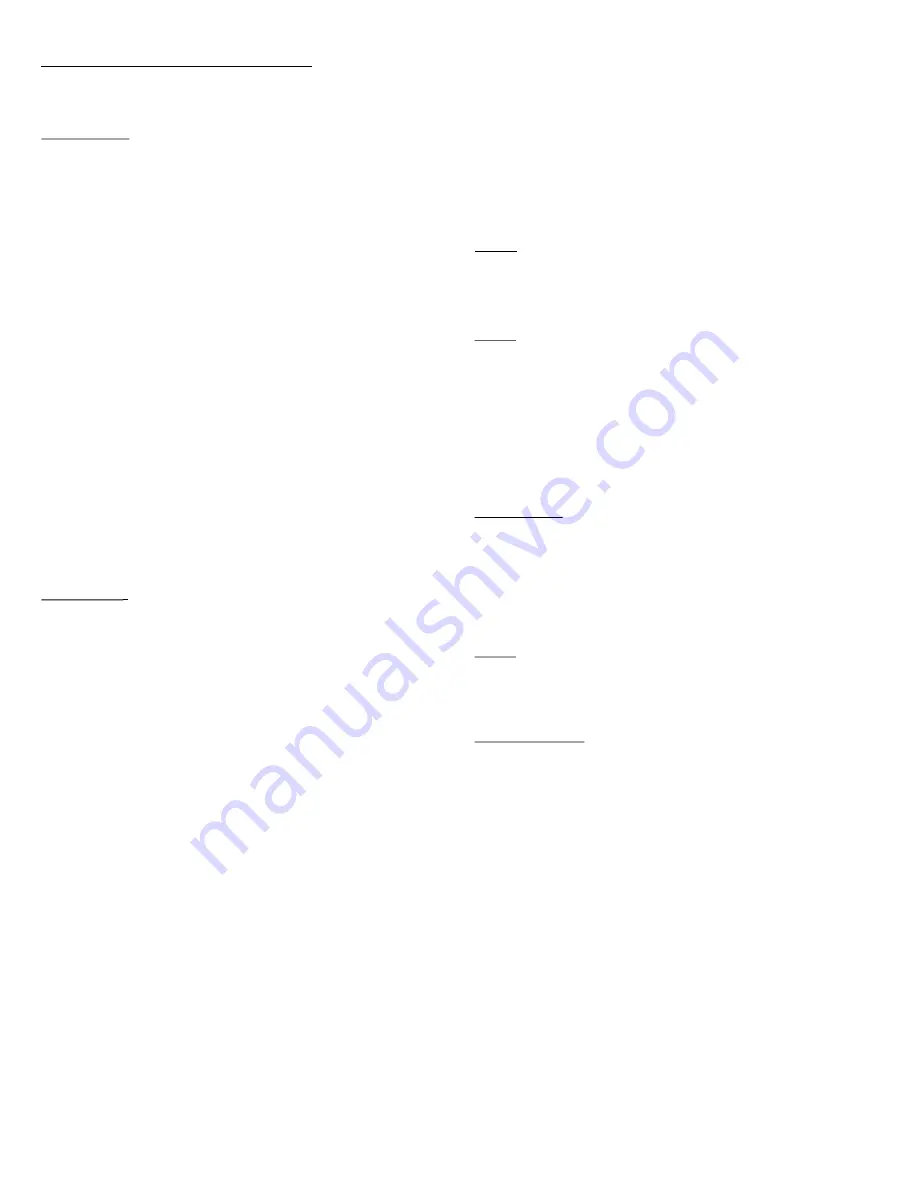
Maintenance Schedule
Regular maintenance and periodic inspection is the key to long and
successful service from your Industrial / Commercial Cooler. The
cooler should receive major servicing at least once a year, more often
if conditions require (dusty environment, constant use, poor water
quality, etc.) For maximum cooling efficiency, long life and
appearance, every two months during operation, the cooler should be
inspected and cleaned.
NOTE: Do Not Undercoat the Water Reservoir
Your cooler's water reservoir is finished with our Peblar XT®
appliance-type finish. It is so hard that asphalt-type cooler water pan
under-coatings will not stick to it. Undercoating will break free,
clogging the pump and water distribution system.
NOTE: Do not use cooler cleaners, cooler treatments, anodes or
other chemical additives in this evaporative cooler. Use of any
additives or water treatment other than the furnished bleed-off will
void your warranty and may impair the life of the cooler.
Before starting any maintenance operation, thoroughly read all
operating and maintenance instructions and observe all
cautions and warnings.
Cleaning
CAUTION:
Never wash your cooler cabinet with a
garden hose; water may harm motor and pump or seep
into ductwork. Motors damaged by water are NOT
covered under warranty.
All foreign materials, mineral scale, hard water deposits, dirt, etc.
should be removed from pad frames, water pan and other
components. Your cooler's long lasting finish can be brought to like-
new condition by using warm water and a soft cloth.
NOTE: Avoid using scouring pads, steel wool or wire brushes, as
these will damage the finish and encourage corrosion.
Maintenance & Inspection
IMPORTANT:
Before operating cooler at the beginning
of each cooling season, turn blower wheel, cooler motor
and pump motor shafts by hand to make sure they turn
freely. Failure to do so may result in burning out motor.
Periodic inspection of your Industrial Cooler will enhance the chance
for long, trouble-free service life. For maximum efficiency, every two
months during operation, or any time the cooler is opened, the cooler
should be inspected. Some suggested items to look for:
[
Check for leaks from pad frames, cabinet, etc.
[
Any dry spots or streaks on pads when pump is operating?
[
Are bolts, nuts and set screws still snug?
[
Are the bearings, etc., making any unusual noises?
[
Does the blower wheel turn freely?
[
Is float level set correctly?
[
Is water in the bottom pan clean?
[
Belt condition / tension / alignment OK?
Set Screws, Bolts and Nuts
Check torque on setscrews and cabinet hardware:
[
Motor and Blower Pulley set screws (95 in-lbs.)
[
Blower Wheel set screws (1 per side, 150 in-lbs)
[
Cabinet hardware (25 in-lbs)
GENERAL INSPECTION
Initial Start-up or Annual Inspection
CAUTION:
Disconnect all electrical power to the cooler
before attempting to install, open, or service your cooler.
More than one disconnect will be required to de-energize
the equipment for servicing. If the cooler is
thermostatically controlled, the thermostat is not to be
used as the power supply disconnect, as it may reset and
start the unit unexpectedly.
Before start-up the cooler for the first time, or at the beginning of each
cooling season, make sure that all required connections,
adjustments, etc. have been made. Verify that:
[
Cooler mounting is level; ductwork is sealed.
[
Cabinet is securely fastened to mounting.
[
Cooler cabinet is properly grounded. Electrical connections
are correctly made, safe and secure.
[
Motor, pump(s), drain, bleed-off, float valve, etc. are
correctly installed and fully functional.
[
Water line securely connected, turned on, no leaks noted.
[
Float adjusted for proper water level.
[
Pump impeller turns free and smooth. If in doubt, remove
impeller cover (see “Cleaning Pump”) and check rotation.
[
Blower wheel, shaft, pulley and motor sheave bolts /
setscrews are tight.
[
Motor sheave / Blower pulley alignment okay; belt correctly
tensioned, blower wheel turns freely.
Start-up Check List
CAUTION
: Never operate cooler with pad frames
removed. This will result in an overloaded condition and
may damage the blower motor.
To verify and check out the cooler installation on initial or annual start-
up, the following procedure should be followed.
[
Turn electrical supply to pump(s) on.
[
Verify that pump(s) starts and pads are evenly wet.
[
Open building exhaust / relief vents (windows, doors, etc.)
[
Turn electrical supply to blower motor on.
[
Observe that motor starts and runs, check each speed
(where applicable) and confirm air delivery.
[
Verify motor amperage does not exceed nameplate.
In case of trouble on any of these steps, refer to the Troubleshooting
Chart on
Cabinet Inspection Checklist
After initial start-up and for a few weeks afterwards, check for and/or
observe the following: Refer to the Troubleshooting Chart on
f
necessary.
[
Leaks from water lines, pad frames, cabinet, etc.
[
Cooler pads: even wetting, no dry streaks.
[
Confirm water level depth setting is correct.
[
Verify full, even flow in water distribution system.
[
Blower wheel / motor rotates freely, no unusual noises.
[
Belt condition / tension / alignment OK.
[
Check motor mounting, cabinet hardware, setscrews on
pulleys, blower wheel are tight
page 8.
page 8 i
UL Classified Industrial / Commercial Evaporative Cooler Use and Care Manual 5