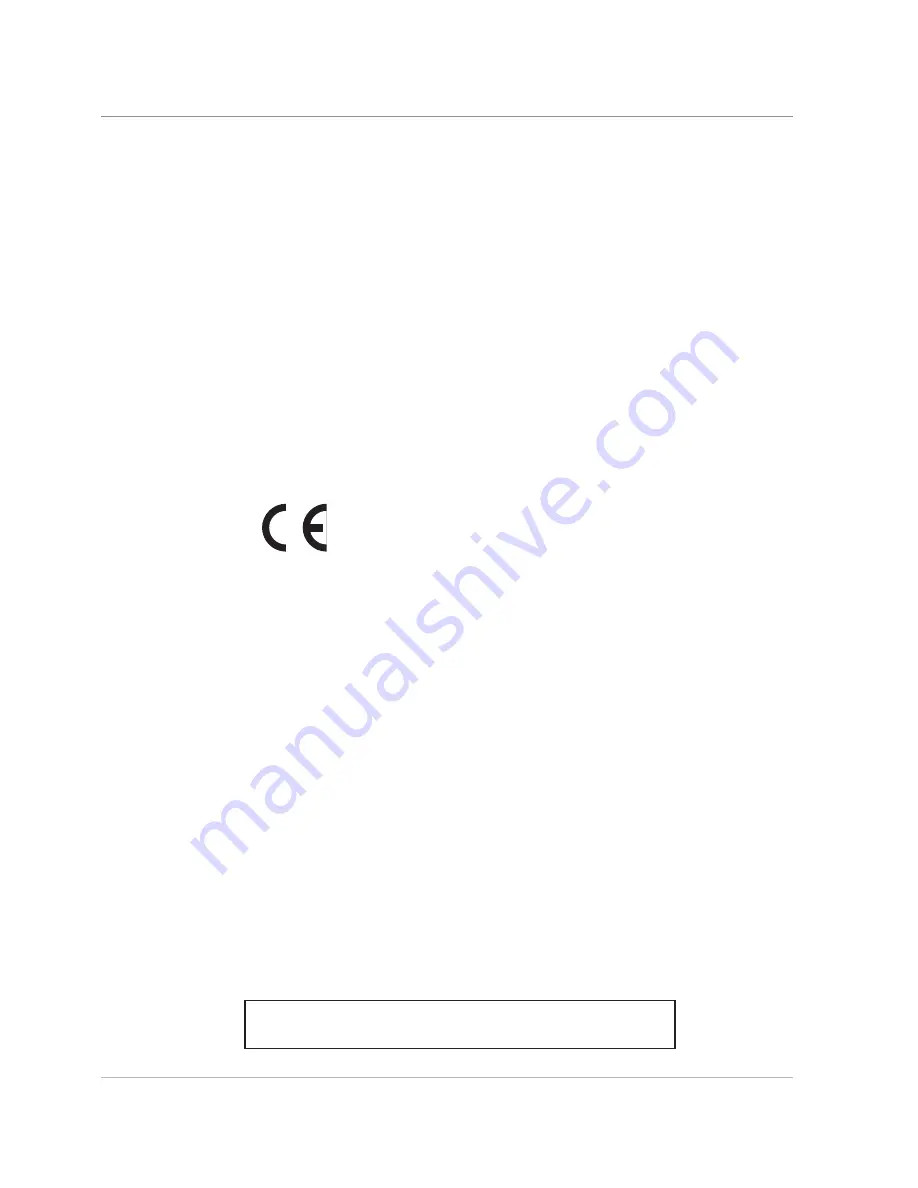
2-4
SDT333A DI380/DI425/SI3300/SI3500 Service Manual
2 • Specifications
2.2
MAcHINe sPecIFIcATIONs
Physical Dimensions
DI380/sI3300
DI425/sI3500
Length
773mm
1043mm
Depth
568mm
568mm
Height
525mm
525mm
Weight
55kg
65kg
Weight will depend on machine configuration. Weights stated do not include material.
Noise Level
Running
73dBA
electrical
230VAC, 50Hz, 3A
or 110VAC, 60Hz, 6A
Maximum speed
DI380/SI3300 - Up to a maximum of 3,000 cycles per hour
DI425/SI3500 - Up to a maximum of 3,500 cycles per hour
Depending on model, fold type and material quality.
compliance
It is certified that the Folding/Inserting machine complies with the
requirements of the Low Voltage Directive 73/23/EEC and the EMC
Directive 89/336/EEC. The product was tested in a typical configuration.
For a formal Declaration of Conformity please contact Compliance
Engineering on +44 (0)1279 426731.
ALL sPecIFIcATIONs ARe sUBJecT TO cHANGe WITHOUT
NOTIFIcATION AND ARe sUBJecT TO TesT
Содержание DI380 Series
Страница 32: ...3 18 SDT333A DI380 DI425 SI3300 SI3500 Service Manual 3 Theory of Operation ...
Страница 50: ...4 18 SDT333A DI380 DI425 SI3300 SI3500 Service Manual 4 Removal Replacement ...
Страница 66: ...5 16 SDT333A DI380 DI425 SI3300 SI3500 Service Manual 5 Adjustments ...
Страница 102: ...7 22 SDT333A DI380 DI425 SI3300 SI3500 Service Manual 7 Service Menu Troubleshooting ...
Страница 114: ...10 8 SDT333A DI380 DI425 SI3300 SI3500 Service Manual 10 Diagrams 10 5 drive belt routing Rear View Front View ...
Страница 122: ......