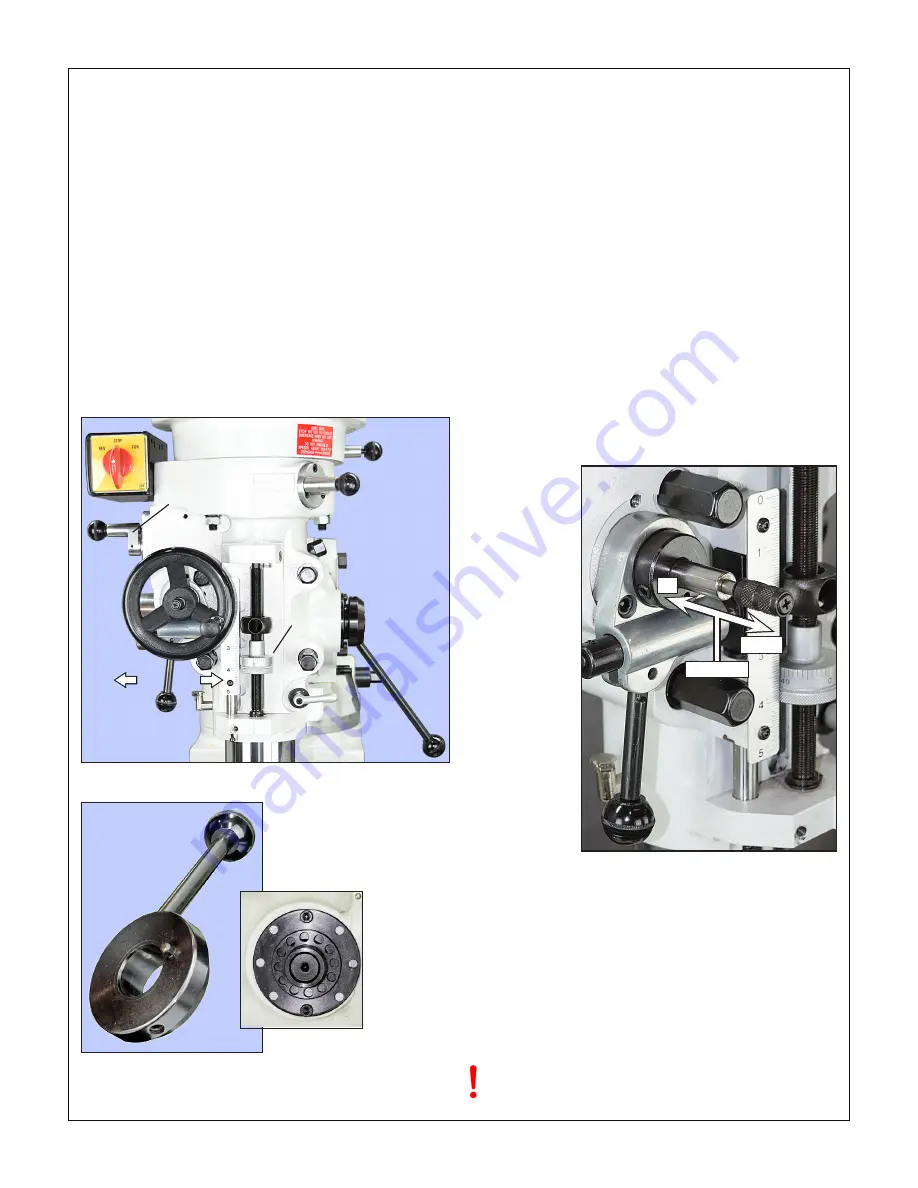
11
Copyright © 2020 Quality Machine Tools, LLC
PM-835S v3 2020-10
QUILL DOWNFEED
The
quill is moved in three different ways: manual
coarse
,
manual
fine
, and
powered
(auto quill feed).
Coarse manual downfeed
In this mode the mill functions like a standard drill press —
lower the quill using the quill manual feed handle, Figure 3-11.
Before operating the manual feed handle, unlock the quill.
Stop the spindle and disengage the quill auto feed (crank at
right of the head).
The feed handle hub, Figure 3-12, is held on the quill pinion
shaft by a spring-loaded ball and a detent groove on the outer
end of the shaft. A pin on the hub locates in one of 12 holes in
an index plate keyed to the shaft.
To reposition the manual feed handle relative to the index
plate, pull the hub about 1/4” away off the plate, then re-index
the hub to a different location.
Figure 3-12
Quill manual feed handle and index plate
Quill manual
feed handle
Quill auto
feed ON/OFF
(engaged/dis-
engaged)
Feed rate
selector
ON OFF
Figure 3-11
Quill controls
Fine feed handwheel
Quill lock
Micrometer
depth stop
Quill auto
feed lever
Fine manual downfeed
For milling operations calling for better control of tool depth,
use the fine feed handwheel.
1. With the spindle
stationary
, disengage the quill auto feed
(crank at right of the head).
2. Unlock the quill.
3. Set the quill auto feed direction plunger to neutral (mid
position), Figure 3-13.
4. Swing the quill auto feed lever to the left.
The quill is now under handwheel control.
NOTE 1:
Clockwise rotation of the handwheel causes the quill
to descend.
NOTE 2:
The handwheel is often removed for better visibility
of the micrometer scale.
NOTE 3:
In common with other knee mills there is no indica-
tion of down feed amount unless a DRO is installed on the
quill. Most users control cutting depth by locking the quill then
raising the knee in precise increments.
Figure 3-13
Auto feed direction plunger
Moving the plunger from fully in to fully out reverses feed direction.
The center position is neutral, no down feed. UP and DOWN direc
-
tions here apply to clockwise spindle rotation — vice-versa for count
-
er-clockwise rotation.
UP
DOWN
NEUTRAL
QUILL AUTO FEED
The auto feed system can be set to drive the quill either up or
down at a choice of three speeds, Figure 3-14. A clutch mech-
anism disables the drive when overloaded (as shipped, the
clutch is adjusted for a drilling capacity of about 3/8” in mild
steel).
Be sure the quill is unlocked before auto feeding