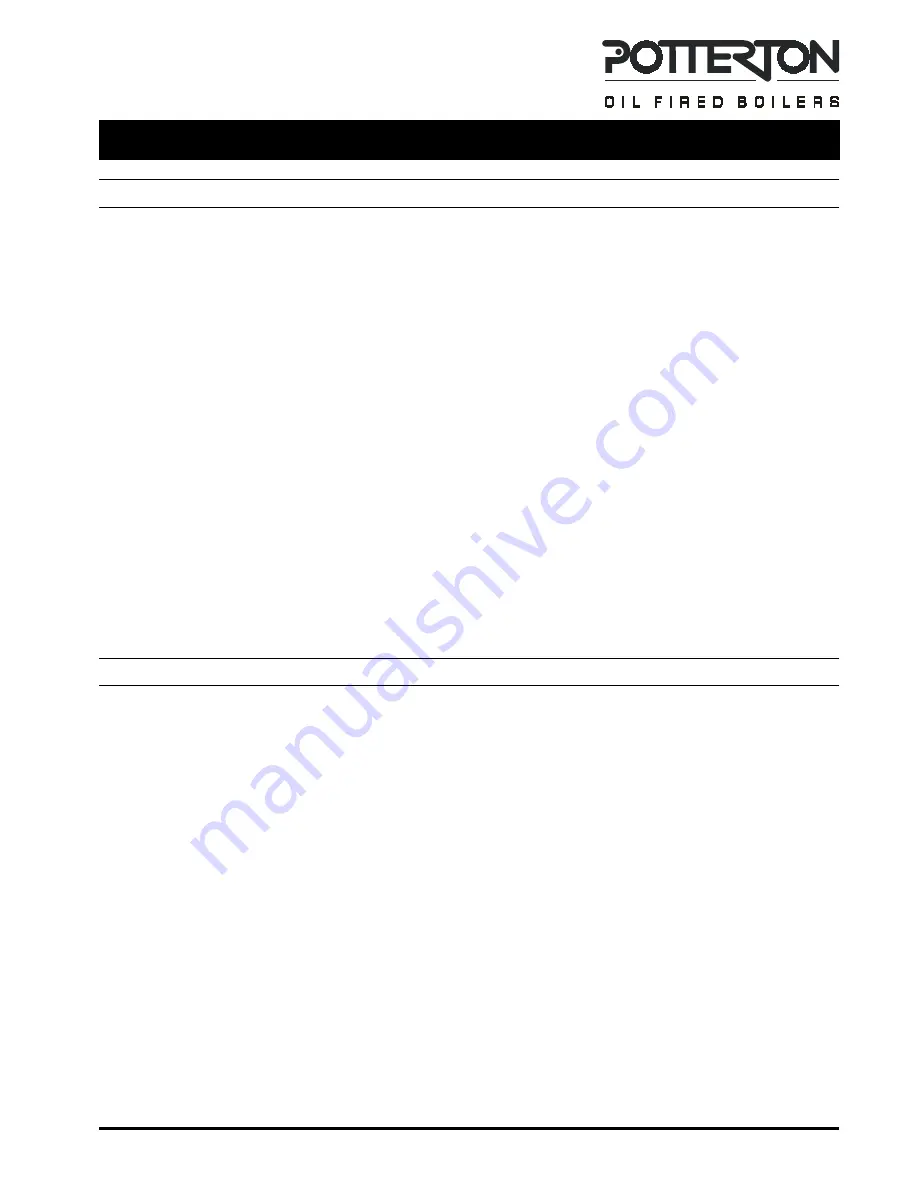
Part No. 5102478
47
Fault Finding
5 - Fault Finding
SYMPTOM
CHECK LIST
ACTION
Burner Does Not
Start, Motor Does
Not Run
1. Mains switched on
Switch on
2. Fuse in switch
Fit a fuse
3. Fuse blown
Replace fuse
4. All external controls call for heat
Set to call for heat
5. Boiler stat calls for heat
Set to an “ON” position
6. Limit stat tripped - Light on
Reset limit stat
7. Boiler at lock out - Light on
Reset
8. Faulty external wiring
Repair if necessary
9. Faulty external controls
Check that they are operating
10. Burner control box faulty
Check by fitting spare box
11. Boiler control panel wiring faulty
Check & refer to wiring diagram
Section 1
12. Burner motor seized
Remove and check ease of rotation
SYMPTOM
CHECK FOR
ACTION
Boiler Starts,
No Flame
Established,
No Oil To Burner
1. Oil in the tank
Re-Fill
2. All valves open from tank to burner
Open valves
3. Fire valve correctly set
Set as per manufactures instructions
4. Filter blocked
Clean and replace elements
5. Air lock in fuel lines
Bleed burner
6. Nozzle blocked
Replace nozzle
7. Pump pressure correct
Set to correct pressure refer to
Burner Instructions
8. Pump rotates:- Is it correct
Dismantle pump from Motor
for either one or two pipe
and check freedom of rotation
9. Pump drive coupling faulty
Remove pump and examine
coupling for signs of wear and
damage, refer to Burner Instructions
10. Solenoid valve not opening
Check operation of the solenoid
valve
Содержание Statesman 45/50
Страница 30: ...30 Part No 5102478 Installation Commissioning Fig 21 ...
Страница 31: ...Part No 5102478 31 Fig 22 Installation Commissioning ...
Страница 32: ...32 Part No 5102478 Installation Commissioning Fig 23 ...
Страница 35: ...Part No 5102478 35 Fig 25 Installation Commissioning ...
Страница 45: ...Part No 5102478 45 Servicing Maintenance Fig 31 ...
Страница 46: ...46 Part No 5102478 Servicing Maintenance Fig 32 ...
Страница 51: ...Part No 5102478 51 Notes Notes ...