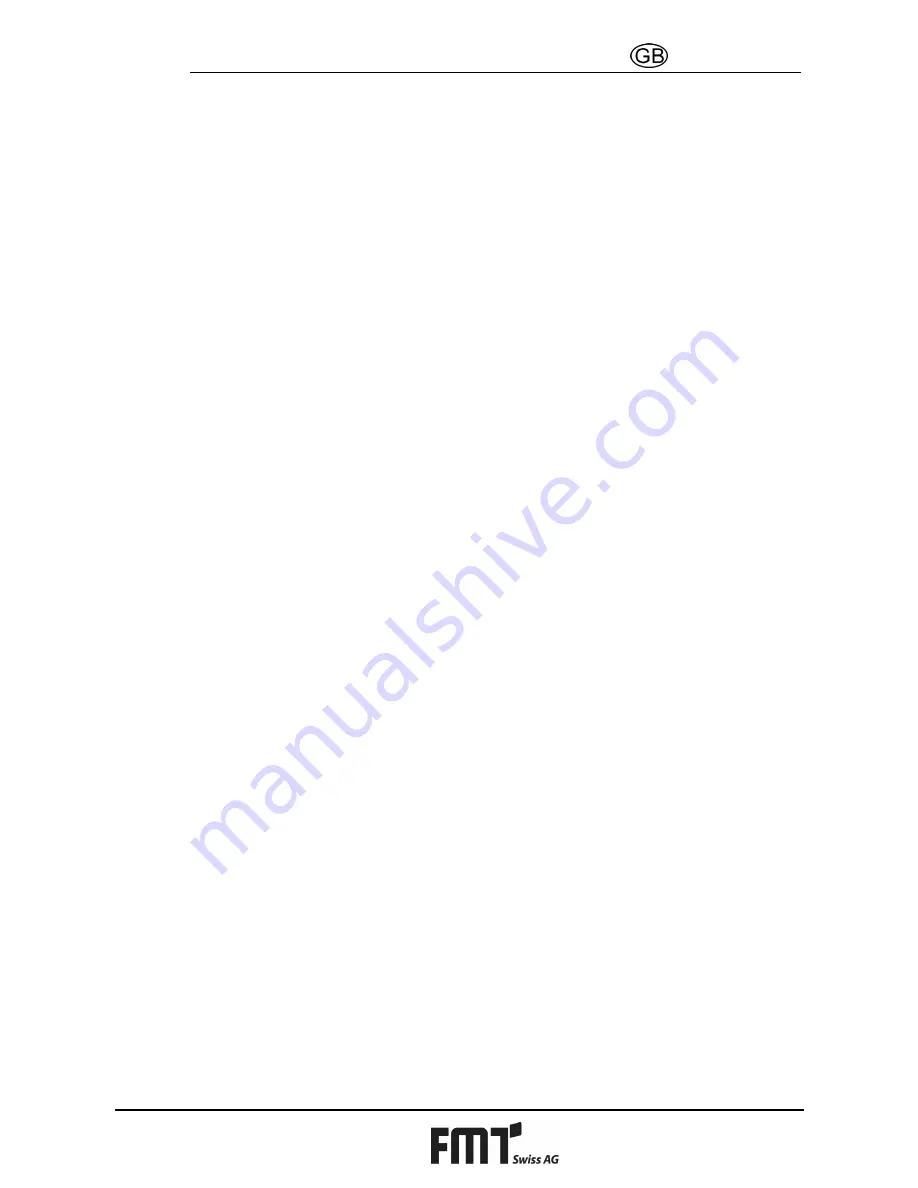
Operating instructions
Oil hose end meter
1.
General details
1.1
Intended use
•
The hose end meter was developed and built for the precise measurement and
determination of volumes of different media having various viscosities.
•
The hose end meter is intended for fitting to the end of a dispensing hose, e.g. a
hose reel.
1.2
Layout and functional description
•
The hose end meter is an oval-wheeled counter with an electronic metering system
and a digital display.
•
The medium flowing through the meter sets two oval cogwheels in rotation,
and this causes two impulses to be passed on to the electronic measuring
mechanism from two reed switches which are displaced with respect to each
other. These impulses are converted by a certain factor into the actual volume
which has flown through, and is shown on the display.
•
The factor has been set by the manufacturer to an average value suitable in
most cases, but if necessary it is simple to reset it to customer-specific
requirements using the pushbutton located in the casing.
•
For the calibratable model, the display and the pushbutton in the casing are
equipped with a lead seal.
•
The total amount is also recorded, and can be displayed by pressing the
'Total' button.
•
Data capture and evaluation are continually monitored electronically, and
errors which may occur are displayed.
•
The electronic measuring mechanism requires a two-phase input signal which
is monitored for phase errors. A self-test is carried out automatically at every
reset.
•
The volume flow can be started and stopped by means of the manually
activated valve positioned upstream of the meter. The anti-drip mouthpiece
fitted below the meter ensures the immediate stopping of the flowing medium,
and prevents after-dripping.
•
Two sealed flush push buttons are all that is needed for operation: Reset and
Total.
•
The electronics are protected against shock and sealed against the entry of
oil. This corresponds to the RFI and EMI shock test conditions.
2