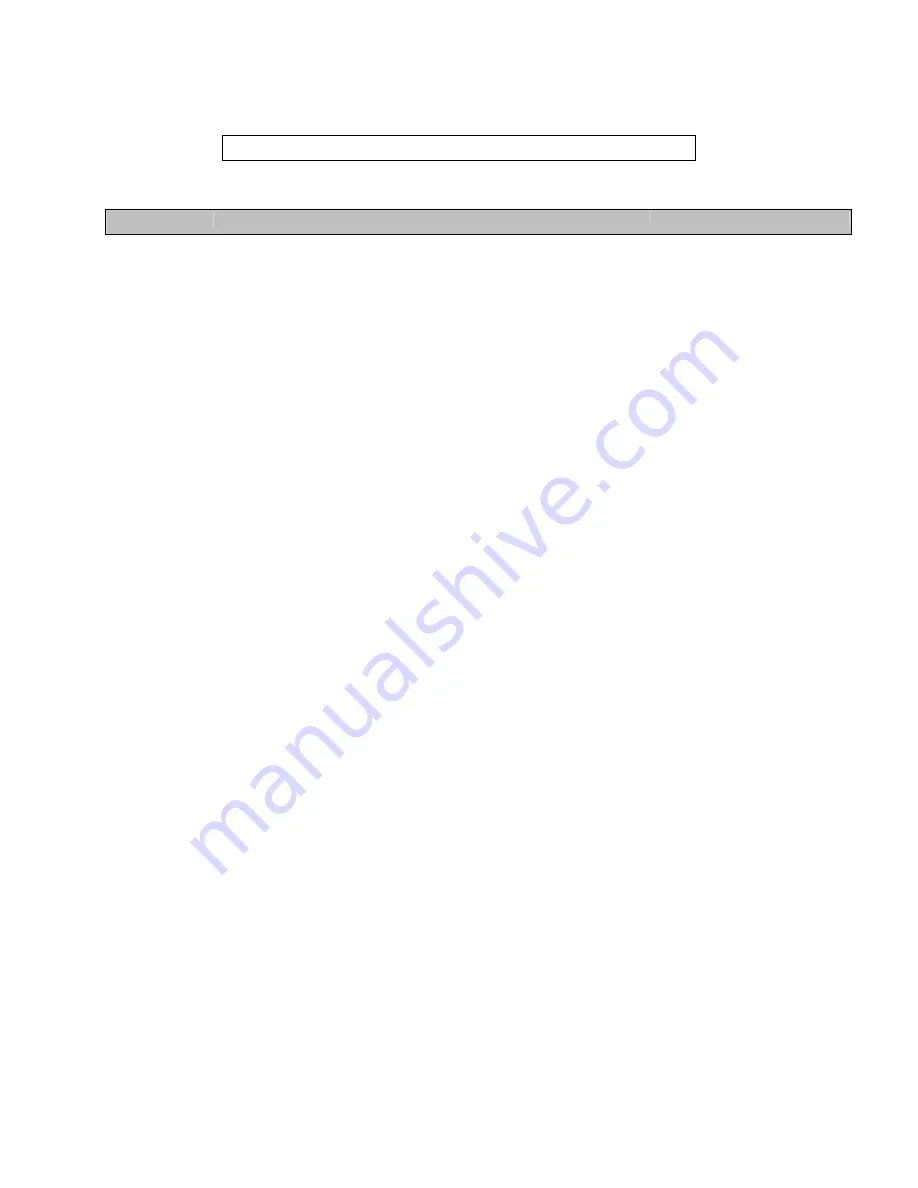
Page 23 of 24
Problem B: Excessive purge flow or blowdown.
Model
Potential Cause
Verification
Corrective Action
B1
All
The purge orifice size is
larger than what is
required for the current
operating conditions.
Verify that the orifice size
corresponds to the actual operating
pressure and flow rate. Contact the
factory if you require sizing data for
your model.
Resize the dryer by
replacing the orifice(s)
with a smaller size.
B2
PCR
PMD
TOC
Inlet or outlet shuttle disc
not shifting.
Verify that the actual operating
pressure and inlet/outlet flow rates
match the specified performance of
the unit. Contact the factory if you
require sizing data for your model.
Line pressure too low at inlet:
Increase the operating
pressure or resize the purge
orifice for the new conditions.
B3
PCR
PMD
TOC
Inlet or outlet shuttle disc
not shifting.
Depressurize the system, remove
shuttle valve assembly, and check
for damage or contamination of
inside the valve body.
Replace or clean valve body
and disc. Check condition of
inlet filtration (A6) and
desiccant (A3).
B4
All
Timer not operating
properly.
Check for incoming voltage
fluctuations caused by inductive
devices (eg. electric motors) on the
same circuit.
Supply line voltage from
another source.
B5
All
Timer defective.
Measure the output voltage from the
timer, as per the cycle and voltage of
your model. See
Maintenance
Section
for more information.
Replace timer.
B6
All
Air leaks.
Remove electrical power from unit
while it is pressurized. Check purge
ports and joints for significant leaks
using soapy water.
Repair as necessary using
Teflon tape or thread sealer.
B7
PHF
PCDA
PCME
PHCA
Check valve ball not
seated properly.
Remove desiccant towers, orifice
plugs, and inspect condition of check
ball and spring for excessive wear or
damage.
Replace check ball
and spring.