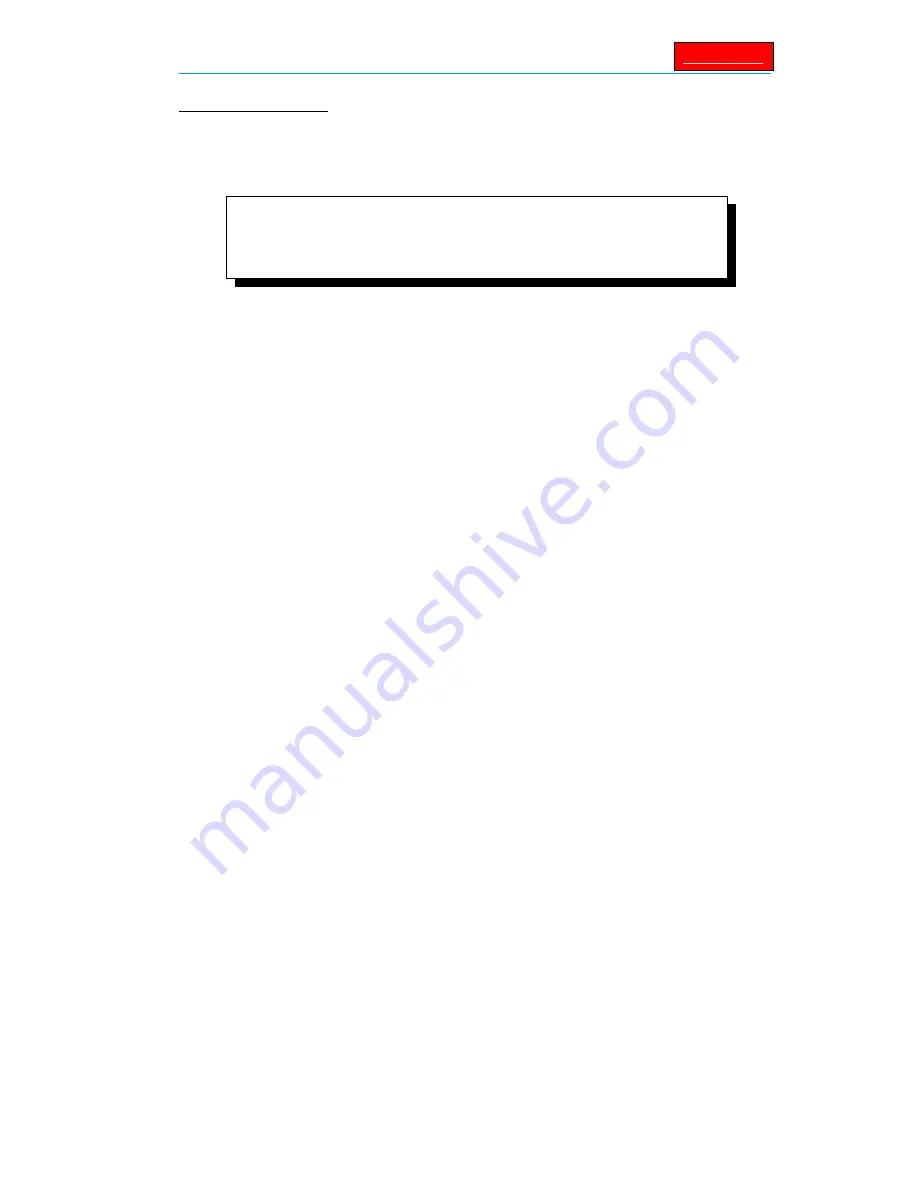
41
Contents
Appendix E — SCANport Datalinks
Appendix E
SCANport Datalink Operation
(Excerpted from A-B Publication 1203-5.2 - May 1995)
In the following discussion, the term ‘Datalink’ is used
extensively. When configuring some SCANport devices, the
term ‘Adaptor I/O’ is used in place of Datalink.
A Datalink is a type of pointer used by some SCANport devices to
transfer information between a SCANport communication interface (such
as the 1560-MBP) and a SCANport device (such as a VFD, SMP3, etc.).
Datalinks allow parameter values to be written when the Control
Command and Reference are sent to the SCANport device. Datalinks
also allow parameter values to be read whenever the Status and
Feedback values are read from the SCANport device.
SCANport devices that support Datalinks have a group of parameters for
Datalink configuration. These parameters are identified as ‘Datalink In’
and Datalink Out’ parameters. The Datalink functions are enabled by
setting the appropriate dip switches on SW1 and by configuring the
‘Datalink In’ and Datalink Out’ adapter I/O parameters in the SCANport
device.
Each Datalink consists of two 16-bit words of input and two 16-bit words
of output. Each of the two input words can be configured to write to a
different destination parameter inside the SCAnport device by setting the
two ‘Datalink In’ parameters for that Datalink to the desired destination
parameters. Similarly, each of the two output words is configured by
setting the two ‘Datalink Out’ parameters for that Datalink.
If a Datalink is enabled the value of the parameters pointed to by the
‘Datalink Out’ parameters will be transferred to the 1560-MBP.
Conversely, data values sent into the Datalink registers will be written to
the parameter locations configured in the ‘Datalink In’ parameters. If a
Datalink is not enabled, any data sent to the corresponding 1560-MBP
data space will be ignored.
If no ‘Datalink In’ parameter is configured the SCANport device will
ignore it. The same is true for a ‘Datalink Out’ parameter. A zero usually
represents an un-configured Datalink.