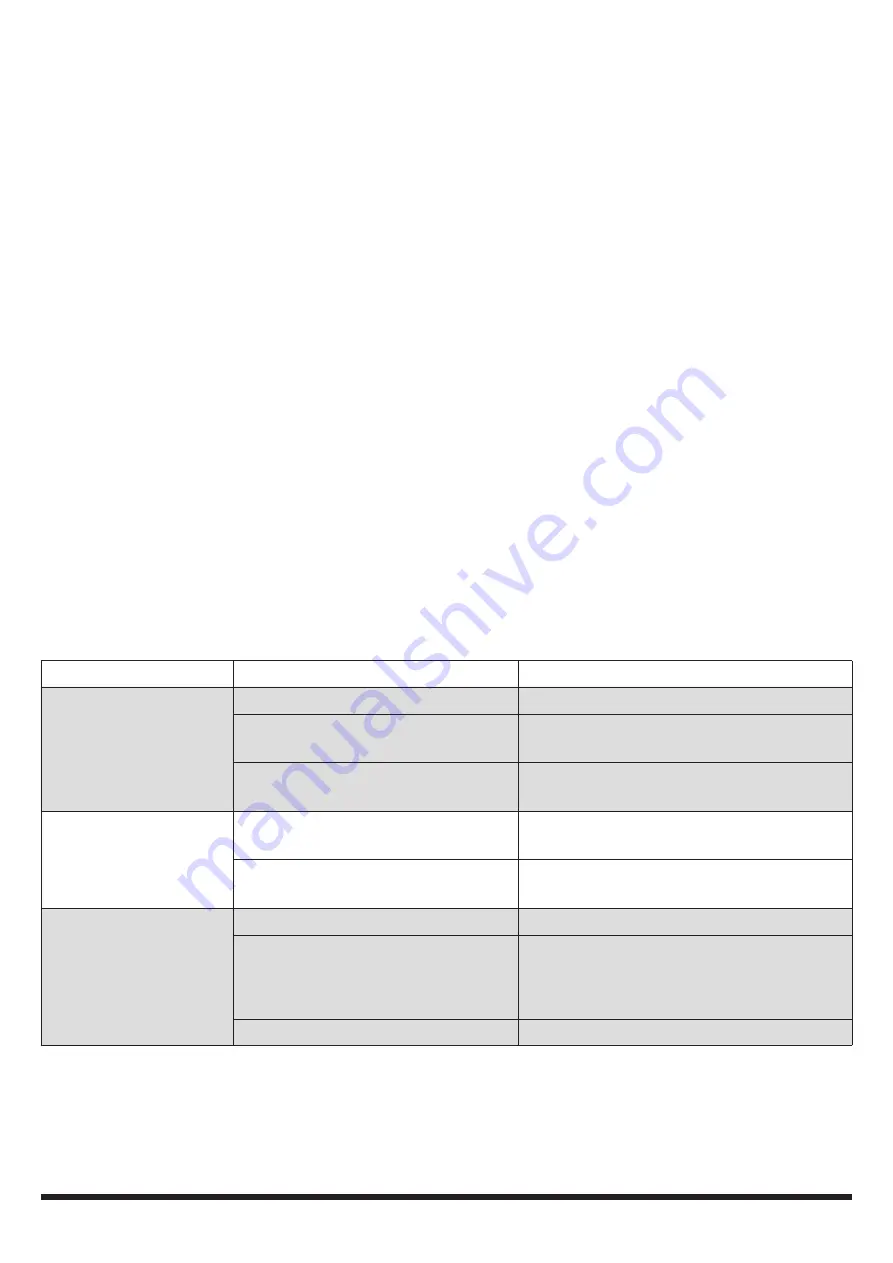
10
For technical questions call 1-800-665-8685
V 3.05
8474116
20 Gallon Pressure Abrasive Blaster
CAUTION! Make sure that the tank has been depressurized before attempting to remove the tank filler
cap (12).
WEAR CONDITIONS
This is usually noted when an excessive amount of dust appears while blasting. Dust will occur if:
1. The abrasive blasting media is worn out if it has lost its granular or spherical appearance or has a lot of
debris mixed in from the parts being blasted. Replace the abrasive blasting media. This is usually noticed
when the abrasive media that exits the nozzle resembles more of a cloud than a stream.
2. The deadman valve parts may wear out. This is usually evident when the blast pattern is too wide and
ineffective; simply replace the nozzle or orifice.
LUBRICATION
Do not use lubricants or air tool oil on the unit. The oil will contaminate the abrasive media, clogging the tool and
reducing the effectiveness of the abrasive.
STORAGE
With a dry, clean cloth or brush, remove any contaminants from the unit and the deadman valve before placing the
unit in storage.
DISPOSING OF THE TOOL
1. If your tool has become damaged beyond repair, do not throw it out. Take it to the appropriate
recycling facility.
2. Abrasive can be re-used until it eventually breaks down or becomes dusty. Dispose of waste abrasives in
accordance with local authority regulations.
TROUBLE SHOOTING
Problem
Possible Cause(s)
Suggested Solution(s)
Excessive dust
while blasting.
1.
Abrasive media may be worn.
1.
Replace the abrasive media.
2.
Too much abrasive media in
the hopper.
2.
Remove excess abrasive media.
3.
Loose air line or fitting connection. 3.
Tighten the fitting and make sure the air
lines are secure.
Uneven blasting action.
1.
Too much abrasive media in
the hopper.
1.
Remove excess abrasive.
2.
Moisture is present while blasting. 2.
Check the air line to make sure that there
is no moisture in it.
Inadequate speed or
inefficiency of blast.
1.
Abrasive media may be worn.
1.
Replace the abrasive media.
2.
Pressure is too low.
2.
Increase the inlet pressure.
WARNING! Do not exceed the maximum
pressure of 125 PSI.
3.
Worn nozzle.
3.
Replace the nozzle.