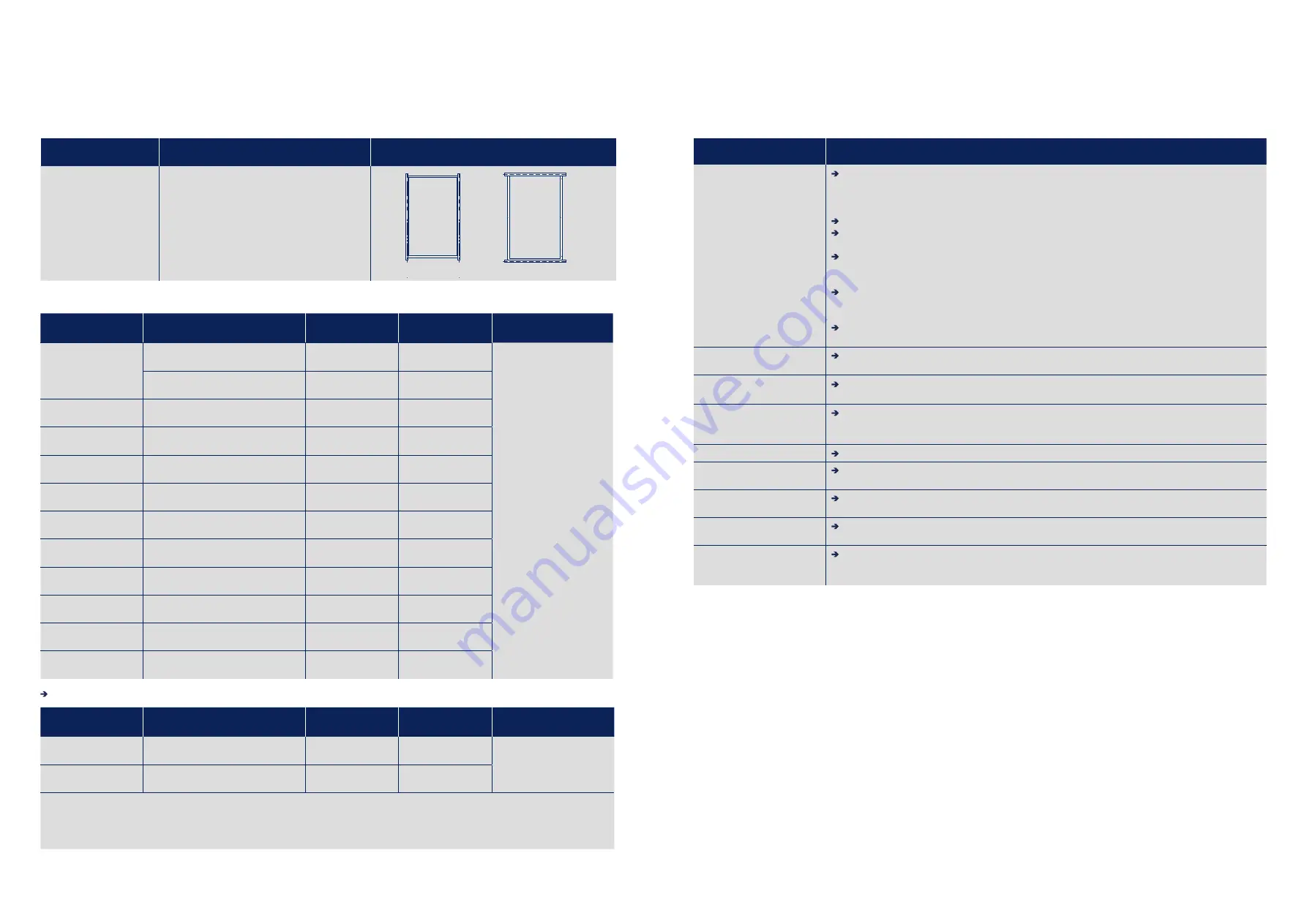
INSTALLATION AND OPERATION MANUAL SOLAR MODULES Q.MAXX-G4
INSTALLATION AND OPERATION MANUAL SOLAR MODULES Q.MAXX-G4
8
9
TYPE OF
INSTALLATION
POINT MOUNTING SYSTEM
LINEAR MOUNTING SYSTEM
Installation
with insertion
profiles
not permitted
IP1
IP2
Installation Site
MOUNTING
OPTION
POSITION OF CLAMPS* [MM]
TEST LOAD
PUSH / PULL** [Pa]
DESIGN LOAD
PUSH / PULL** [Pa]
SAFETY
FACTOR
CL1a
20 - 450 (max. span: 1300 mm)
5400 / 3600
3600 / 2400
1.5
150 - 570
5400 / 3000
3600 / 2000
FB1
356
5400 / 3600
3600 / 2400
FB2
356
4000 / 3600
2660 / 2400
IP1
-
3600 / 3600
2400 / 2400
CL1b
200 - 350
2600 / 3600
1730 / 2400
CL2a
20 - 350
3600 / 2000
2400 / 1330
CL2b
20 - 200
2400 / 2400
1600 / 1600
CL3
200 - 350
4000 / 3600
2660 / 2400
CL5
short side: 20 - 100
long side: 300 - 450
3600 / 3600
2400 / 2400
CL6a
outer clamps: 20 - 450
middle clamps: 646 - 1046
8100 / 4000
5400 / 2660
CL6c
outer clamps: 20 - 450
middle clamps: 746 - 946
4000 / 4000
2660 / 2660
The below mounting options are only possible under certain conditions.
MOUNTING
OPTION
POSITION OF CLAMPS* [MM]
TEST LOAD
PUSH / PULL** [Pa]
DESIGN LOAD
PUSH / PULL*** [Pa]
SAFETY
FACTOR
CL1b
20 - 550
1700 / 2400
1130 / 1600
1.5
IP2
-
*
**
***
Distance between outer edge of module and middle of the clamp; consider further details below.
Loads according to IEC 61215-2:2016 and UL 61730.
Test procedure according to IEC 61215-2:2016 and UL 61730. Loads for these mounting options do not fulfill the requirements
of the standards.
2 Planning
2.3 Mounting Options
2 Planning
2.3 Mounting Options
MOIUNTING
OPTION
REQUIREMENTS
All
The loads in the table are related to the mechanical stability of the solar modules. The mechanical
stability of the mounting system including clamps has to be evaluated by the system supplier. The
listed test load values have been determined with the following clamp parameters: clamp width =
40 mm and clamp depth = 10 mm.
The system installer is responsible for the determination of location-specific load requirements.
Ensure, that the connection cables of the junction box do not run between laminate and mounting
rails
Modules bend under load. Therefore, sharp objects (e.g. screws, ballast stones, rail ends, rails
with burrs or sharp corners) must not be placed near the module backside so as not to touch the
laminate under load.
Ensure that the junction boxes do not touch the mounting structure (e.g. shorts rails, ballast, etc.)
or the rooftop under load. Clamps or insertion profiles etc. must not touch the glass (even under
load).
Unbalanced loads (e.g. snow overhangs, snowdrifts) which result in locally significantly increased
loads must be removed or avoided by technical measures.
CL1a
Clamping range 20 - 450 mm: The clamp position is variable in the given range but the distance
between the clamps along the long side of the module (span) must not be larger than 1300 mm.
CL1a, CL2a, CL3,
FB1, FB2, CL6a
Ensure that module frame is fixed directly on the rail of the substructure (no spacer allowed
between the module and substructure).
CL1b
Using of short mounting rails are permissible, if they overlap with the module less than 210 mm.
Maintain a minimum distance (clearance) of ≥ 35 mm between frame bottom edge and roof top or
ballast
CL1b, CL2b, CL3, FB2
Minimum support depth of 15 mm is required on the back side of the module.
CL5
Minimum required support depth on the module backside is 10 mm on long frame side and 15 mm
on short frame side.
IP1, IP2
Ensure minimum support depth of 15 mm on the backside and 10 mm on the front side of the
module.
FB1, FB2
Use M8 corrosion-proof screws and washers (diameter ≥ 15.8 mm) for mounting slots (Detail A,
Fig.1). Mounting screws and washers should have the same material properties.
CL6c
Using of short mounting rails are permissible, if they overlap with the module less than 150 mm.
Maintain a minimum distance (clearance) of ≥ 50 mm between frame bottom edge and roof top or
ballast