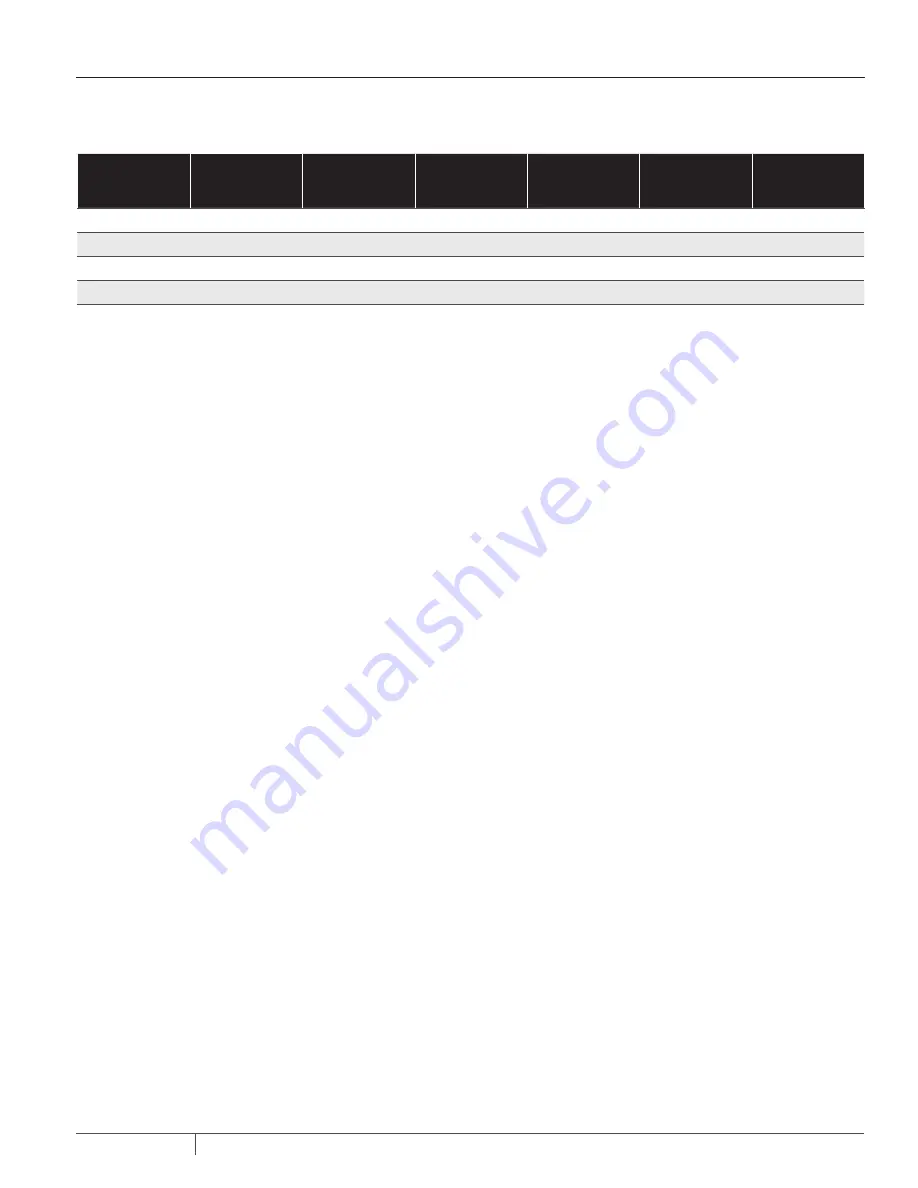
9
PN524 (08-01-20)
GENERAL SERVICE
When installed in a clear well and operated under normal
conditions, the submersible turbine pump requires no special
maintenance. The hermetically sealed motor is pre-filled and
self-lubricating. Completely tested at the factory, it should
provide many years of dependable ser vice. The motor is a
continuous duty type and can operate continuously for long
periods.
REMOVING PUMP FROM WELL
Most pump problems are caused by above-ground elec trical
problems. Minor control box components or outside electrical
difficulties (such as low voltage) can cause a mal function.
Before removing pump from well, check motor windings for
damage (check winding resistance with an ohmmeter – see
Page 7). Eliminate all above-ground trouble causes before
pulling pump. Pull the pump only as a last resort.
SANDLOCKED PUMP
NOTICE:
Before pulling pump, make all possible above ground
electrical tests. Most submersible pump problems are above
ground, not in the pump itself.
NOTICE:
Motor failure can result from starting a sand locked
pump. Do not bypass overload circuit or exceed electrical
rating when trying to start a siezed pump.
Remove a sandlocked pump from well for cleaning. To prevent
pump from locking again when reinstalled, clean the well
thoroughly before reinstalling the pump.
SERVICE
CLEANING SANDLOCKED PUMP
1. Insert a reducing bushing in discharge adapter cap to
receive a hose coupling.
2. Use a hose to flush pump backwards (discharge to suction).
Oscillate shaft backwards and forwards with a pump pliers
and backwash pump for several minutes.
CHECKING PUMP PERFORMANCE
Water containing abrasives can cause impeller wear and reduce
impeller efficiency, resulting in overload conditions. In such
cases, it is necessary to remove the pump from the well and
replace the impellers to maintain capacity and pressure. To
assure quality and integrity of the unit, have your pump serviced
by authorized Berkeley personnel.
SERIES
INLET SHAFT
SPACER
KEY NO. 19
THRUST SHAFT
SPACER
KEY NO. 15
DISTANCE SLEEVE
KEY NO. 10
STAGE SPACER
KEY NO. 10
DISCH. SHAFT
SPACER KEY NO. 7
BEARING
JOURNAL
KEY NO. 6
115
3.738 (89.30)
1.356 (34.44)
2.896 (73.56)
4.37 (111.00)
0.620 (15.74)
1.749 (44.40)
155
3.687 (93.65)
1.407 (35.74)
2.845 (72.28)
4.37 (111.00)
0.671 (17.04)
1.749 (44.40)
230
3.789 (96.24)
1.295 (32.90)
2.957 (75.10)
4.37 (111.00)
0.577 (14.66)
1.749 (44.40)
300
3.967 (100.75)
0.860 (21.85)
3.3917 (86.15)
4.37 (111.00)
0.400 (10.16)
1.749 (44.40)
Table VI: 6TS-Mixed Flow Shaft Spacer and Bearing Journal Lengths in Inches (mm)
(See Exploded View, Page 14)