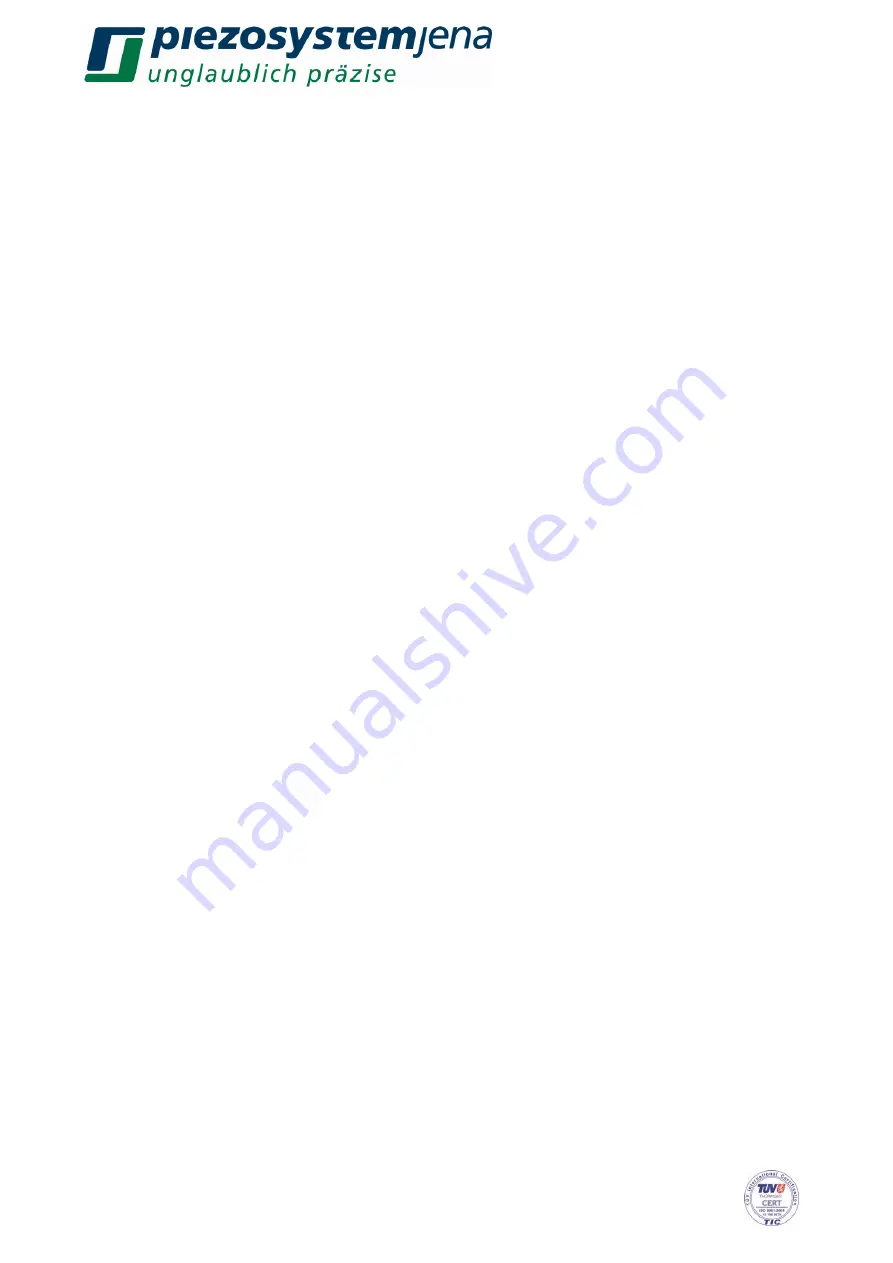
Geschäftsführer: Dr. Bernt Götz • Telefon 03641/66880 • Fax 03641/668866 • www.piezosystem.com
60
10 controller adjustment
When any actuator made by
piezosystem jena
is connected to the
30DVxxx
, amplifier their
specific values are read from the actuator
’s ID-chip. The Digital Signal Processor (DSP) of the
amplifier is set with these values. These parameters were investigated in the
piezosystem jena
laboratory and ensure safe function of the actuator.
There are no kp-, ki-, and kd-values for actuators without a measurement system because the
closed loop mode is impossible in this configuration. Closed loop is automatically switched off.
To adapt the controller properties to your special application please start with the default values. At
first please switch on the closed loop mode by pressing the
encoder knob “OFFSET” or by the
command
cl,1
via RS232. Change one parameter step by step and check the result with the
oscilloscope on the ANALOG 9pin SUB-D socket of the amplifier. You must install a monitoring
output to
position value in open loop
with the command
monsrc,6
.
In general, change the parameters in small steps and, depending on the actuator's reaction,
slightly increase the step width. If the system begins to oscillate, switch off the closed loop
immediately by pressing the encoder knob, then reset the last values entered!
First of all, check the function of the notch filter. This has been factory adjusted so that the main
resonant frequency is suppressed in an actuator with standard mass loading. If your application
has a different mass, the resonant frequency changes (higher mass = lower frequency). The notch
parameters are adjustable with the commands
notchon
,
notchf
and
notchb
.
The sweep function of the internal function generator can be used to determine the resonant
frequency. Use
function generator
in the
choose menu
of the actuator. Set the amplitude to 5%,
the offset to 0%, and the sweep time to 1 (1sec/decade). Set the amplifier to open loop (
“OL/CL”
LED lights green). With the MOD/MON cable (MON plug) you can connect the oscilloscope to the
ANALOG socket of the amplifier. The following adjustments on the oscilloscope are required: store
function, time base = 0.5 sec/div and input voltage = 0.1V/div. The display shows the response of
the actuator measured by the integrated measurement system. Before the measured curve swings
out, there is a position where the amplitude is 0 Volts. This is the adjusted notch frequency. At the
resonant frequency, the measured curve goes very high. At this point you have to adjust the notch
frequency to the resonant frequency to linearize the curve. Using the notch filter might increase
noise.
The correct ki-value is determined as follows:
In the
function generator
menu,
set rectangle to 1 Hz, amplitude to about 50%, and offset to 25%.
Please set the monitoring output to
Umes/CL
in the
analog i/o
menu. The following adjustments
on the oscilloscope are required: store function, time base = 0.05sec/div and input
voltage = 1V/div. Set the amplifier to closed loop (
“OL/CL” LED lights yellow). The oscilloscope
display shows the step response of the actuator measured by the integrated measurement system.
If the slew rate is too low, please increase the ki-value in the
digital controller
menu. The over
swing after the rise time should be smaller than 1% of the total step.
In these adjustments, the actuator system can begin to oscillate in resonant frequency.
Please switch off the closed loop immediately by pressing the
encoder knob “OFFSET”.
Then reset the last values entered! Continuous use at resonance can damage the actuator!
Now you can try to increase the slew rate in
slew rate/filter
menu
,
as long as no oscillation or
large over swing occurs.