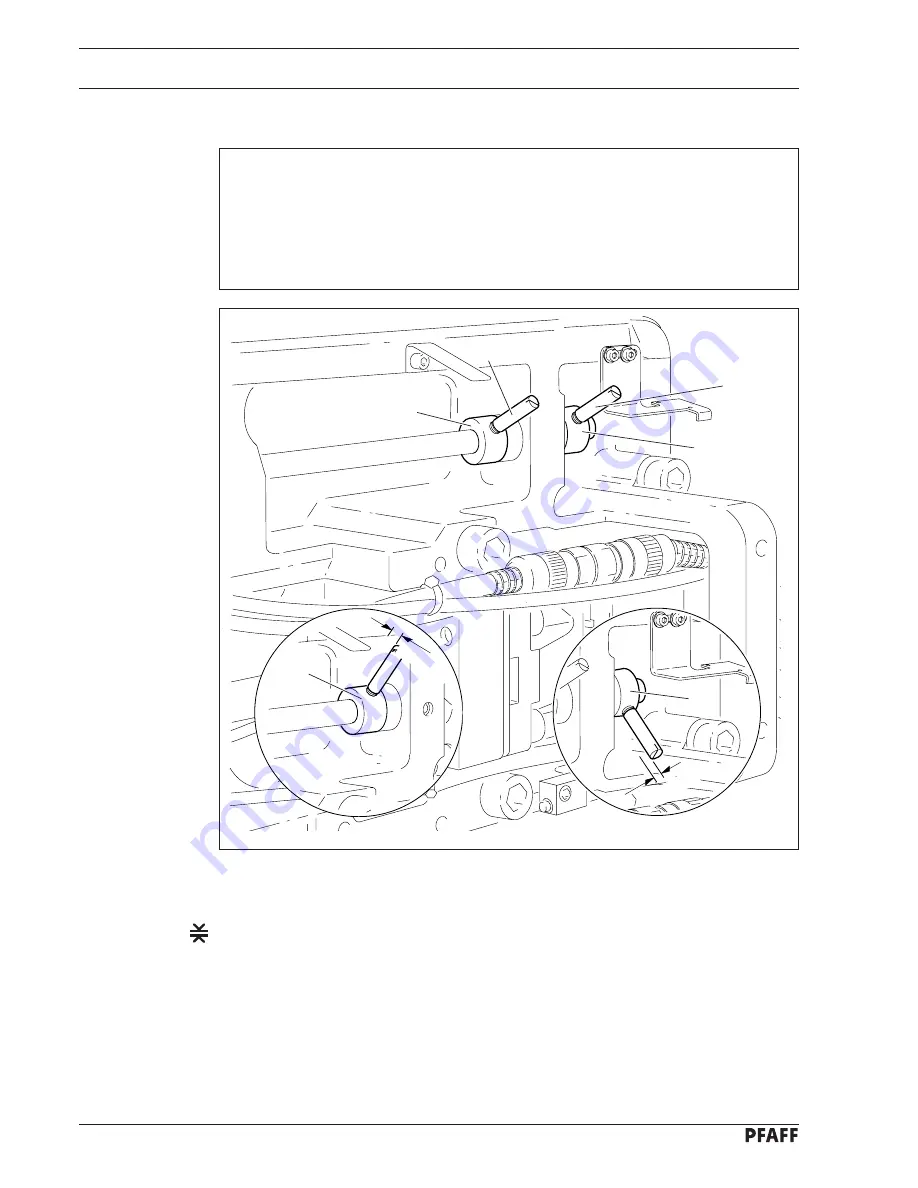
Adjustment
13 - 18
13
.05.16
Mechanical limiting of the stitch length
Requirement
1. The maximum stitch length should be 2.5 mm, but the needle should not touch the
needle plate cutout when sewing forwards or in reverse.
2. When the maximum stitch length is set, when sewing forwards the screws of stop
1
and when sewing in reverse the screws of stop
3
should each have a clearance of
0.3 mm
to the corresponding metal edge.
Fig. 13 - 15
●
Switch on the machine and set parameter 849 in accordance with
requirement 1
, see
Chapter 13.11 Parameter settings.
●
Select the maximum stitch length on the control panel.
●
Adjust stop
1
(screw
2
) in accordance with
requirement 2.
●
Press the key on the machine head and sew 2 stitches (in reverse).
●
Adjust stop
3
(screw
4
) in accordance with
requirement 2.
●
Switch off the machine.
1
2
3
4
89-036
0,3 mm
89-035
0,3 mm
1
3
Содержание 2483-980/31
Страница 109: ...15 2 2483 980 Version27 01 03 Overview ...
Страница 110: ...15 3 Circuit diagram Version 29 01 02 91 191 454 95 Part 1 ...
Страница 111: ...15 4 91 191 454 95 Part 2 Version 29 01 02 Circuit diagram ...
Страница 112: ...15 5 Circuit diagram Version 29 01 02 91 191 454 95 Part 3 ...
Страница 113: ...15 6 91 191 454 95 Part 4 Version 29 01 02 Circuit diagram ...