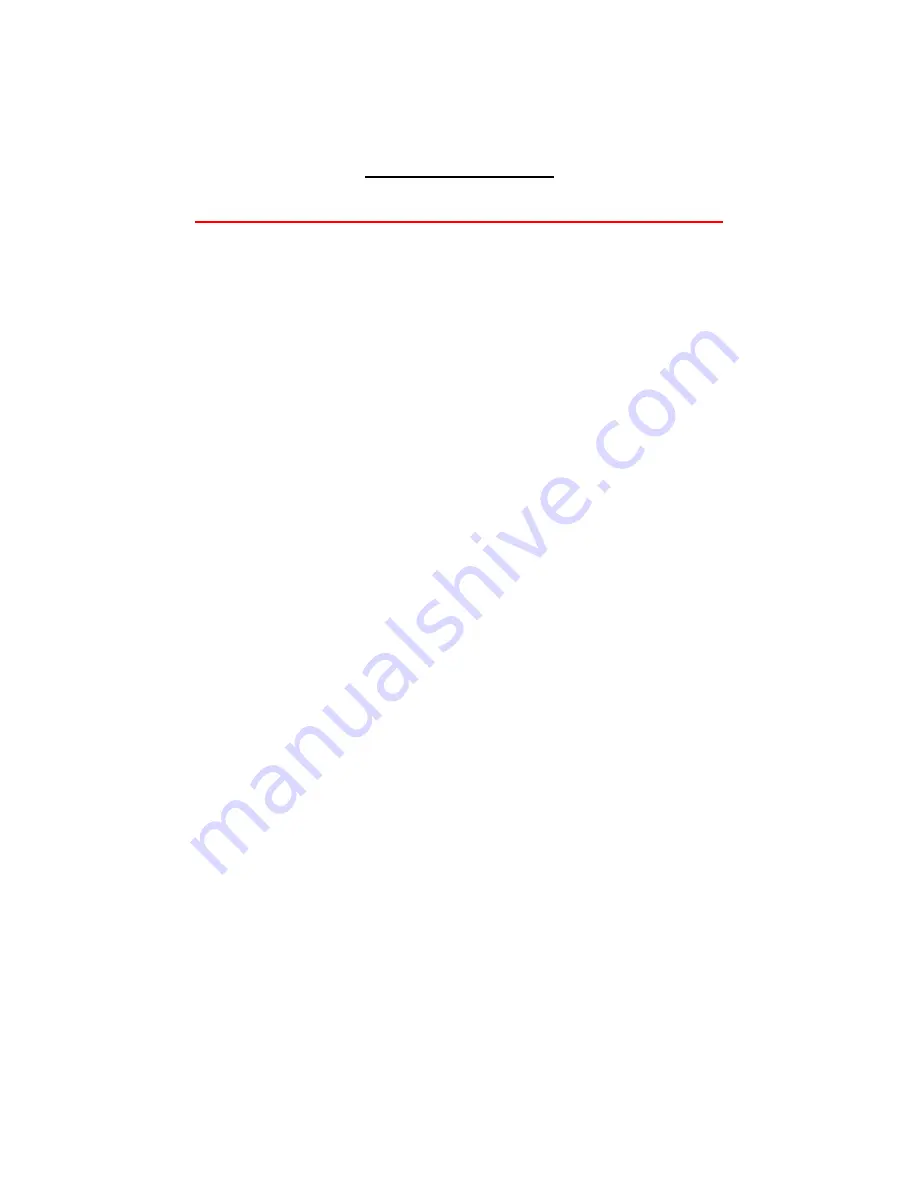
12
Operating Machine
Please ensure all torch consumables are tight before use
1. Ensure machine has been setup as previously stated
2. Turn on the machine and the power light indicates and cooling fan is running
3. Set the function switch in the ‘test gas’ position, air will flow from torch head, now set the
air pressure in gauge using adjuster on regulator on rear of machine to 55PSI
Once the correct air pressure has been set press down the adjuster on air regulator and
set the function switch to the ‘cutting’ position
4. Ensure earth clamp is connected to workpiece or workbench ensuring a good clean point
of contact
5. Select cutting amperage knob to desired cutting power (the following guide lines will vary
in accordance to material grade, characteristics and user operation)
20 Amps for up to 6mm on mild steel
30 Amps for up to 9mm on mild steel
40 Amps for up to 12mm on mild steel
60 Amps for up to 17mm on mild steel
When cutting aluminium, alloys and stainless steel cutting thickness is reduced by
approximately 20%
6. Hold torch in starting position on work and press torch switch and the pilot arc will initiate
(blue flame from torch) , once the pilot arc is in contact with the workpiece it will sense
this and switch to main cutting power.
Once you come to the end of cut/workpiece the machine will sense this and turn off main
cutting power and re-start the pilot arc. If you have now finished cutting release torch
trigger and pilot arc will stop. Air will continue to flow from torch for a preset time to cool
torch consumables.
7.
Getting correct amperage / cutting speed for desired job.
The combination of correct cutting amperage and travel speed can change per user, here
are some tips on obtaining optimum settings.
Blow back when cutting – If you experience blow back and the metal is not cut all the way
through, you either are traveling too fast or you need to increase the cutting amperage
Cutting arc is erratic and work is being cut all way through. You are traveling too slow or
cutting with too high amperage for work. What is happening is the machine is sensing
that there is no metal left to cut and turning off main cutting power and going back to pilot
arc mode and when you move again it senses more metal to cut and brings main cutting
power back in.
It can take a while to get used to plasma cutting if never done before. Experiment with
settings on some scrap material until you find the best amperage / cutting speed for user.
Содержание PLASMA 60HF
Страница 2: ...2...
Страница 17: ...17 Plasma torch switch TS1 Wiring Diagram...
Страница 18: ...18...
Страница 19: ...19...