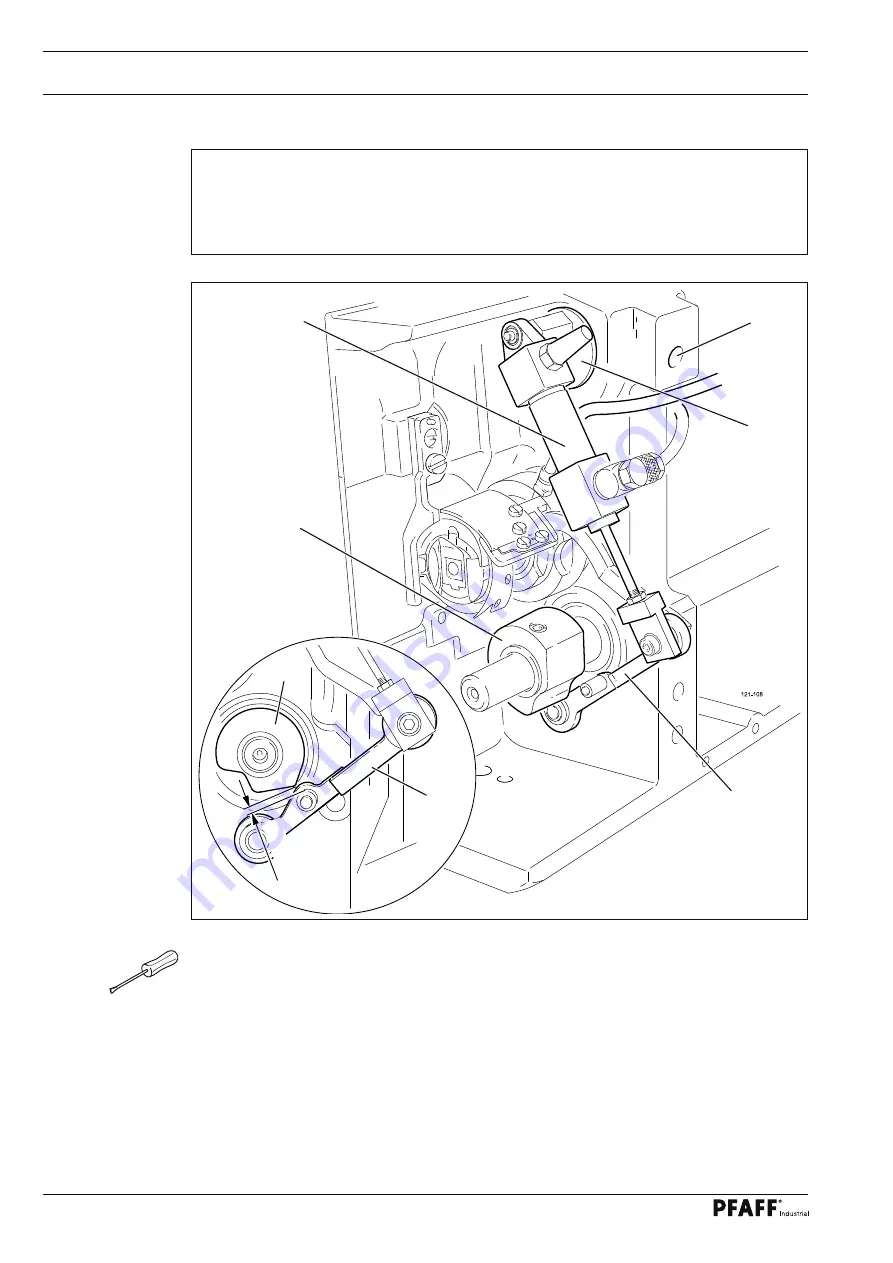
Adjustment
78
13
.06.02
Adjusting the roller lever
Requirement
When cylinder
1.
3
is fully extended, the roller of roller lever
4
should be
0.1 mm
away
from the highest point of control cam
5.
Cylinder
2.
3
should be parallel to the front edge of the bed-plate.
Adjust or turn eccentric
●
1
(screw
2)
in accordance with the
requirements
.
50-65a
5
4
0,1 mm
Fig. 13 - 11
5
3
1
2
4
Содержание 3519-4/01
Страница 38: ...Sewing 38 Double pointed darts Fig 10 02 0 320 mm 0 320 mm Insertion marking Insertion marking...
Страница 142: ...142 Pneumatics switch diagram Version 14 06 06 91 744 699 95 Part 6...
Страница 150: ...150 Circuit diagram Version 10 07 08 91 191 499 95 Part 1...
Страница 151: ...151 91 191 499 95 Part 2 Version 30 03 06 Circuit diagram...
Страница 152: ...152 Circuit diagram Version 30 03 06 91 191 499 95 Part 3...
Страница 153: ...153 91 191 499 95 Part 4 Version 11 02 11 Circuit diagram...
Страница 154: ...154 Circuit diagram Version 30 11 05 91 191 499 95 Part 5...
Страница 155: ...155 91 191 499 95 Part 6 Version 10 07 08 Circuit diagram...
Страница 156: ...156 Circuit diagram Version 30 03 08 91 191 499 95 Part 7...
Страница 157: ...157 91 191 499 95 Part 8 Version 01 10 08 Circuit diagram...
Страница 158: ...158 Circuit diagram Version 30 03 06 91 191 499 95 Part 7...
Страница 159: ...159 91 191 499 95 Part 8 Version 07 07 06 Circuit diagram...