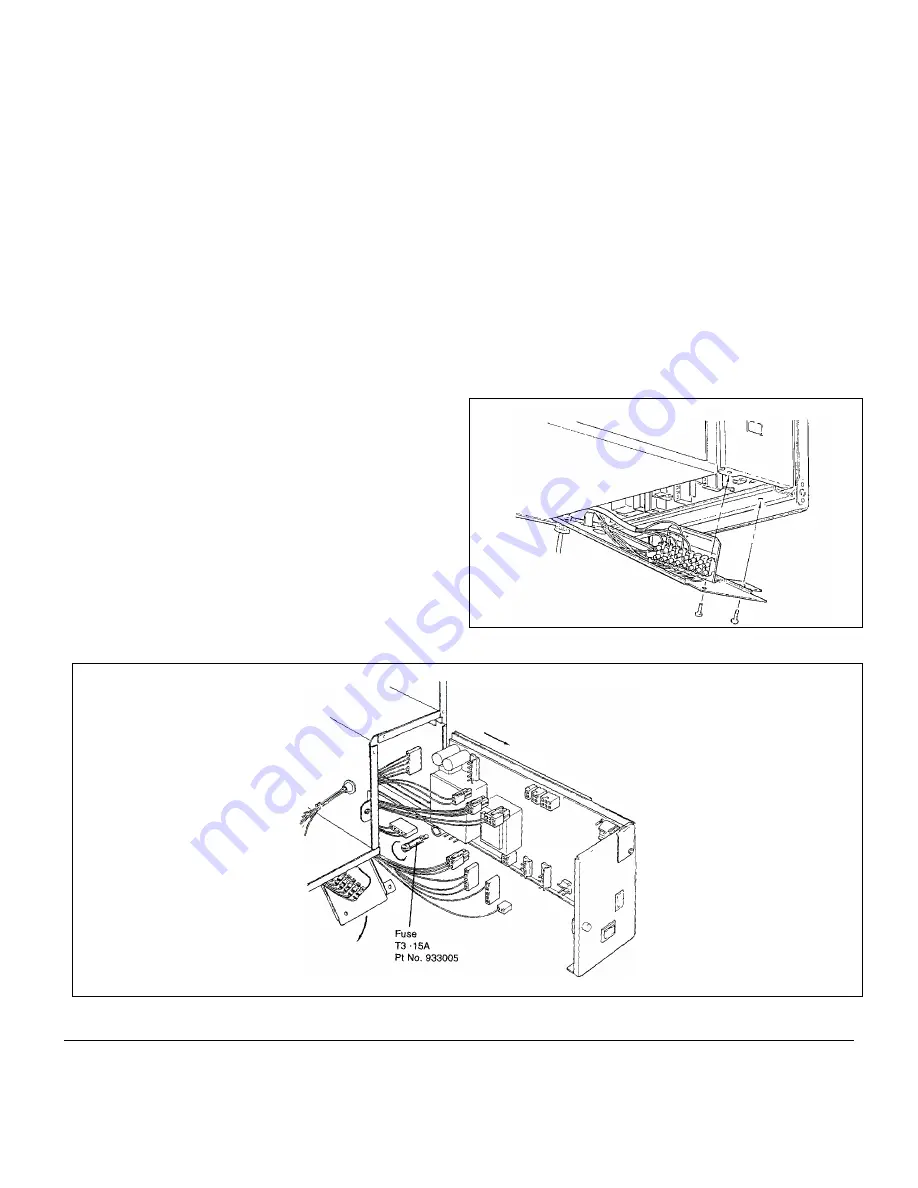
26
SERVICING & REPLACING PARTS – Page 26
14) BOILER CONTROL BOARD.
IMPORTANT
Before replacing the control board refer to fault
finding section of these instructions. The control
should only be replaced if the diagnostic display
indicates it is faulty.
a)
Remove decorative and functional doors as
described in “Servicing Boiler”.
b)
Remove screw retaining access door on under side
of boiler. FIG. 22.
c)
Remove screw retaining control front panel and tray.
FIG. 22.
d)
Gently pull front panel forward removing connectors
from the control as they become accessible. FIG. 23.
15)
BOILER CONTROL BOARD FUSES.
a)
Remove decorative & functional doors as described in
“Servicing Boiler”.
b)
Remove screw retaining access door on under side of
boiler. FIG. 22.
c)
Remove screw retaining control front panel and tray.
FIG. 22.
d)
Gently pull front panel forward removing connectors
from the control as they become accessible. FIG. 23.
e)
Remove old fuse and replace with the correct Potterton
component T3 ISA Pt 933005.
f)
Replacement is the reverse of removal.
e)
Remove tray from boiler and carefully remove
retaining screws at the rear of the control tray, single
M4 and washer nut on the top of the control and
plastic fixings holding the board to the tray.
f)
Replacement is the reverse of removal. Ensure that
M4 nut and washer used to earth the control tray is
refitted.
FIG. 22 REMOVING CONTROL SECURING SCREWS
FIG. 23 REMOVING CONTROL TRAY
Содержание envoy 30
Страница 4: ...4 TECHNICAL DATA PAGE 4 FIG 2 GENERAL ARRANGEMENT ...
Страница 28: ...28 FAULT FINDING CHART 1 Page 28 ...
Страница 29: ...29 FAULT FINDING CHART 2 Page 29 ...
Страница 30: ...30 BOILER INTERNAL WIRING Page 30 ...
Страница 31: ...31 BOILER WIRING LAYOUT Page 31 ...
Страница 36: ...36 Back Page ...