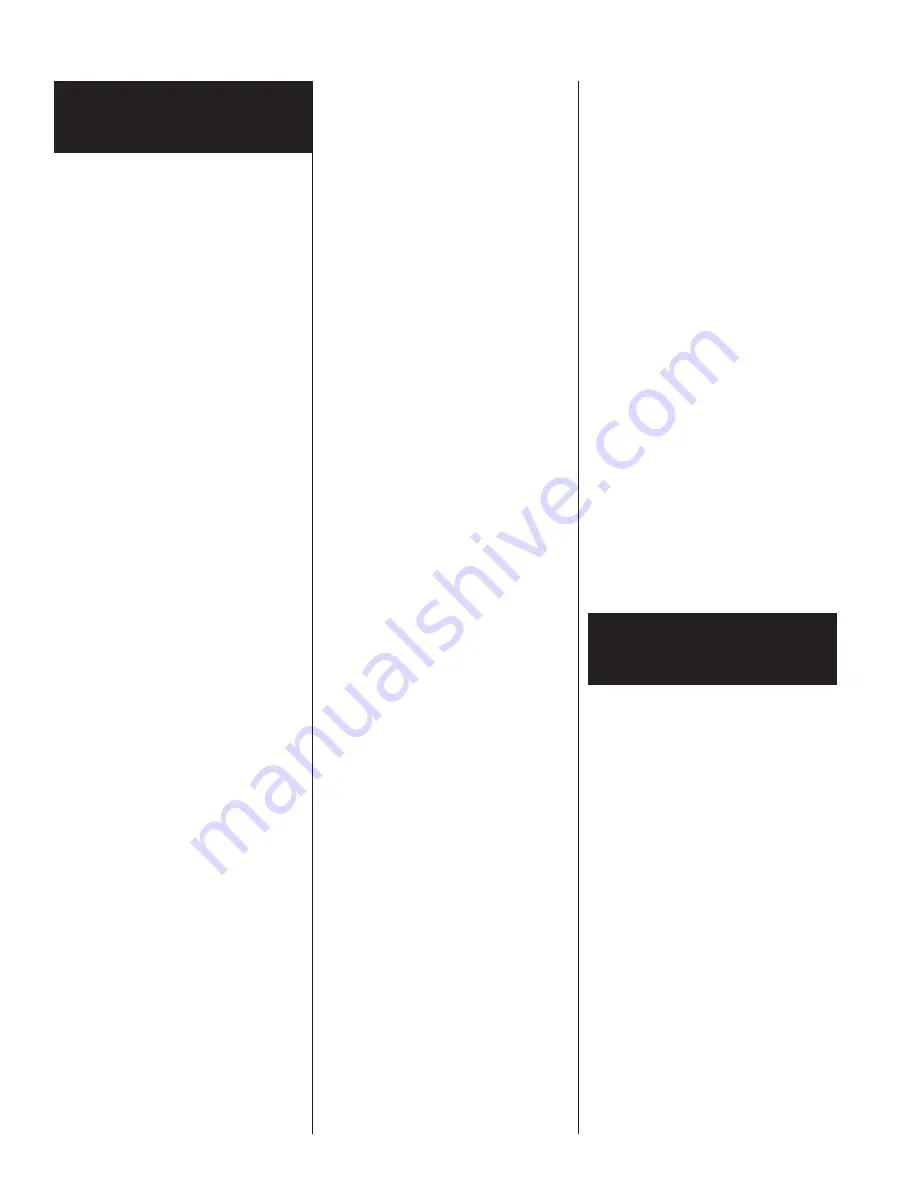
4
Pump
Servicing
electrical components of the
pump. Starting with the power
cord, inspect for cuts or nicks
in the insulation. If the cord is
damaged, it must be replaced!
9. Using the ohmmeter, check
the resistance of the motor
windings by connecting one
lead clip to each electric “flat”
prong on the power cord plug.
The ohmmeter should be on
R x 1 setting.
To check for ground, place the
ohmmeter on R x 100k,
connect one lead clip to the
“round” ground prong on
the power cord and touch the
other lead clip to each
“flat” prong individually. If
the reading is other than
infinity (
∞
on the ohmmeter
scale), a leakage through
stator insulation or moisture in
the windings is occurring and
the pump must be replaced.
WARNING: Before handling
these pumps and controls,
always disconnect the power
first.
Do not smoke or use sparkable
electrical devices or flames in a
septic (gaseous) or possible
septic sump
.
Pump does not run or hum.
1. Line circuit breaker may be
off, blown or loose.
2. Water level in sump may be
too low. Run in more water.
Turn on level is 12 to 13
inches above sump bottom.
3. Pump and/or switch cord plug
may not be making contact
in receptacle.
Read the following instructions
carefully before replacing any
parts. Reasonable care and safe
methods should be practiced.
Check local codes and
requirements before installation.
Only competent electrician
should make the installations.
Servicing should be performed
only by knowledgeable pump
service contractors or authorized
service stations.
1.
WARNING:
Always disconnect
the pump from power source
before handling or making any
adjustments. Always wear
rubber boots when there is
water on the floor and you
must unplug the pump.
2. Before removing pump from
sump for repair, check if the
trouble could simply be a
blown fuse, tripped circuit
breaker, or a power cord
not completely inserted into
the receptacle.
3.
NOTE:
Automatic thermal
overload protects the sealed-
in-oil motor. Running dry will
overheat the motor and
activate the overload protector
until the unit cools.
4. If the unit is being operated
by the optional float control or
diaphragm switch, unplug the
pump from the piggyback
receptacle and plug the pump
directly into the power source.
If the pump starts each time it
is plugged directly into the
receptacle and does not start
each time when plugged into
the piggyback switch with
the float raised up (or the
diaphragm switch pressed in)
to a start position, replace the
complete piggyback switch
assembly and retest with
new assembly.
5. If pump fails the above two
steps, unplug and pull the
pump from the sump by the
handle. Sandblast, if possible,
any dirt or trash from the
outside of the pump before
proceeding.
6. Check for an obstruction in the
impeller cavity by laying the
pump on its side and removing
the 5 screws (20) to remove
the plastic base (18 & 19). If
the impeller does not rotate
freely, clear the impeller
and cavity walls before
reassembling the base.
Repeat Step 4.
7.
Air Locking:
A sump pump is
said to be air locked if air traps
in the pump and it cannot get
out, thus preventing pump
from operation. Hydromatic
sump pumps have a small air
vent hole in the impeller cavity
to let out trapped air. If the
hole becomes plugged, pump
may air lock. To break the air
lock, use a small screwdriver
to clear the hole in the impeller
cavity. As a secondary
precaution in installations of
this type –
1
⁄
8
" hole should be
drilled in the discharge pipe
below the check valve.
The check valve should be
12 to 18 inches above pump
discharge. Do not put check
valve directly into pump
discharge opening.
NOTE: In sumps where the
pump is operating daily, air
locking rarely occurs.
8. If the above tests have not
resolved the problem, the
problem may be in the
Pump
Troubleshooting