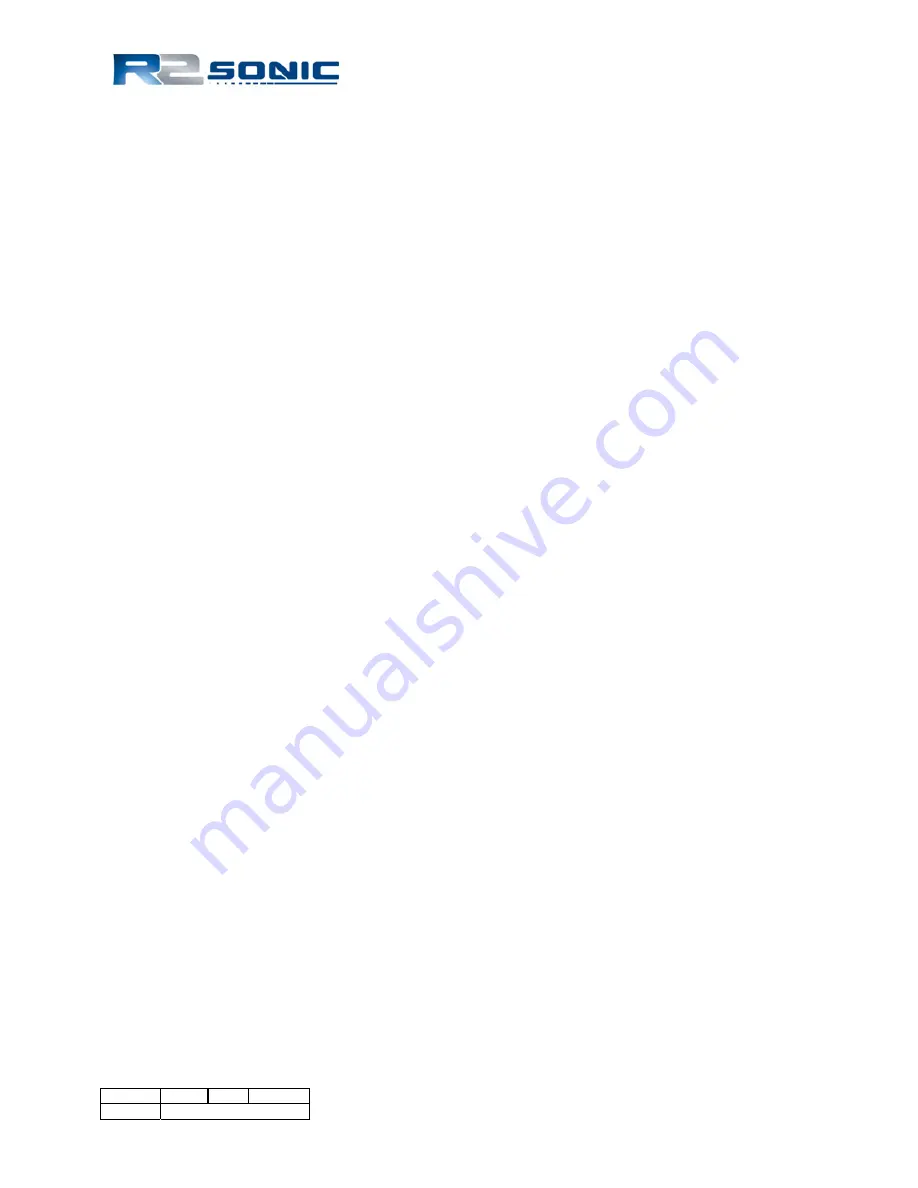
Page
74
of
133
Version 3.0 Rev r000
Date 25-08-2010
Part No. 96000001
during survey operations. If mounting the antenna on a vessel that has helicopter landing facilities,
coordinate the placement of the antenna with the personnel in charge of helicopter operations.
When the location for the antennae has been determined the next step is determining how the
coaxial cable, connecting the antenna and the receiver, is to be run. The cables should be run in
such a manner so as to be protected from possible damage. Cables should not be run through
hatches or windows, if it can be avoided; if such runs are necessary, then a block or other such
obstruction should be placed so that the hatch or window will not close on the cable. If the cables
are to be suspended between two points, a rope or other line should be strung to carry the weight
of the cables. Cables should never be kinked; all cables have a minimum bending radius, if it is
known adhere to it, if it is not known, use common sense. Do not run cables in a manner that they
will become safety hazards on the vessel, causing personnel to trip or be caught on them. Avoid
running cables along voltage carrying lines.
It is important to mark the cables at both ends to denote what they are and to where they go.
The connection to the antenna may be required to be completely water proofed (depending on the
manufacturer’s recommendations) using electrical tape, with a secondary covering of self-
amalgamated tape. Ensure that there are no air gaps in the tape; they will become a channel for
water. If a cable is to be run upwards from the antenna, form a drip loop by leaving slack in the
cable that will hang below the antenna connector. This will allow any water that flows down the
cable to collect and drip from the slack loop instead of running into the connector.
The cables, connectors and antennae should be inspected regularly for signs of damage, corrosion
or abuse. Any abrasions on the cable should be securely taped; if possible, a waterproof coating
should also be applied.
8.1.2
GPS Calibration
Prior to commencing survey operations, the accuracy of the Differential GPS position and
transformation to local datum should be determined. There are two main methods to determine
the accuracy of the DGPS position and data transformation. For both methods, a local land survey
benchmark is required.
8.1.2.1
Position Accuracy Determination Method 1
The GPS antenna is physically placed over the survey benchmark. The surveyor will ensure that the
antenna has a clear view. This is particularly important if the benchmark being used is in a dock area.
The surveyor will also ensure that, if a separate antenna is used to receive differential corrections,
that it is not blocked.
The GPS position data should be logged, in the data collection software, for not less than 15
minutes. The collected data can then be averaged, standard deviations determined, and compared
to the published position of the survey benchmark.
Содержание 2022
Страница 1: ...SONIC 2024 2022 BROADBAND MULTIBEAM ECHOSOUNDERS Operation Manual V3 0 Part No 96000001 ...
Страница 2: ...Page 2 of 133 Version 3 0 Rev r000 Date 25 08 2010 Part No 96000001 ...
Страница 28: ...Page 28 of 133 Version 3 0 Rev r000 Date 25 08 2010 Part No 96000001 This page intentionally left blank ...
Страница 70: ...Page 70 of 133 Version 3 0 Rev r000 Date 25 08 2010 Part No 96000001 This page intentionally left blank ...
Страница 72: ...Page 72 of 133 Version 3 0 Rev r000 Date 25 08 2010 Part No 96000001 This page intentionally left blank ...
Страница 92: ...Figure 78 Smooth log information copied from real time survey log ...
Страница 96: ...Page 96 of 133 Version 3 0 Rev r000 Date 25 08 2010 This page intentionally left blank ...
Страница 112: ...Page 112 of 133 Version 3 0 Rev r000 Date 25 08 2010 This page intentionally left blank ...
Страница 116: ...Page 116 of 133 Version 3 0 Rev r000 Date 25 08 2010 This page intentionally left blank ...
Страница 124: ...Page 124 of 133 Version 3 0 Rev r000 Date 25 08 2010 Part No 96000001 Figure 93 Sonic 2024 2022 Projector ...
Страница 125: ...Page 125 of 133 Version 3 0 REV r000 Date 25 08 2010 Figure 94 Sonic 2024 Receive Module ...
Страница 126: ...Page 126 of 133 Version 3 0 Rev r000 Date 25 08 2010 Part No 96000001 Figure 95 Sonic 2022 Receive Module ...
Страница 127: ...Page 127 of 133 Version 3 0 REV r000 Date 25 08 2010 Figure 96 Sonic 2024 Mounting Bracket Drawing 1 ...
Страница 128: ...Page 128 of 133 Version 3 0 Rev r000 Date 25 08 2010 Part No 96000001 Figure 97 Sonic 2024 Mounting Bracket Drawing 2 ...
Страница 129: ...Page 129 of 133 Version 3 0 REV r000 Date 25 08 2010 Figure 98 Sonic 2022 Mounting Bracket Drawing 1 ...
Страница 130: ...Page 130 of 133 Version 3 0 Rev r000 Date 25 08 2010 Part No 96000001 Figure 99 Sonic 2022 Mounting Bracket Drawing 2 ...
Страница 131: ...Page 131 of 133 Version 3 0 REV r000 Date 25 08 2010 Figure 100 Sonic 2024 2022 Mounting Bracket Flange ...
Страница 132: ...Page 132 of 133 Version 3 0 Rev r000 Date 25 08 2010 Part No 96000001 Figure 101 SIM Box Drawing ...
Страница 133: ...Page 133 of 133 Version 3 0 REV r000 Date 25 08 2010 Figure 102 R2Sonic Deck lead minimum connector passage dimensions ...