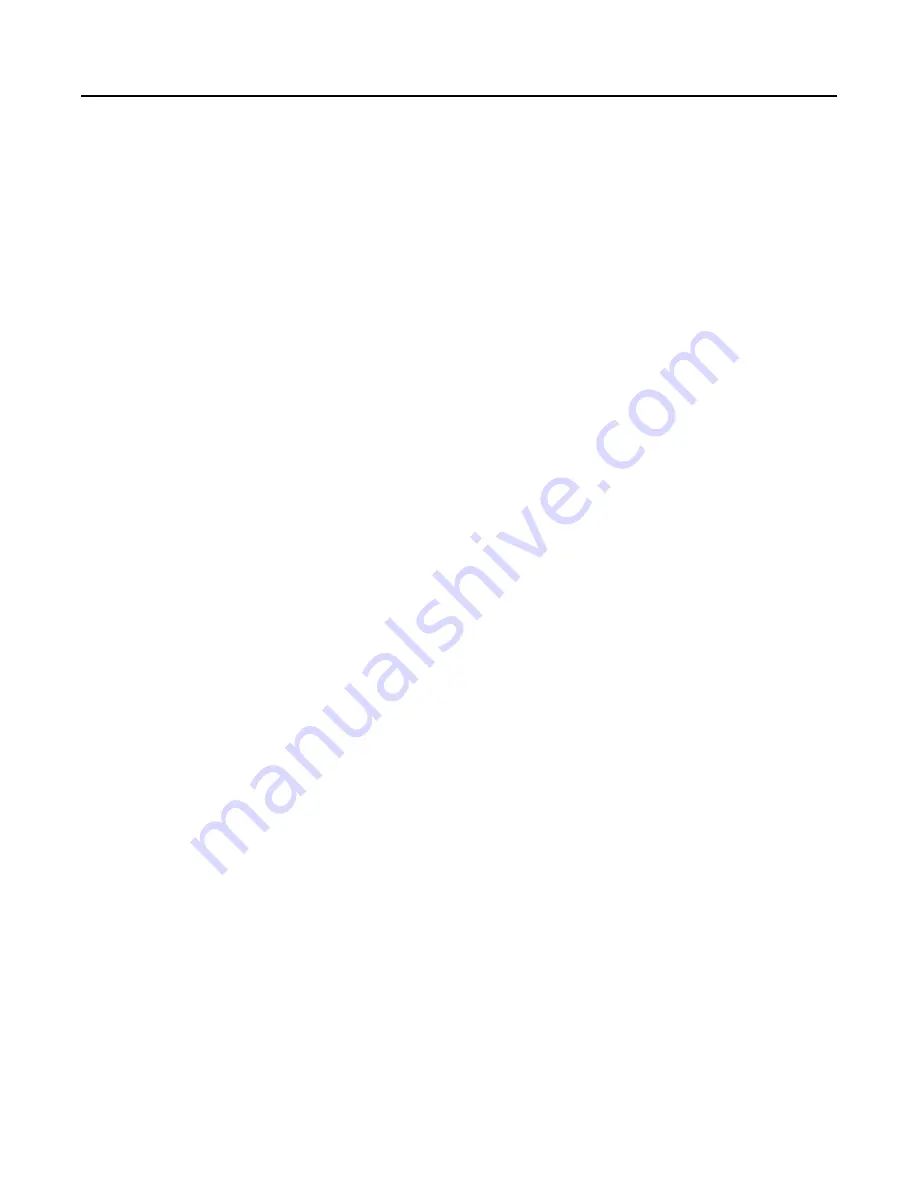
“ Speed Sensor - Clean/Inspect“. . . . . . . . . . . . . . . 82
Every 3000 Service Hours or 2
Years
“ Cooling System Coolant - Change“ . . . . . . . . . . . 63
Every 6000 Service Hours or 3
Years
“ Cooling System Coolant (ELC) - Change“ . . . . . . 61
Every 7500 Service Hours
“ Alternator - Inspect“ . . . . . . . . . . . . . . . . . . . . . . . . 56
“ Engine Oil Pump - Inspect“ . . . . . . . . . . . . . . . . . . 70
“ Fuel Injector - Inspect/Adjust“ . . . . . . . . . . . . . . . . 75
“ Fuel Transfer Pump (Lift Pump) - Inspect“ . . . . . . 78
“ Starting Motor - Inspect“ . . . . . . . . . . . . . . . . . . . . 84
“ Turbocharger - Inspect“ . . . . . . . . . . . . . . . . . . . . . 84
“ Water Pump - Inspect“. . . . . . . . . . . . . . . . . . . . . . 85
Every 20 000 Service Hours
“ Overhaul (Major)“. . . . . . . . . . . . . . . . . . . . . . . . . . 79
“ Overhaul (Top End)“ . . . . . . . . . . . . . . . . . . . . . . . 80
Commissioning
“ Actuator Control Linkage - Lubricate“. . . . . . . . . . 55
“ Alternator - Inspect“ . . . . . . . . . . . . . . . . . . . . . . . . 56
“ Alternator Pulley - Check“ . . . . . . . . . . . . . . . . . . . 56
“ Belts - Inspect/Adjust/Replace“. . . . . . . . . . . . . . . 59
“ Belts - Inspect/Adjust/Replace“. . . . . . . . . . . . . . . 58
“ Cooling System Coolant Level - Check“. . . . . . . . 66
“ Driven Equipment - Check“ . . . . . . . . . . . . . . . . . . 66
“ Engine Crankcase Breather - Clean“ . . . . . . . . . . 68
“ Engine Mounts - Inspect“ . . . . . . . . . . . . . . . . . . . 69
“ Engine Oil Level - Check“ . . . . . . . . . . . . . . . . . . . 70
“ Engine Protective Devices - Check“ . . . . . . . . . . . 73
“ Fan Drive Pulley - Check“ . . . . . . . . . . . . . . . . . . . 74
“ Fuel System - Prime“ . . . . . . . . . . . . . . . . . . . . . . . 75
“ Fuel Tank Water and Sediment - Drain“ . . . . . . . . 77
“ Jacket Water Heater - Check“ . . . . . . . . . . . . . . . . 79
“ Severe Service Application - Check“ . . . . . . . . . . 82
“ Walk-Around Inspection“ . . . . . . . . . . . . . . . . . . . . 84
50
SEBU8604-02