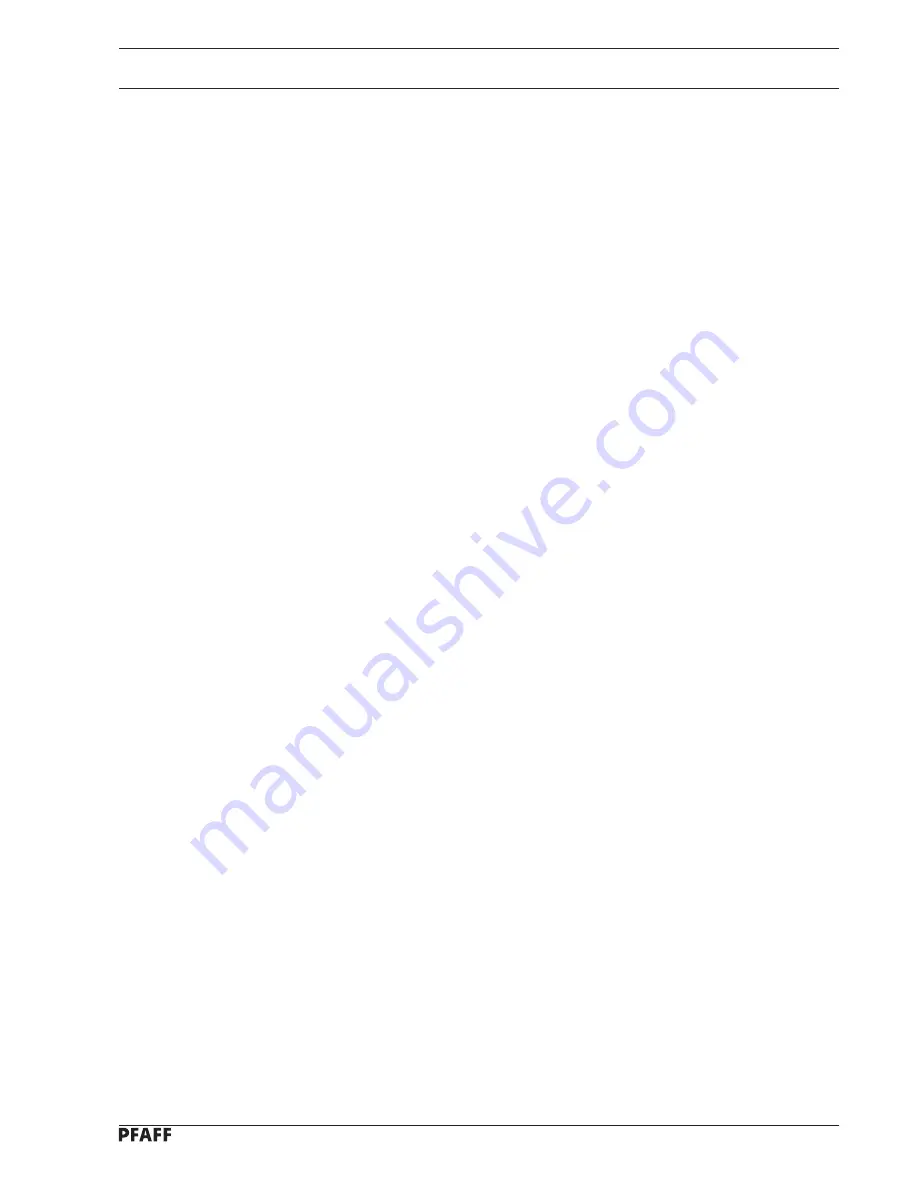
Index
Contents ............................................................................... Chapter - Page
11
.15.01
Example of seam programming ........................................................................... 11 - 18
0
11
.15.02
Example for programming a decorative seam ..................................................... 11 - 28
0
11
.15.03
Example of Teach In programming ...................................................................... 11 - 31
0
12
Care and maintenance ......................................................................................... 12 - 1
0
12
.01
Cleaning ................................................................................................................. 12 - 1
0
12
.02
Lubricating the hook .............................................................................................. 12 - 2
0
12
.03
Filling the oil reservoir ............................................................................................ 12 - 2
0
12
.04
Lubricating the bevel gears .................................................................................... 12 - 3
0
12
.05
Filling the oil reservoir of the thread lubricator ....................................................... 12 - 4
0
12
.06
Cleaning the air filter on the control box ................................................................ 12 - 4
0
13
Adjustment ........................................................................................................... 13 - 1
0
13
.01
Notes on adjusting ................................................................................................. 13 - 1
0
13
.02
Tools, gauges and other adjustment aids .............................................................. 13 - 1
0
13
.03
Abbreviations ......................................................................................................... 13 - 1
0
13
.04
Adjusting the basic machine .............................................................................. 13 - 2
0
13
.04.01
Adjusting the synchronizer ..................................................................................... 13 - 2
0
13
.04.02
Setting the machine configuration ......................................................................... 13 - 4
0
13
.04.03
Positioning the needle in the direction of sewing (1471E1) ................................... 13 - 5
0
13
.04.04
Needle bar frame limitation (1471E1 only) ............................................................. 13 - 6
0
13
.04.05
Positioning the needle in the direction of sewing (1474E1) ................................... 13 - 7
0
13
.04.06
Preadjusting the needle height .............................................................................. 13 - 8
0
13
.04.07
Needle rise, hook-to-needle clearance, needle height and needle guard (1471E1) 13 - 9
0
13
.04.08
Needle rise, hook-to-needle clearance, needle height and needle guard (1474E1) 13 - 11
13
.04.09
Needle setting in transverse direction to sewing (1471E1) .................................... 13 - 13
13
.04.10
Needle setting in transverse direction to sewing (1474E1) .................................... 13 - 14
13
.04.11
Bobbin case opener height .................................................................................... 13 - 15
13
.04.12
Bobbin case opener stroke .................................................................................... 13 - 16
13
.04.13
Feed wheel height (1471E1) .................................................................................. 13 - 17
13
.04.14
Feed wheel height (1474E1) .................................................................................. 13 - 18
13
.04.15
Clearance between roller-presser and feed wheel ................................................. 13 - 19
13
.04.16
Roller-presser ......................................................................................................... 13 - 20
13
.04.17
Holding-down clamp (1474E1 only) ........................................................................ 13 - 21
13
.04.18
Automatic presser-foot lifter .................................................................................. 13 - 22
13
.04.19
Knee lever .............................................................................................................. 13 - 23
13
.04.20
Tension release ...................................................................................................... 13 - 24
13
.04.21
Thread check spring(1471E1) ................................................................................. 13 - 25
13
.04.22
Thread check spring(1474E1) ................................................................................. 13 - 26
13
.04.23
Bobbin winder ........................................................................................................ 13 - 27
13
.04.24
Roller-presser pressure .......................................................................................... 13 - 28
13
.05
Adjusting the edge trimmer -725/04 for the 1471E1 ......................................... 13 - 29
13
.05.01
Position of the knife carrier .................................................................................... 13 - 29