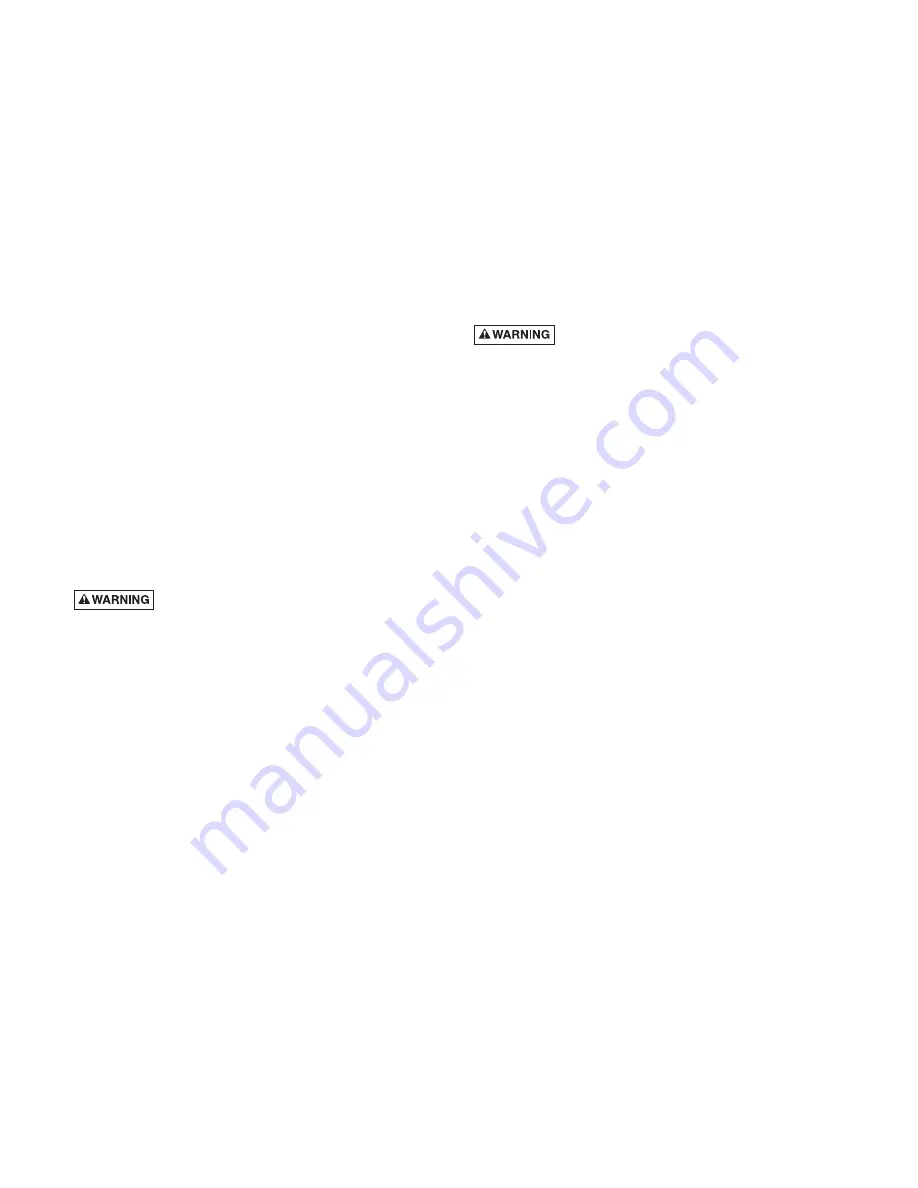
3
INSTALLATION
Only qualified, licensed personnel should install pump and
wiring.
Pump mount must:
Be located away from corrosive or flammable liquids.
Have enough ventilation to maintain air temperature at less
than the maximum ambient temperature rating (Max. Amb.)
listed on the motor model plate. If this pump is installed in
an enclosure/pump house, the enclosure must have
adequate ventilation and air circulation to keep the
temperature in the enclosure at or below the motor’s rated
ambient temperature whenever the pump is running.
Be solid - level - rigid - vibration free. (To reduce vibration
and pipe stress, bolt pump to mount).
Allow pump suction inlet height to be as close to water level
as possible.
Allow use of short, direction suction pipe (to reduce friction
losses).
Allow for gate valves in suction and discharge piping.
Have adequate floor drainage to prevent flooding.
Be protected from excess moisture.
Allow adequate access for servicing pump and piping.
NOTICE: Support all piping connected with pump!
Fire and burn hazard.
Modern motors run at
high temperatures. To reduce the risk of fire, do not allow
leaves, debris, or foreign matter to collect around the pump
motor. To avoid burns when handling the motor, let it cool
for 20 minutes before trying to work on it.
Piping:
Use at least 1-1/2" IPS PVC pipe with 5" trap. Use at least
2" pipe with 6" trap. Increase size if a long run is needed.
To avoid strains on the pump, support both suction and
discharge pipes independently. Place these supports near
the pump.
To avoid a strain left by a gap at the last connection, start all
piping at the pump and run pipe
away
from the pump.
Never use a suction pipe smaller than pump suction
connection.
To avoid airlocking, slope suction pipe slightly upward
toward the pump.
NOTICE:
To prevent flooding when removing pump for
service, all flooded suction systems
must
have gate valves in
suction and discharge pipes.
Fittings:
Fittings restrict flow; for best efficiency use fewest possible
fittings.
Avoid fittings which could cause an air trap.
Pool fittings must conform to International Association of
Plumbing and Mechanical Officials (IAPMO) standards.
Use only non-entrapping suction fitting or double suction.
POOL PUMP SUCTION
REQUIREMENTS
Pump suction is hazardous and can trap
and drown or disembowel bathers. Do not use or operate
swimming pools, spas, or hot tubs if a suction outlet
cover is missing, broken, or loose.
Follow the guidelines
below for a pump installation which minimizes risk to
users of pools, spas, and hot tubs.
Entrapment Protection
The pump suction system
must provide protection against
the hazard of
suction entrapment or hair entrapment/entanglement.
Suction Outlet Covers
All suction outlet covers must be maintained. They must
be replaced if cracked, broken, or missing.
See below for outlet cover certification requirements.
All suction outlets must have correctly installed, screw-
fastened covers in place.
Testing and Certification
Suction outlet covers must have been tested by a
nationally recognized testing laboratory and found to
comply with the latest ASME/ANSI Specification for
Suction Fittings For Use in Swimming Pools, Spas, Hot
Tubs, and Whirlpool Bathtub Applications.
Содержание Sta-Rite CF6 Series
Страница 11: ...11 ...