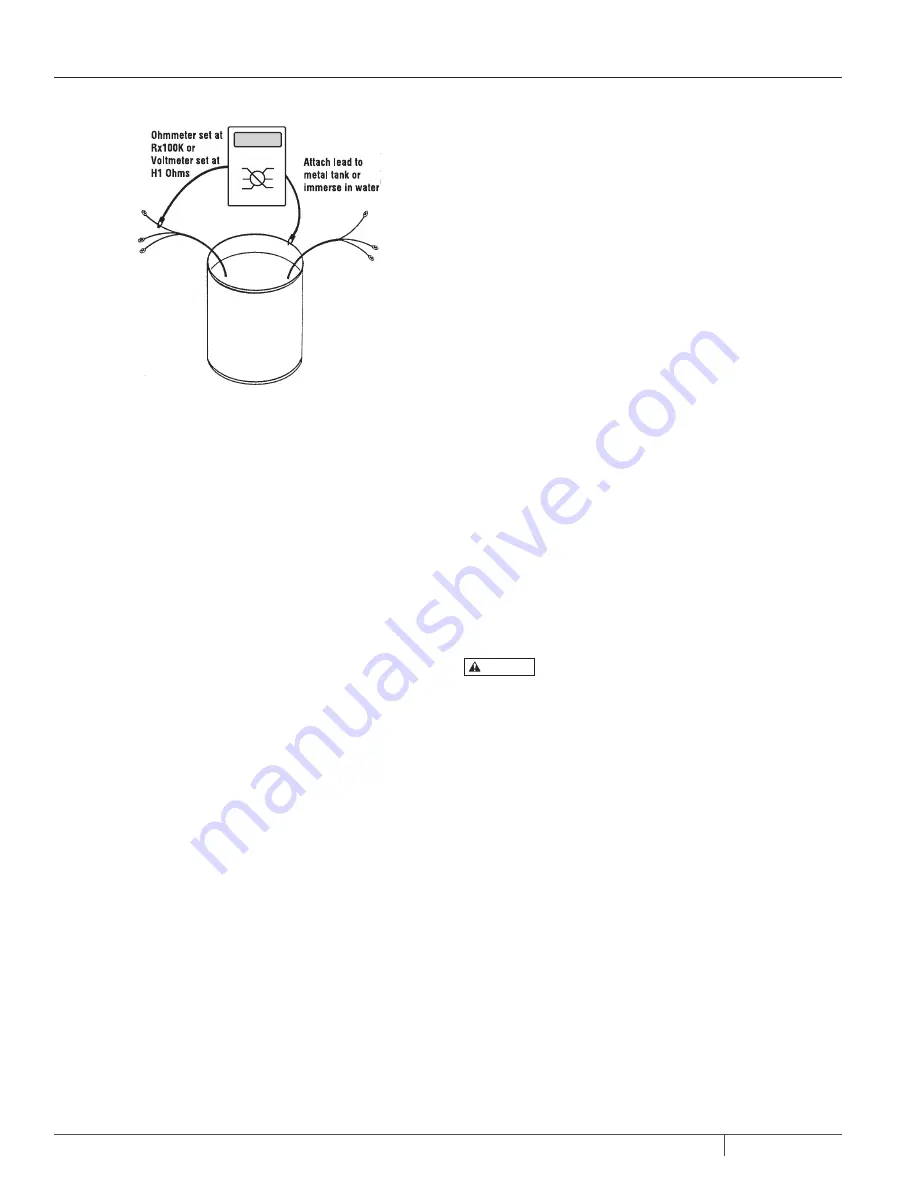
6
PN524 (08-01-20)
INSTALLATION
ROTATION CHECK (3-PHASE ONLY)
After satisfactorily completing continuity test, connect cable
to pump controller. Check 3-phase motors for correct rotation.
If necessary, reverse any two cable leads at the controller
and recheck rotation. Permanently mark and match to control
box terminals for future reference. Connect cable to motor
controller and then wire controller to disconnect switch.
Connect temporary jumper wire between proper terminals in
controller to temporarily energize magnetic coil.
Momentarily engage disconnect switch and note direction of
rotation. The shaft should rotate counterclockwise when viewed
from the top or shaft end of the motor. If rotation is incorrect,
reverse any two wires; mark wires to correspond with the
controller terminal numbers.
NOTICE:
Pump is water lubricated. Do not operate the pump for
more than 5 seconds while it is out of water.
GENERAL INSTALLATION
After completing all connections and tests so far, connect a
5-foot length of pipe to pump.
Lower pump into well with pipe clamps attached to the 5-foot
pipe. Attach a standard length of pipe to 5-foot length and lower
pump CAREFULLY into well.
NOTICE:
Do not use a pipe longer than 5 feet for the first
con nection. Hoisting pump upright with a long length of pipe can
cause pump misalignment from excessive leverage.
CAUTION
Use extreme care when lowering pump and cable
to avoid damage to cable insulation.
Anchor power cable to pipe every 20 feet with adjustable steel
band clamps. Protect insulation from clamps with pieces of split
rubber hose inserted between clamps and cable. Attach cable to
pipe halfway between clamps with waterproof tape (Scotch No.
33 or equivalent).
SUBMERGENCE
Be sure the pump is always submerged, even at extreme
pumping rates. Install pump at least 10 to 20 feet below the
lowest “drawdown” water level and at least 5 feet above bottom
of well.
CHECK VALVES
Pump back spin and hydraulic shock can cause severe damage
to the pump and motor. Install at least one check valve in the
discharge pipe (riser pipe) to help prevent this.
Install the first check valve in the pump discharge or in the
discharge pipe it self, not more than 25’ above the pump. Install
another check valve not more than 200 feet above the first one.
Repeat, all the way up the riser pipe. The last check valve on the
Figure 1C: Splice and Cable Continuity
SPLICE AND CABLE CONTINUITY TEST
Before installing pump check cable and splices as follows
(see Figure 1C):
1. Submerge cable and splice in steel barrel filled with water.
Make sure both ends of cable are out of water.
2. Clip one ohmmeter lead to barrel. Test each lead in cable
successively by connecting the other ohmmeter lead to the
three cable leads, one after the other.
3. If resistance reading goes to zero on any cable lead, a
leak to ground is present. Pull splice out of water. If meter
reading changes to “infinity” (no reading) the leak is in the
splice.
4. If leak is not in splice, slowly pull cable out of water until
reading changes to “infinity”. Reading will change to
“infinity” when leak comes out of water.
5. Repair cable by splicing as explained under “Electrical
Splices and Connections”.