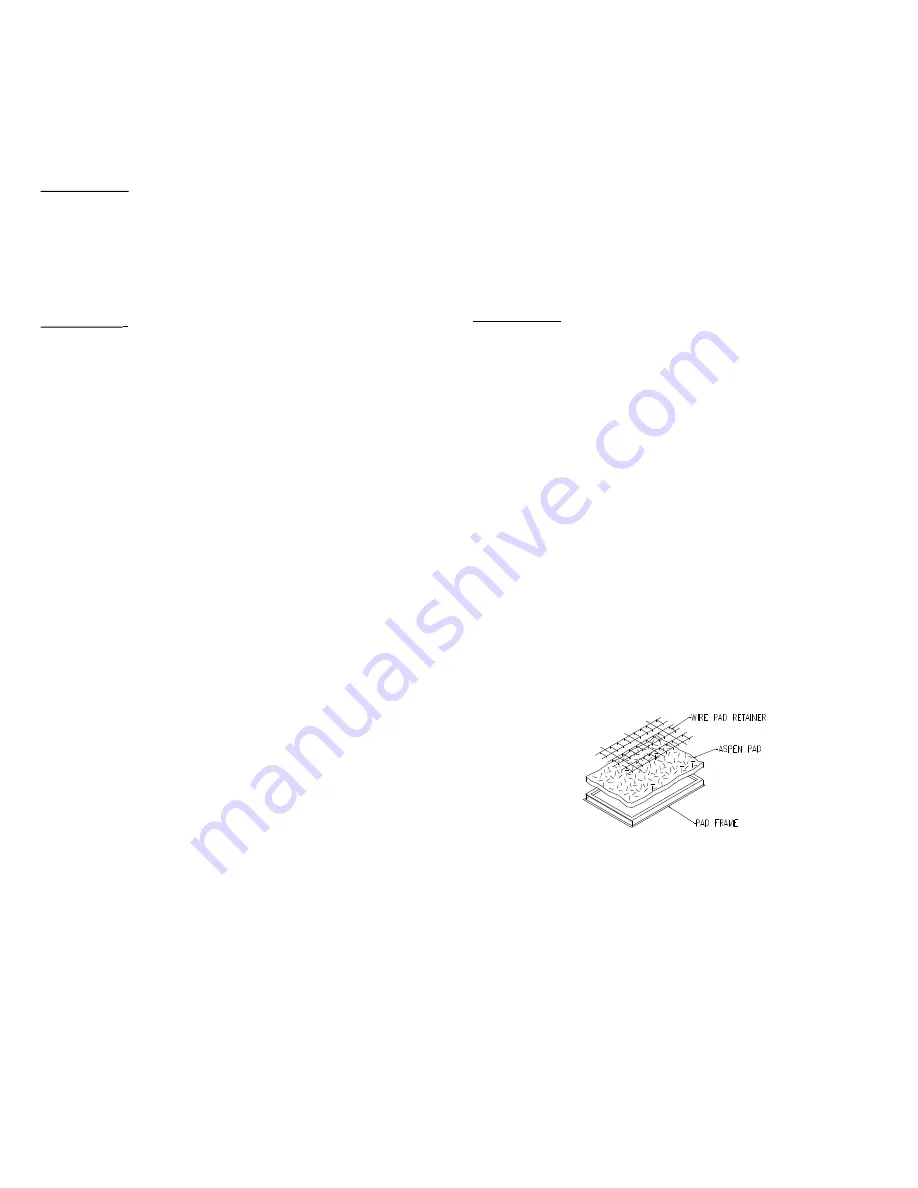
Blower Shaft Bearings
D/H8801 or D/H1425 - Blower shaft bearings need periodic
lubrication. They should be checked 20-30 days after initial start-up of
operation. The oil cups on the bearings should be filled with a good
grade of SAE 20W or 30W non-detergent oil when necessary. Under
normal use, oiling is required every three months of operation.
Do Not
Over- Oil.
D2231A or H2231 Blower shaft bearings are sealed and do not
require oiling.
Pump Motor Bearings
The pump motor does not require lubrication.
Changing Cooler Pads
CAUTION:
Disconnect all electrical power to the cooler
before attempting to install, open, or service your cooler.
More than one disconnect will be required to de-energize
the equipment for servicing. If the cooler is
thermostatically controlled, the thermostat is not to be
used as the power supply disconnect, as it may reset and
start the unit unexpectedly.
Your cooler pads should be changed at least twice a year… at the
beginning of a season and midway through. However, your pads may
need to be changed more frequently, depending on local air and water
conditions. For instance, in areas where mineral content of the water
is high, deposits may build up in the cooler pads, restricting airflow.
Replace pads as follows:
!
Remove pad assembly from cabinet.
!
Remove pad retainers from frame, using caution as retainers can
spring back. Carefully remove all aspen from retainers. Remove
and discard old pads.
!
Using a mild detergent, wash dirt and scale from pad frames.
Wire brushing is not recommended. If finish is damaged or
rusting is noted, repair area as noted in the “Touch-Up” section.
Rinse with fresh water.
!
Lay new pad in frame, starting at trough end, making sure pad is
snug against trough and outer edges with no air spaces.
Note
:
New pad must completely fill frame (no gaps) or hot air may enter
building.
!
Pad thickness should be uniform across the frame.
!
Replace pad retainers and lock under edge of frame. Sharp
points must be buried into pad (they hold pad in place and prevent
sagging).
!
Pre-soak pads and check for air gaps along edges, reinstall pad
frames into unit.
!
Start pump and allow troughs to fill… check water level in troughs
by slightly tilting each pad frame out.
REPLACEMENT PARTS
When ordering replacement parts, always refer to the serial and
model number of your cooler. Use the part numbers listed in the
accompanying parts list, as illustrated in the diagrams for your model.
Adjust Belt Tension
Each time you inspect your cooler, be sure to check belt tension on
motor/blower assembly. Check belt condition and replace it if frays or
cracks appear. Check alignment of blower pulley with motor pulley
Cleaning Water Pump & Hose
CAUTION:
Disconnect all electrical power to the cooler
before attempting to install, open, or service your cooler.
More than one disconnect will be required to de-energize
the equipment for servicing.
If the cooler is
thermostatically
controlled, the thermostat is not to be
used as the power supply disconnect, as it may reset and
start the unit unexpectedly
.
CAUTION
: Do not allow pump to fall over and become
submerged; water will damage pump motor.
Clean water pump and hose assembly as follows:
!
Unplug pump cord, remove mounting bracket screw and
remove pump from cooler. Shake gently to remove water.
!
To prevent breakage, carefully release the five snap-out tabs
in order noted on base plate and remove impeller base plate
from the pump body.
!
Using a mild detergent solution and a soft cloth, clean
deposits from screen, around impeller and base plate.
!
Spin impeller to dislodge any remaining foreign material.
!
Remove any foreign material in the hose adapter (between
the pump and hose), or between the hose and the water
distributor assembly.
!
Rinse and reinstall impeller base plate.
!
Reinstall pump and reconnect pump cord.
Draining
Drain the cooler (with power off and pads removed) as follows:
!
Connect a drain hose to the drain fitting on the bottom of the
reservoir, if not already connected to drain line.
!
Remove overflow standpipe from the drain fitting.
!
Drain and clean reservoir (never drain water onto a roof,
mineral build-up or damage to roof may occur).
Touch-Up
The hardness, adhesion and smoothness of the internal and external
finish on your cooler makes it extremely unlikely that scratches or
chipping will occur. In the event that finish damage does occur, it
should be promptly repaired by the following procedures:
1.
Sand the area around bare metal spots.
2.
Prime and paint with a quality paint.
Do not use asphalt type cooler undercoat material in water
reservoir.
Undercoat will break free, clogging the pump and
water distributor.
Lubrication
Motor Bearings
Some of the 3/4 & 1 Hp, single phase motors used in Industrial /
Commercial coolers have ports for lubricating the motor and are oiled
at the factory. If the need for oiling is indicated, see individual motor
nameplate for specific instructions on re-lubricating the motor. Under
normal use, these motors require oiling about every 12 months of
operation.
Do Not Over-Oil
.
The larger Hp motors use ball bearings and are permanently
lubricated and do not require lubrication.
(see page 4 for detailed steps).
6 UL Classified Industrial / Commercial Evaporative Cooler Use and Care Manual