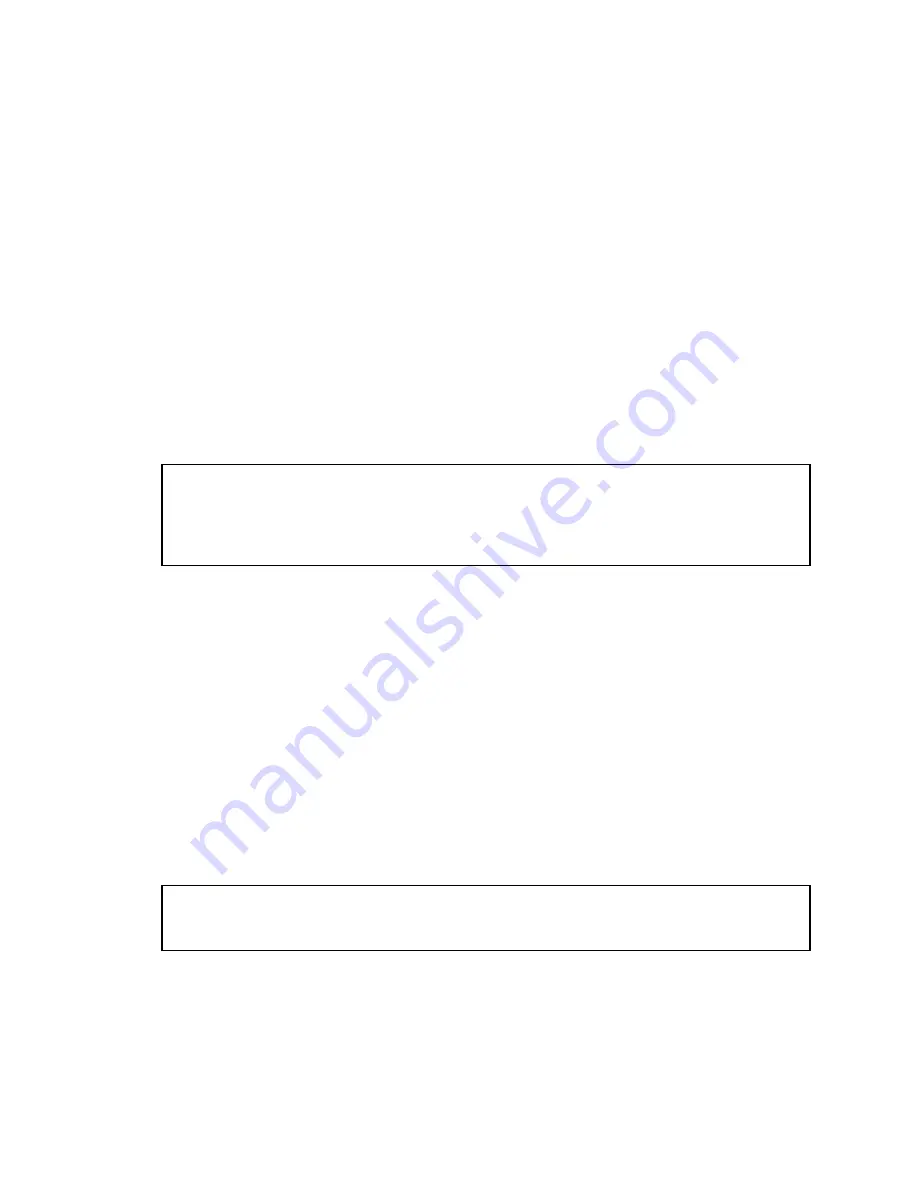
3
SECTION 3 - PRINCIPLES OF OPERATION
3.1 Air System
The air flows from the air compressor to the storage tank and then to the air buffering dryer.
Drying steps involved are summarized as follows:
3.2 Air Compressor
Ambient air is drawn through the intake filters of the air compressor and is compressed to
approximately 80-110 PSIG in the storage tank.
3.3 Pressure Switch, and Safety Relief Valve
The air pressure in the storage tank is controlled by the unloader pressure switch. The
pressure switch starts the air compressor at 80 PSIG and stops it at 110 PSIG. This unloader
pressure switch releases the static air from the air compressor discharge line, allowing for
easy start-up. The inline check valve prevents the air from flowing out of the tank back
through the compressor after the compressor has shut off. The tank pressure safety relief
valve is factory preset to prevent pressure building above 165 PSIG.
3.4 Air Buffering Dryer
Air now flows from the air storage tank to the air buffering dryer which uses silica gel to
remove the moisture. The silica gel is dry when it is a blue color. If the silica gel turns pink,
it must be replaced. Refer to Figure 7.
3.5 Manual Drain Valve
The manual drain provides a means of draining water from the storage tank. The water
should be drained each day after the unit has been in service.
3.6 Water Drain Instructions
With at least 20 PSIG pressure in the storage tank, slowly open the water drain valve
allowing water to drain from tank; close the water drain valve when all moisture or water has
drained. Repeat Procedure as needed. Refer to Figure 7.
NOTE:
Never operate system with the safety relief valve removed from the tank.
DO NOT make adjustments to this valve. This is an A.S.M.E. requirement and
MUST NOT be tampered with.
NOTE:
Important to keep tank drained under freezing conditions.