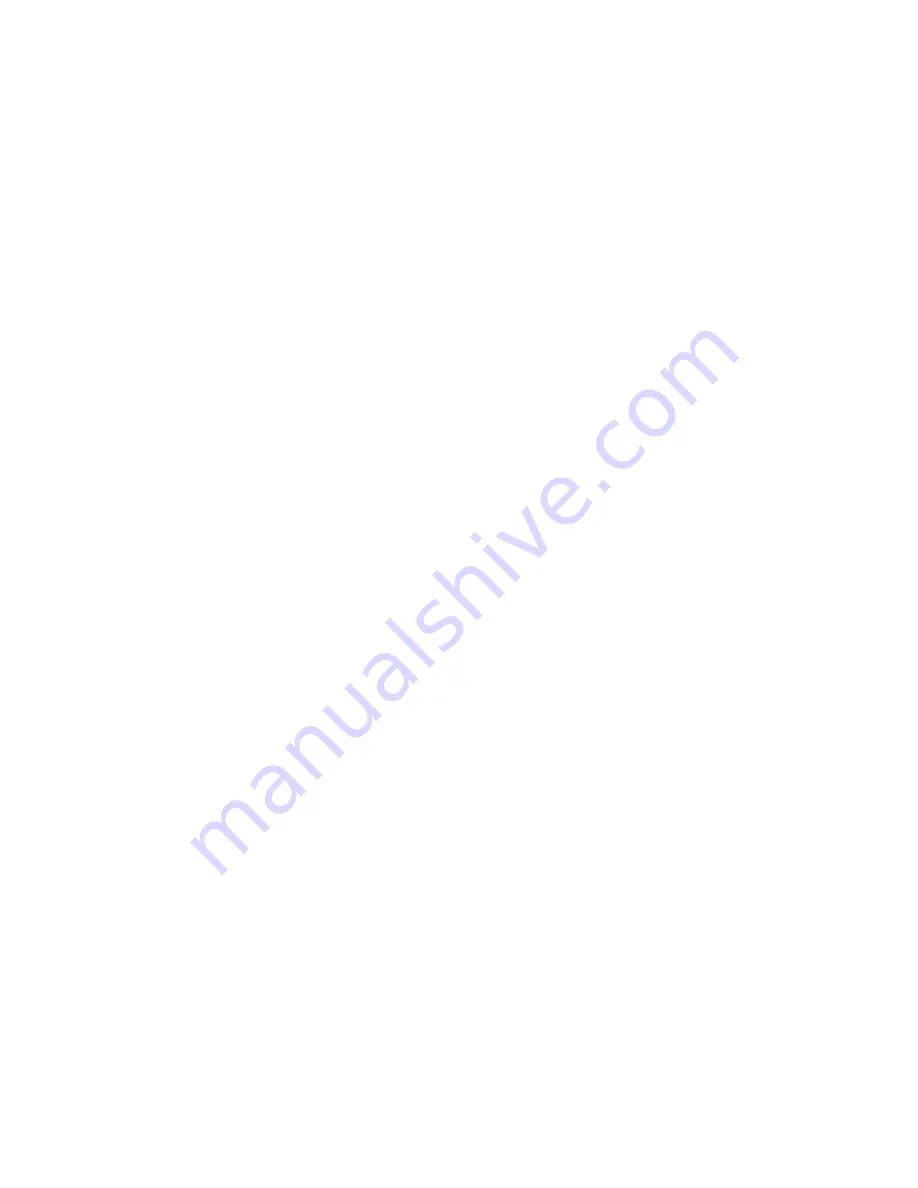
Headstock
The headstock is located on the operator's left end of the lathe
bed. It contains the main spindle, the part of the lathe that
rotates, an oil reservoir and the mechanism for obtaining various
spindle speeds and for transmitting power to the feeding and
threading mechanism.
The headstock mechanism is driven by an electric motor
connected to a belt pulley and gear system.
The main spindle is mounted on bearings in the headstock and is
hardened and specially ground to fit different lathe holding
devices. The spindle has a hole through its entire length to
accommodate long workpieces. The hole in the nose of the
spindle has a standard #5 Morse taper (MT5).
Centers, collets, drill chucks, tapered shank drills and reamers
may be inserted into the spindle. Chucks, drive plates, and
faceplates may be mounted onto the spindle nose.
Spindle speed is controlled by the variable speed switch and
Hi/Low belt position.
Содержание PM-1127VFI-LB
Страница 1: ...Spartan Robotics Lathe Safety Training Manual...
Страница 5: ......
Страница 7: ...Headstock Controls...
Страница 9: ...Carriage Controls...
Страница 13: ...Tooling Examples...