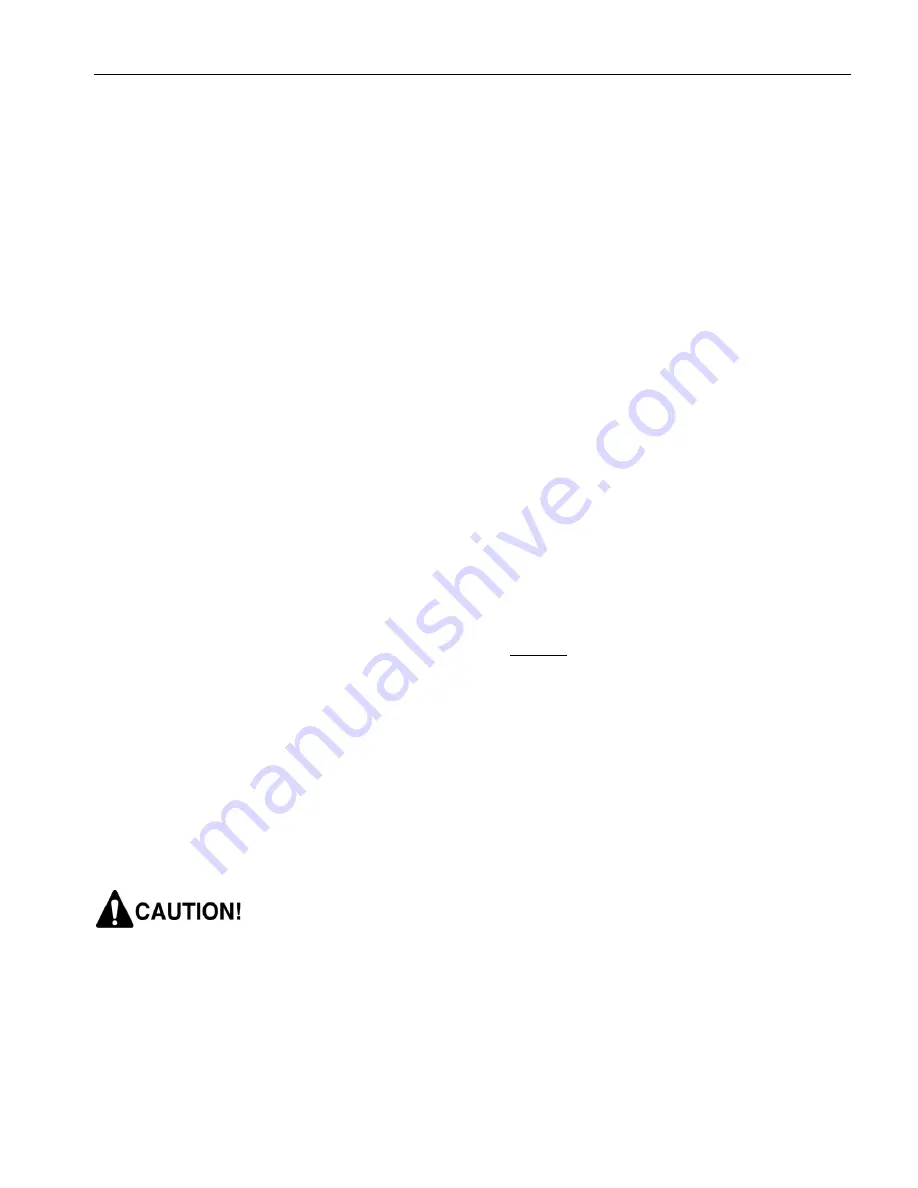
Pro-
Flex 120 Operator’s Manual
29
GREASE SPECIFICATIONS
All greases are not compatible. Grease incompatibility will decrease the lubrication
ability of the grease, and can cause premature part failure.
Grease can have mineral or synthetic base oils and thickening agents such as lithium, calcium,
barium, sodium, or aluminum
What We Use:
- Progressive uses Shell Gadus S2 V220 2
- This grease has: - A mineral oil base
- A lithium-
12 hydroxy thickener (“lithium” thickener)
- Extreme Pressure additives (EP)
- An NLGI Grade 2
Recommended Grease Properties
The grease you use for this machine must have these properties:
NLGI grade 2
Lithium thickener (NOT LITHIUM COMPLEX)
1
Kinematic Viscosity at 40°C is no greater than 220 cSt
Dropping Point Less than 400° F
General Purpose Grease, Not Heavy Duty
No MOLY (molybdenum disulphide) additives in the grease
2
No synthetic grease
3
No High Temperature Grease
4
Notes on grease compatibility:
1) If a thickener other than lithium is used (including lithium complex), the existing grease
will be contaminated and the lubrication properties may be lost leading to component
damage.
2) Molybdenum Disulfide (Moly) is an additive used in slow moving, extreme load
applications. The particles in the “Moly” will actually increase bearing wear in a high
speed mower application. Generally speaking Moly based greases will be grey in
colour.
3) If synthetic base oil is used rather than mineral base oil, the grease will be
contaminated; the lubrication properties may be lost leading to component damage.
4)
We do not recommend the use of “High Temperature” greases, mower component
temperature should never reach temperatures above the level at which general
purpose greases can operate.
“High Temperature” greases may contain thickeners
that are not compatible with Lithium-12 Hydroxy based thickeners.
Grease with these features is considered to be a “General Purpose Grease”. Use on all grease
point locations on your Progressive Mower. Check the properties of the grease you wish to use
with your supplier prior to use.
When performing daily greasing routine, ensure all grass clippings are removed from the
mower decks. Clipping build-up can cause overheating of the bearings and belts
leading to premature wear and subsequent failure.
Содержание TD65
Страница 2: ......
Страница 44: ...42 ...
Страница 52: ...TD65 65 2 Parts Manual 4 1 3 Blade Options 08 2014 ...
Страница 53: ...TD65 TD65 2 Parts Manual 5 1 4 Deck Gearbox Assembly 08 2014 ...
Страница 54: ...TD65 65 2 Parts Manual 6 1 5 Wing Deck Assembly TD65 06 2016 ...
Страница 55: ...TD65 TD65 2 Parts Manual 7 1 6 Wing Deck Assembly TD65 2 06 2016 ...
Страница 56: ...TD65 65 2 Parts Manual 8 1 7 Rear Deck Assembly 08 2014 ...
Страница 57: ...TD65 TD65 2 Parts Manual 9 2 FRAME ASSEMBLY 2 1 Frame Assembly 08 2014 ...
Страница 58: ...TD65 65 2 Parts Manual 10 2 2 Tire Assemblies 08 2018 ...
Страница 59: ...TD65 TD65 2 Parts Manual 11 3 HYDRAULICS 3 1 Hydraulics 08 2018 ...
Страница 60: ...TD65 65 2 Parts Manual 12 4 DRIVELINE 4 1 Driveline 08 2014 ...
Страница 61: ...TD65 TD65 2 Parts Manual 13 4 2 Input PTO Shaft B Model 08 2014 ...
Страница 62: ...TD65 65 2 Parts Manual 14 4 3 Input PTO Shaft D Model 08 2014 ...
Страница 63: ...TD65 TD65 2 Parts Manual 15 4 4 Intermediate PTO Shaft 08 2014 ...
Страница 64: ...TD65 65 2 Parts Manual 16 4 5 Deck PTO Shaft 08 2014 ...
Страница 65: ...TD65 TD65 2 Parts Manual 17 4 6 Deck Gearbox 02 2015 ...
Страница 66: ...TD65 65 2 Parts Manual 18 4 7 4 Way Gearbox 08 2014 ...
Страница 67: ...TD65 TD65 2 Parts Manual 19 5 OPTIONAL EQUIPMENT 02 2017 ...