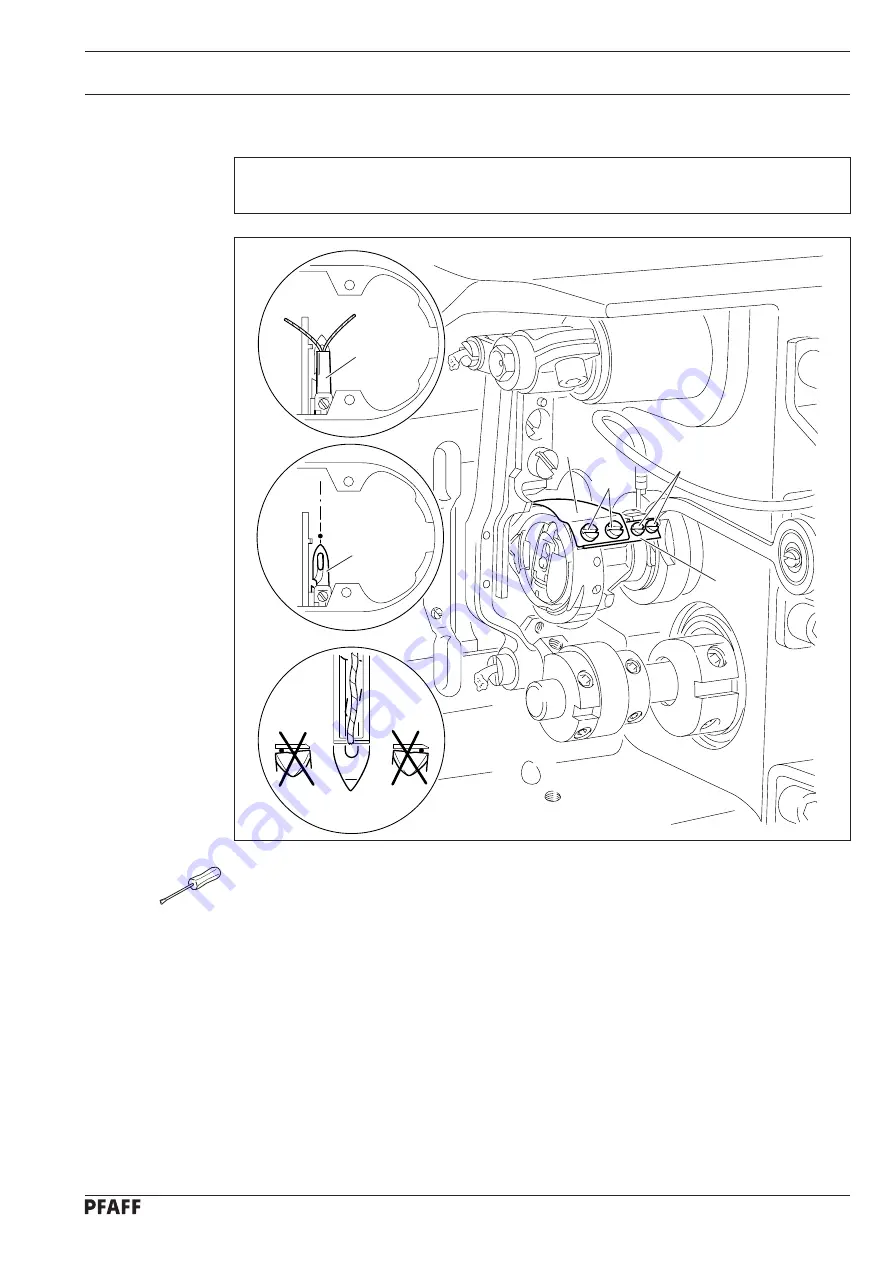
Adjustment
13 - 43
49-106
49-109
49-108
49-107
1
2
5
4
3
1
Fig.13 - 41
13
.06.12
Manual trimming control
Requirement
Both threads have to be cut perfectly in the catcher cutout on both right and left-hand side.
●
Position the needle bar at b.d.c and activate the engaging lever manually.
●
Turn the hand wheel until thread catcher
1
is its front reversal point.
●
Double a thread and insert it into the cutout of thread catcher
1
.
●
Turn the hand wheel further until the trimming process is finished.
●
If both threads are not trimmed in accordance with the
requirement,
loosen screws
2
and align thread catcher
1
with respect to knife
3
.
●
Make sure that the tip of the thread catcher is pointing to the centre of the needle and
tighten screws
2
firmly.
●
Move catcher stop
4
onto thread catcher
1
and tighten screws
5
firmly.
●
Screw on feed dog and needle plate, making sure that the movement of the feed dog in
the needle plate cutout is not restricted.
Содержание 3822-2/42
Страница 147: ...15 3 91 191 494 95 Page 1 Version 01 09 05 Circuit diagrams...
Страница 148: ...15 4 Circuit diagrams Version 01 09 05 91 191 494 95 Page 2...
Страница 149: ...15 5 91 191 494 95 Page 3 Version 01 09 05 Circuit diagrams PFAFF PFAFF PFAFF PFAFF PFAFF...
Страница 150: ...15 6 Circuit diagrams Version 01 09 05 91 191 494 95 Page 4...
Страница 151: ...Notes...