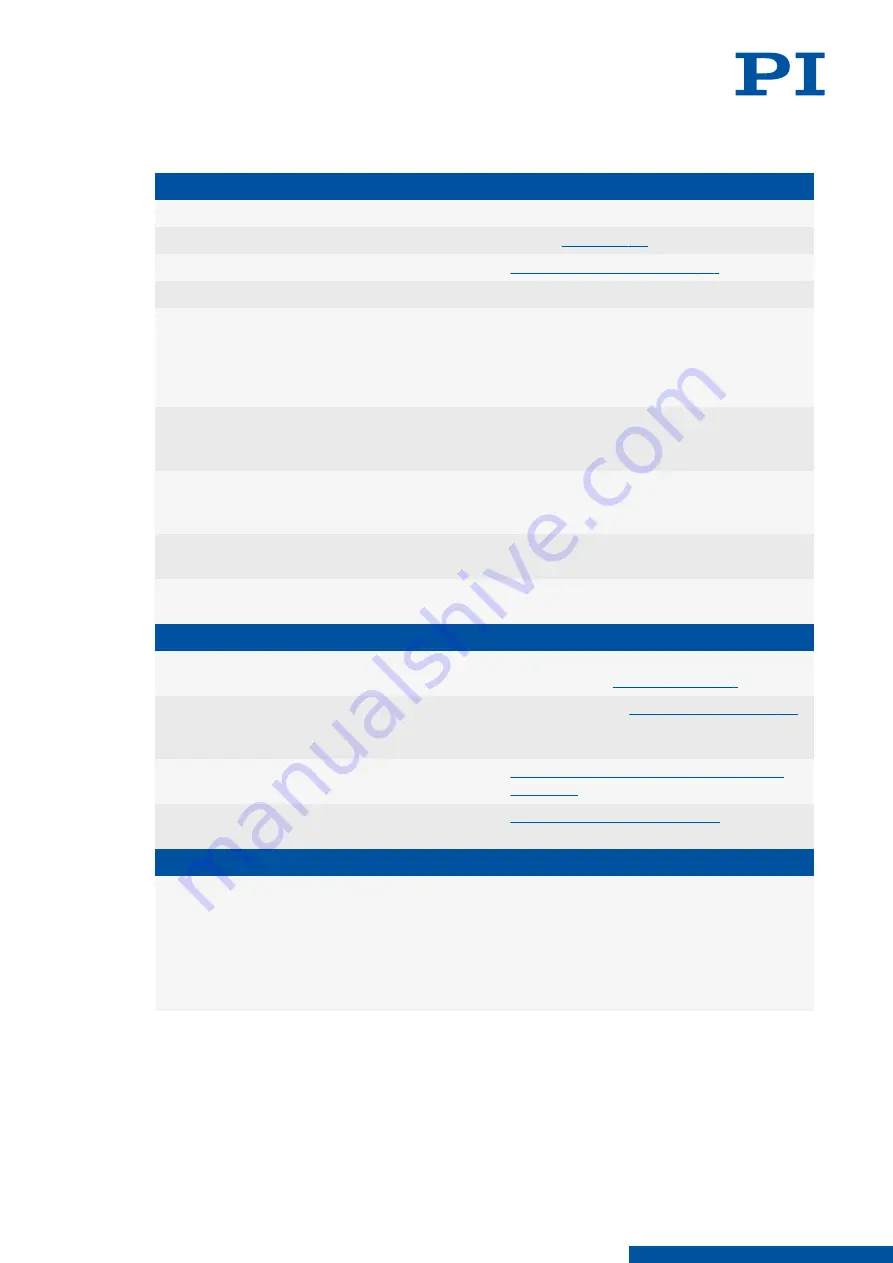
9
Troubleshooting
The positioner does not move
Cable not connected correctly
►
Check the cable connections.
The electronics or mechanics were replaced
►
Run the
once again.
Electronics not connected correctly
►
Check all connecting cables (p. 21)
.
Defective electronics
►
Check the electronics.
Motion platform has triggered the limit
switch
►
If you are using a controller from PI: Switch on
the servo mode for the affected axis again in the
PC software.
►
Command the axis to move away from the limit
switch.
The positioner was connected to the switch-
ed-on electronics
►
Switch the electronics off and on again or restart
them with the
RBT
command or with the corre‐
sponding PC software function.
Incorrect configuration
►
Check the L‐417.xx9025E1's parameter settings
in the electronics connected and make the ap‐
propriate corrections.
Incorrect command or incorrect syntax
►
Send the
ERR?
command in the PI electronics
and check the error code .
Incorrect axis or channel commanded
►
Make sure that the electronics use the correct
axis respectively channel identifier.
Reduced positioning accuracy
Excessive load
►
Do not exceed the maximum permissible loads
according to the
When the L-417.xx9025E1B is mounted verti-
cally: Load exceeds the holding brake's hold-
ing force
►
Make sure that the
is not exceeded.
Warped base body
►
Mount the L‐417.xx9025E1 onto an even sur‐
Increased wear due to small motion over a
long period of time
►
Perform a maintenance run (p. 25)
Uncontrolled oscillation
Large changes to the load or the alignment
of the L-417.xx9025E1
►
Switch off the servo control system or the con‐
troller immediately.
►
Check whether the servo control parameter set‐
tings correspond to the selected closed‐loop
control mode; see user manual for the controller.
►
If necessary, correct the settings of the servo
control parameters.
9 TROUBLESHOOTING
L417UM0002EN
‒
10/25/2022
27
M O T I O N | P O S I T I O N I N G