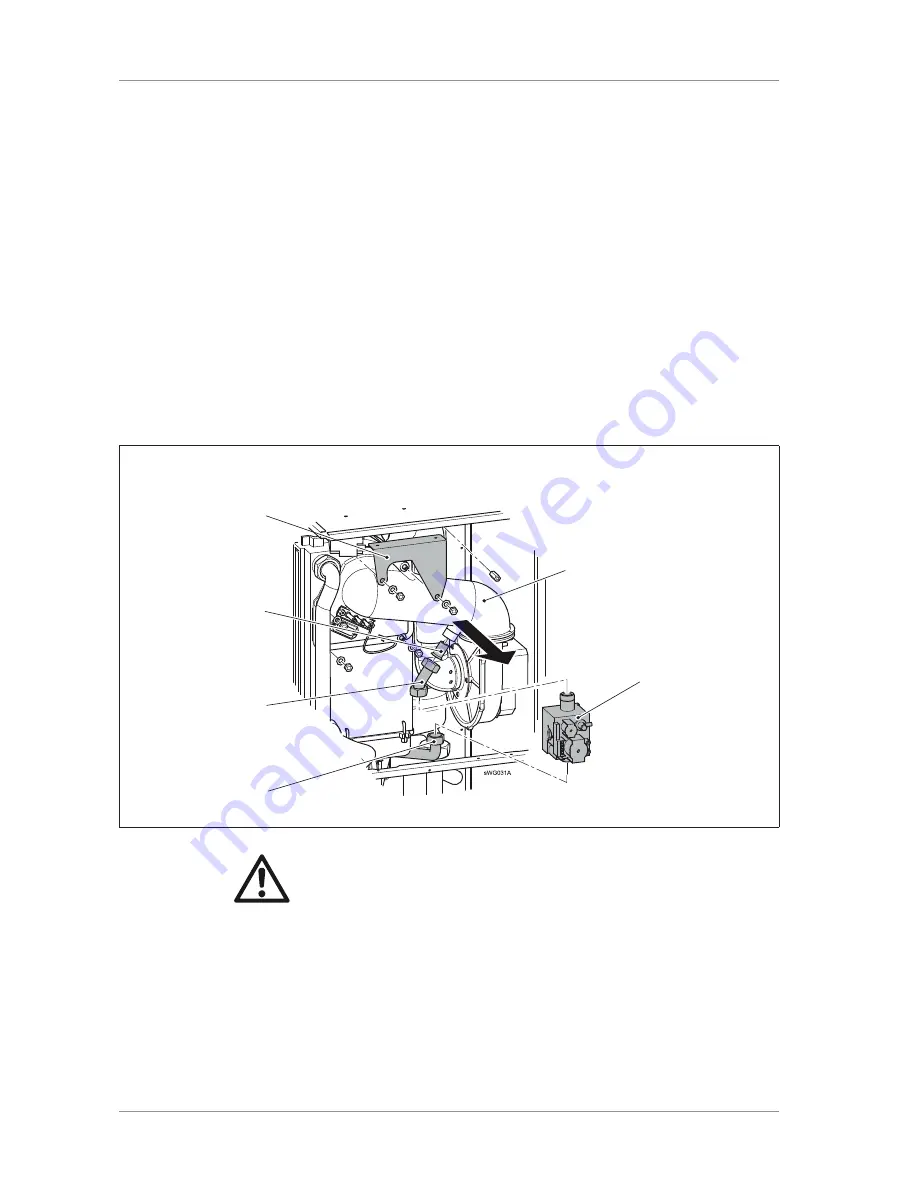
Servicing
64
POTTERTON COMMERCIAL
120
-393 632
.4 04.08 F
h
Dismantling of the gas burner (PARAMOUNT two 60 D)
• Disconnect the connecting lines to the fan.
• Disconnect ionisation line.
• Disconnect ignition cable.
• Disconnect fastening screws of the bracket on the housing lid.
• Disconnect the screw connections of the gas connection pipe at
the mixing chamber and the gas valve.
• Remove the gas connection pipe and the gas injector.
• Disconnect the gas connection pipe at the gas valve and remove
gas valve.
• Undo the 5 fastening screws at the mixing chamber/heat ex-
changer.
• Remove bracket.
• Pull out the burner together with mixing chamber, fan and ea-
haust gas muffler to the front (see figure 19)siehe Abb. 20
• Clean burner pipe with soft brush.
Use new seals when installing.
Fig. 20: Dismantle of the gas burner (PARAMOUNT two 60 D)
Pull out burner with mixing
chamber and flue silencer.
Remove bracket.
Remove gas valve.
Remove gas injec-
tor.
Remove gas con-
nection pipe.
Disconnect gas
Содержание Paramount two
Страница 8: ...Safety 8 POTTERTONCOMMERCIAL 120 393 632 4 04 08 Fh 2 6 Conformity declaration Paramount two 30 115 ...
Страница 14: ...Technical Data 14 POTTERTONCOMMERCIAL 120 393 632 4 04 08 Fh 3 4 Wiring diagram ...
Страница 20: ...Before installation 20 POTTERTONCOMMERCIAL 120 393 632 4 04 08 Fh Connection plan ...