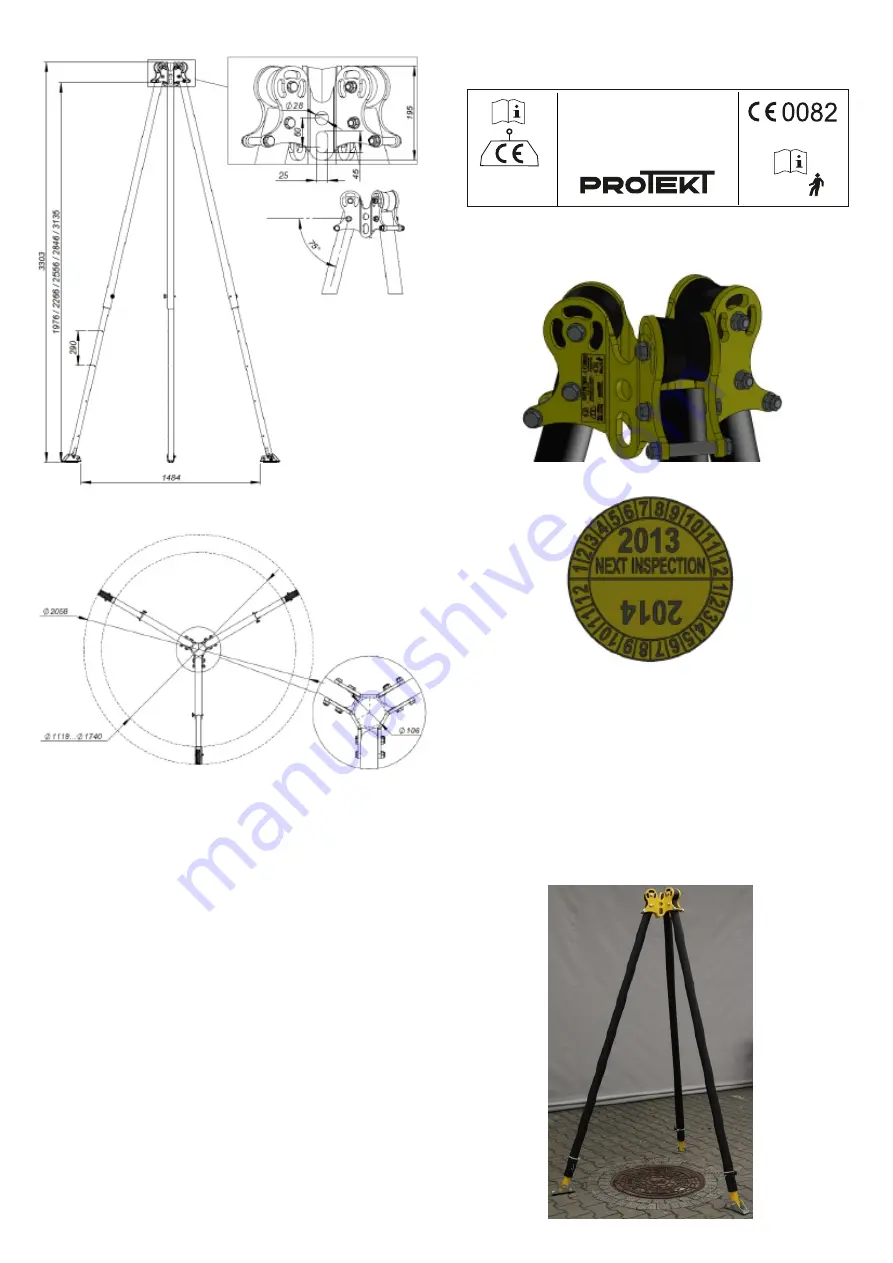
5. GENERAL DIMENSIONS
Fig. 4 – General dimensions of device – front view
Fig. 5 – General dimensions of device – bottom view
6. TIME OF USAGE
Maximum time of usage of correctly operating devices is unlimited.
The device must be withdrawn from use immediately and destroyed if it has
been used to arrest a fall or there are any doubts concerning its function.
NOTE: Maximum time of usage of the device depends on intensity and
environment of use. If the device is used in heavy conditions, being exposed to
frequent contact with water, sharp edges, corrosive substances, extreme of
temperatures, it may be necessary to withdraw the device after only one use.
7. PERIODIC INSPECTIONS
At least once a year, after every 12 months of use, it is necessary to carry out
periodic detailed inspection of the device.
Periodic inspection may be carried out by a properly qualified and skilled
person.
After 5 years of use, it is recommended that periodic inspections are carried
out by the manufacturer of the equipment or an entity authorised by the
manufacturer to carry out such inspections.
8. MARKING OF DEVICE TM 15
Marking elements:
a) Name/ type of device
b) Model designation of device.
c) Reference number.
d) Number/year/class of European standard.
e) CE mark and number of notified body which supervises the production of the
equipment.
f) Month and year of manufacture.
g) Serial number of device.
h) Attention: read instruction manual.
i) Mark of device's manufacturer or distributor.
j) Maximum number of concurrent users
Fig. 6 – Identity label of device TM 15
Fig. 7 – Location of marking of device AT254
2/5
Fig. 8 – “Next inspection” sticker
“Next inspection” sticker should be affixed near identity label and it is
necessary to mark month and year of the next periodic inspection. Do not use
the device after this date.
Note: Before the first use, mark the date of next inspection (date of first use +
12 months, e.g. first use 01.2013 – mark 01.2014).
“Next inspection” sticker affixed near identity label.
9. INSTALLATION OF TRIPOD
It is recommended that tripod TM 15 is installed by two people.
a) Place the tripod vertically in the lowest position on a level, stable and hard
surface. The legs should be turned outside to the maximum.
Make sure that feet are placed on a hard surface and can bear the load. The
tripod should be placed above opening so that work rope is approximately in
the middle of the opening.
max. 3 x
EN 795:2012/B
TS 16415:2013/B
SAFETY
TRIPOD
TM-15
Date of manufacture: MM.YYYY
Serial number: 000001
Ref. AT-017
WLL: 1000kg
MBS: 2100kg